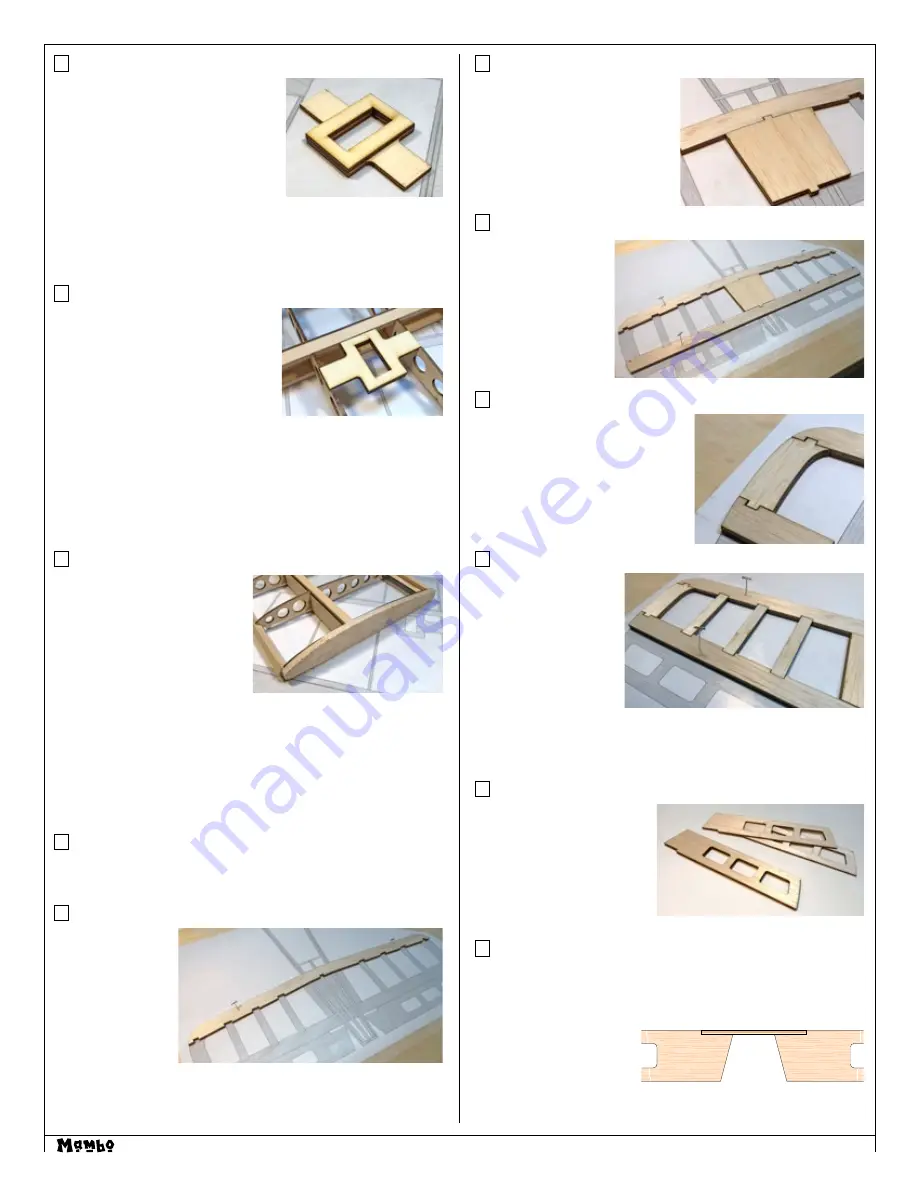
Construction Manual
www.oldschoolmodels.com
Page 7
Step 26 - Wing Assembly (aileron servo mount)
Cut into LP4 are the aileron servo
mounts. However there are two slightly
different sizes to help accommodate
the different brands servo sizes.
You’ll need one SM1 and one SM2 for
each aileron mount. The pieces that
are slightly larger are designed with
the etched circle.
Glue one SM2 to SM1 as shown here - making sure both pieces
either have an etched circle, or they both don’t (matched pairs).
Now do this again so you’ll have two matching aileron mounts.
Step 27 - Wing Assembly (aileron servo mount)
The aileron mount you just assembled
in the previous step is now glued into
place on the bottom of the wing, as
shown here.
Note that if you’re using the slightly
large SM1/SM2 pieces, it will only
properly fit when the longer edge
(designated by the etched circle) is orientated towards the trailing
edge of the wing.
Also note that SM1 should be flush with the wing’s surface, with
SM2 orientated inside the wing. (Refer to the photo.)
When satisfied with the fit and orientation, securely glue both
aileron mounts in position.
Step 28 - Wing Assembly (Tip)
Locate both of the TIP pieces
from BPTIP.
These are the wing tips and are
glued into place, up against the
outer R5 tip ribs.
Make sure each R5 is sanded flat
with no extra wood protruding,
then glue one TIP to each end.
You’ll need to make sure they are properly positioned as there
isn’t a guide to aid in this step. Also, these TIP pieces are slightly
oversized to give a bit of “wiggle-room”.
This completes assembly of the Mambo wing.
Now it’s time to start construction of the tail surfaces.
Prepare your work area
Now tape the horizontal stabilizer plan and a fresh piece of waxed
paper on your building board.
Step 29 - Horizontal Stab Assembly (S1)
Locate both S1’s
from BP1. These
are glued on top of
each other to form
a thicker S1. Make
sure they are exactly
aligned with each
other when gluing
them together.
Then pin them in place over the plan as shown here.
Step 30 - Horizontal Stab Assembly (S2)
Locate both S2’s from BP1. These
are glued together to form a
thicker S2, then glued to the
center of S1, as shown here.
Step 31 - Horizontal Stab Assembly (S3)
Locate both S3’s from
BP1. These are glued
together to form a
thicker S3, then glued
to the S2, as shown
here.
Step 32 - Horizontal Stab Assembly (S4)
Locate four S4’s from BP6 and BP7.
These are glued together to make a
pair of matching, thicker S4’s.
Then these S4’s are glue in place as
the stab’s tips as shown here - one
each end of the horizontal stab.
Step 33 - Horizontal Stab Assembly (S5, S6, and S7)
Locate four S5’s, four
S6’s and four S7’s from
BP1.
Glue two S5’s together
to make a thicker S5,
then do the same to
make a matching pair
of S5’s. Do the same for
the S6’s and S7’s.
These are now glued in place as shown, making sure they are firmly
seated in the pre-cut notches in S1 and S3.
Step 34 - Elevator Assembly (E1)
Locate four E1’s from BP1.
Glue two E1’s (perfectly
aligned on top of each other )
to form a thicker E1, then do
the same for the remaining
E1’s. This will give you the left
and right elevator halves.
Step 35 - Elevator Assembly (joiner)
Locate the 4” length of 3/32” dowel to create the elevator joiner.
Measure and trim it to the length as shown on the plans - roughly
3-1/4”.
Pin both elevator halves in
position, making sure they
are perfectly aligned with
each other, then securely
glue the elevator joiner
dowel place.