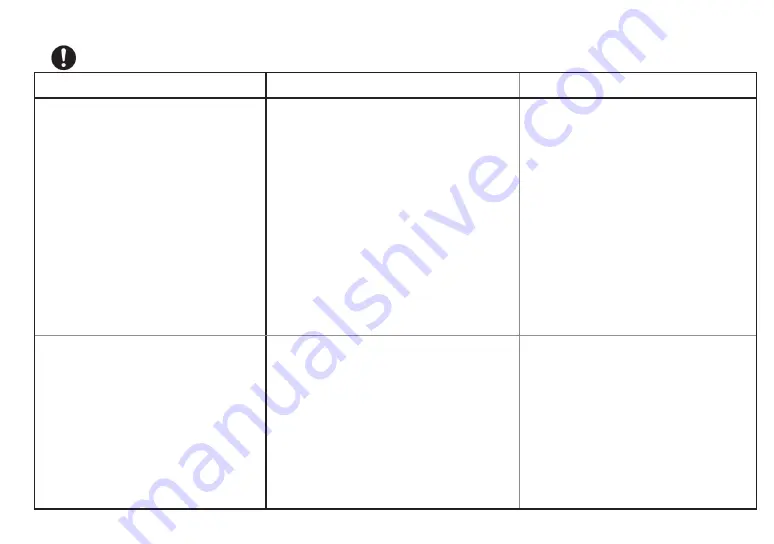
-
28
-
Trouble
Cause
Corrective measures
The machine does not operate though
the power switch is turned ON.
・
Power is not supplied.
・
A screw hasn't been removed from the
pick up spot for a certain amount
of time.
・
Too many screws were loaded into the
scooping hopper.
・
A foreign object (for example: a screw)
intruded into the main body.
・
The AC adapter is faulty.
・
Check the connection of the power
supply of the AC power adapter.
・
Take the screw out from the
pick up site.
・
Adjust the timer setting knob.
・
Reduce the quantity of screws in the
scooping hopper to a proper load
level.
・
Remove the foreign object.
・
Consult our service section.
[Model number UI315-15]
Screws do not flow.
・
Screws with a larger diameter than the
specified rail size were loaded or screws
with a different diameter were mixed
in together.
・
An insufficient quantity of screws are in
the scooping hopper.
・
Use screws with the specified
nominal diameter.
・
Remove the screws with the odd
nominal diameter.
・
Add a proper quantity of screws into
the scooping hopper.
10.
TROUBLESHOOTING
For safety, always unplug the AC adapter from the wall outlet before making any adjustments.
Summary of Contents for OM-26R Series
Page 43: ...42...