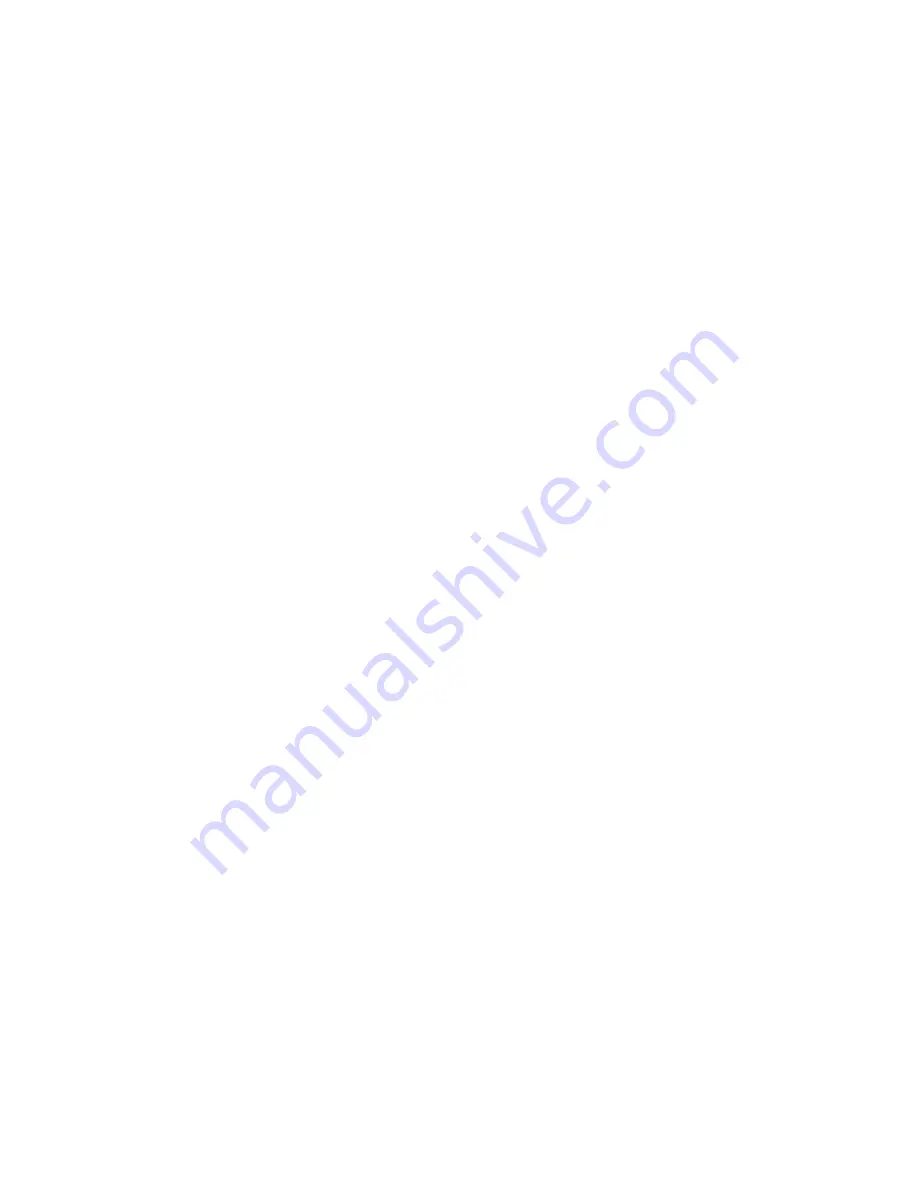
38
5.
Place output planet sub-assembly into windows of spindle (1A). The output planets must
have their part number facing up. Slide the planet sub to the center of the spindle. Repeat
the same for the rest of output planet sub-assemblies.
6.
Lift and rotate the housing sub-assembly over the spindle (1A) so that the seal is facing
down. Align the housing outer seal bore with the spindle inner seal diameter surface. Lower
the housing onto spindle. Insure that the housing is seated onto the spindle.
7.
Slide each output planet sub out from the center of the spindle and install planet shaft (1N).
Rotate the planet shaft so that the threaded hole is pointed towards the center of the
spindle.
8.
Insure the planet shaft (1N) is fully seated against the bearing shoulder of the planet sub.
Rotate the housing in order to seat the output planet bearings.
NOTE:
Skip step 9 if reusing old planet shims and pins on the planet shaft. Be sure to put
correct sets in to correct Holes, see step 5 and 6 page 24.
9.
Measure gap between the spindle (1A) and planet shaft (1N) using depth micrometer. Lightly
tap the planet pins to insure that they are fully seated, then re-measure the gap. Shim
thickness is gap measured plus .001 inches to .002 inches, so that there is .001-.002 inches
of preload.
10.
Stack shims (1K) and place the shims on the recessed face of the planet pin. Stack the
shims such that the thickest shim is on top.
11.
Place Bearing Carrier (1M) on the bench with the counter bored holes facing down.
12.
Press the Main Bearing Cone (1C) onto the Bearing Carrier using a tool similar to T-191993
13.
Place the Bearing Carrier (1M) with the Bearing Cone (1C) onto the top of the Spindle (1A)
to help keep the Hub Sub-Assembly aligned to the Spindle. Make sure to align thru hole with
the taped holes in the spindle without disturbing the shims.
14.
Press the Hub Sub-Assembly onto the Spindle (1A) by pressing down on the Bearing Carrier
(1M). An arbor press or hydraulic press (as long as the pressure is very low) maybe used to
press down on the bearing carrier.
NOTE:
Take extreme caution to ensure that the Hub Sub-Assembly is being pressed
squarely onto the Spindle.
15.
Apply loctite 263 to 6 bolts (1P) and install them in the bearing carrier as per BCD procedure
and torque them. Rotate the housing by hand. Apply loctite 263 to the remaining bolts (1P).
Install and torque complete.
This concludes the Housing-Spindle Subassembly.
Summary of Contents for Torque-Hub C014C5 Series
Page 1: ...1 Torque Hub Planetary Final Drive C014C5 Series Service Manual Rev 01 11 13 ...
Page 14: ...14 THIS PAGE INTENTIONALLY LEFT BLANK ...
Page 15: ...15 DISASSEMBLY ...
Page 18: ...18 THIS PAGE INTENTIONALLY LEFT BLANK ...
Page 28: ...28 ASSEMBLY ...
Page 41: ...41 Planetary Final Drive Service Manual Assembly Drawing ...
Page 45: ...45 T179926 ASSEMBLY PRESSING TOOL ...
Page 46: ...46 T214917 ASSEMBLY PRESSING TOOL ...
Page 47: ...47 T215321 SEAL PRESSING TOOL ...
Page 48: ...48 T205708 LEAK TEST ADAPTER ...
Page 49: ...49 T219813 BEARING CONE HEATER ...
Page 50: ...50 T219850 STUD DRIVER ...