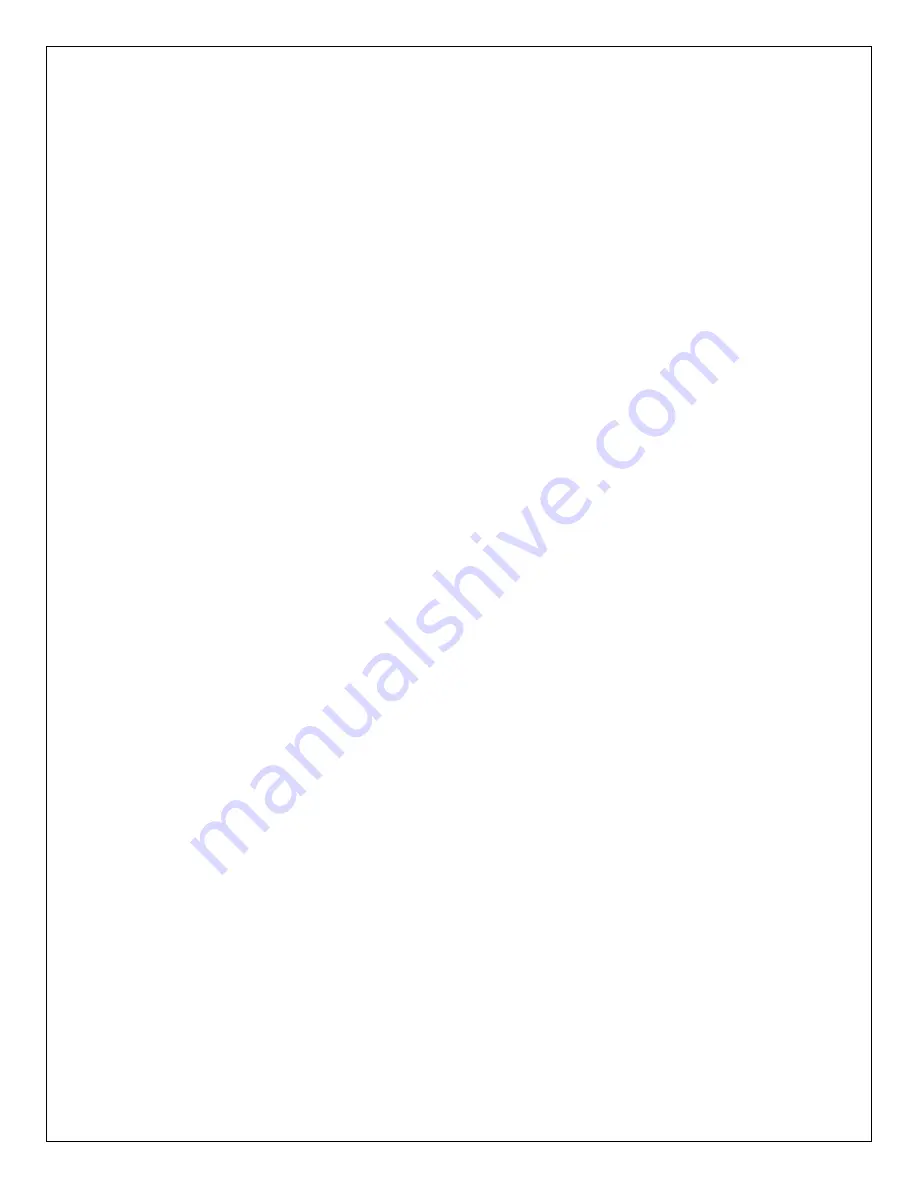
Effective 07/2014
IV
Oxygen Cleaning Procedure
Scope
This procedure sets forth the cleaning requirements for parts that are used in the
construction of
OGSI
oxygen systems and are in the gaseous oxygen product stream,
including but not limited to valves, tubing, fittings, manifolds and pipes. This procedure
represents the method for cleaning OGSI oxygen service equipment. These cleaning
methods and subsequent inspections result in a degree of cleanliness required for the safe
operation of the oxygen service equipment.
This document is based on guidelines provided in the Compressed Gas Association (CGA)
publication
CGA G-4.1-2009,
and is intended to comply with that publication.
Supersession
This procedure supersedes all previous written and verbal direction set forth with Audubon
Machinery Corp and its operating subsidiaries on the topic of cleaning and preparing parts
for oxygen service.
The Chief Engineer, or his/her delegate, shall periodically review this document as well as
other industry relevant procedures and publications to ensure consistency between AMC
internal procedure and industry norms.
Safety
Contamination such as grease, dirt, oil, dust, solvents, weld slag, sand, rust, paper, fiber,
rags, wood, coal, and previously applied thread sealants on parts that come into contact
with oxygen can cause a combustion reaction resulting in system degradation, failure, or a
hazard to nearby personnel. Care needs to be taken in the cleaning and handling of
components used in oxygen service to prevent any contamination related failure.
While the
CGA G-4.1-2009
standard makes allowance for cleaning parts using caustic
agents, acids or solvents, the
OGSI
procedure will use only mechanical (soaking, wire
brushing or grinding) means for pre-cleaning and hot water cleaning with aqueous
detergents for final cleaning. An effective rinse with potable water is mandatory and
applied to ensure that the residual cleaning agent is removed from the system.
Training
Personnel involved in the cleaning, preparation, and assembly of parts used in oxygen
service will be trained in these cleaning procedures and be familiar with this document.
Documented evidence of training (with annual refresher training) shall be maintained by
the supervisor of each impacted employee.
Summary of Contents for OG-15
Page 2: ...Page left intentionally blank...
Page 45: ...Effective 07 2014 Appendix...
Page 46: ...Page left intentionally blank...
Page 48: ...Page left intentionally blank...