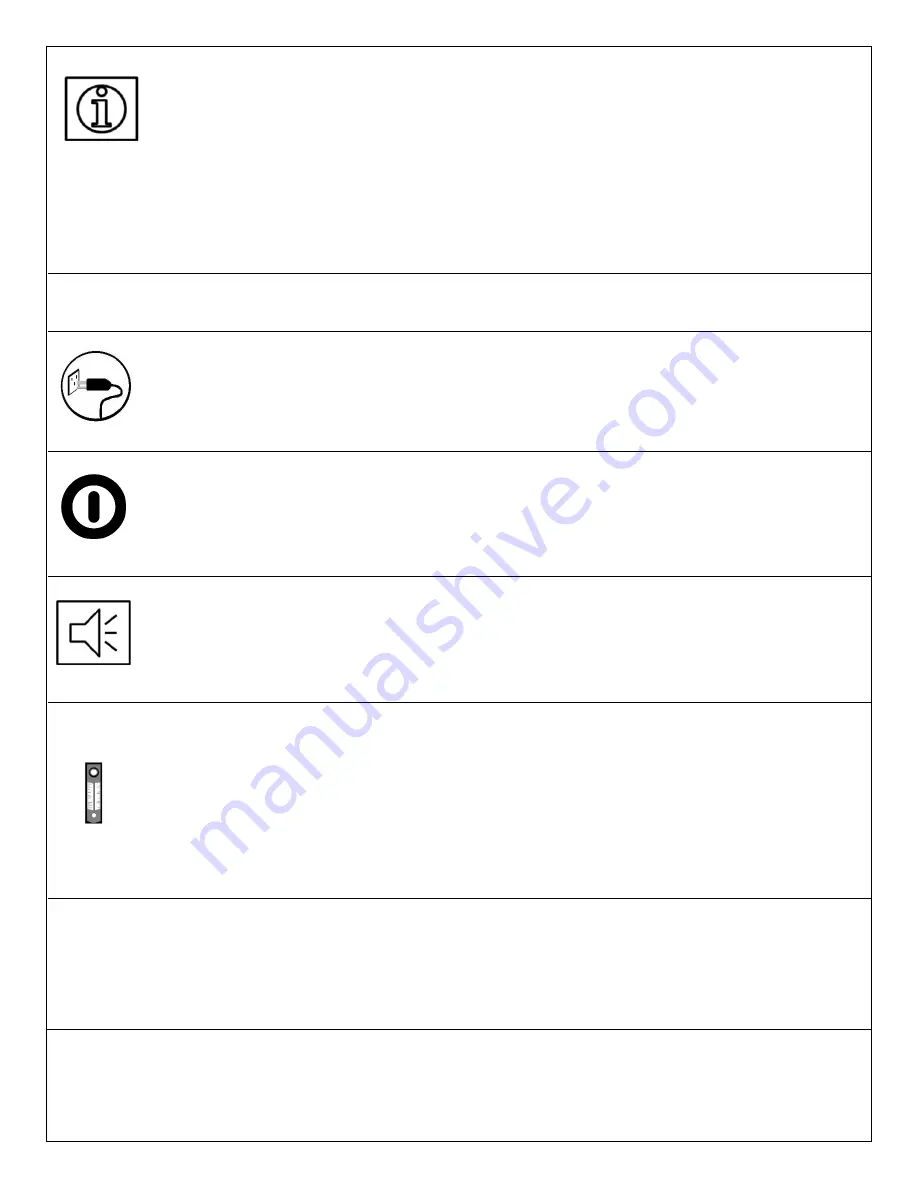
Effective 07/2014
36
Set-up & Installation
Although every
OG-15/OG-20
unit is thoroughly tested and checked before it is
shipped from our facility, the following steps are necessary to ensure that none of the
internal components have been damaged during shipment. This check should take less
than five minutes to perform.
(Refer to ‘
Initial Inspection’
on page 2 and ‘
Unpacking
Instructions
’ on page 5 before reading the instructions below)
Make a visual inspection of the machine and make sure all parts are properly connected.
(Refer to ‘
Components
’ section)
Connect the unit into a grounded electrical outlet. A receptacle plug of local configuration
will need to be attached first if the machine has been shipped outside North America.
Push the
ON/OFF
green lighted power switch to the
ON
position and make sure that the
green light is illuminated.
Listen for the sound of the compressor to start operating. If you do not hear it within a few
seconds, shut the machine down immediately and call
OGSI
for assistance.
Once the machine is operating, turn the knob on the upper part of the oxygen flow meter to
adjust the oxygen flow to
7 LPM
(
0.4 Nm
3
/h)
for
OG-15
and
10 LPM (0.5 Nm
3
/h
) for
OG-20
.
The ball in the flow meter should be in the middle of the flow meter indicating
7 LPM
or
10 LPM
flow for
OG-15
and
OG-20
respectively. The oxygen pressure gauge should read
12
psi (0.83 bar)
or
20 psi (1.4 bar)
for
OG-15
and
OG-20
respectively. If it does not, turn the
oxygen regulator either clockwise to increase the pressure or counter-clockwise to decrease it
until it reaches
12 psi (0.83 bar)
or
20 psi (1.4 bar)
for
OG-15
and
OG-20
respectively.
You should be able to feel oxygen being discharged from the lower left oxygen outlet port.
If these things do not occur, check to make sure that none of the hose connections have
come loose. Call the
OGSI Technical Service Department
at
(800) 414-6474
(toll free
number in USA and Canada) or
(716) 564-5165
if no loose connections are found and
trouble persists.
Summary of Contents for OG-15
Page 2: ...Page left intentionally blank...
Page 45: ...Effective 07 2014 Appendix...
Page 46: ...Page left intentionally blank...
Page 48: ...Page left intentionally blank...