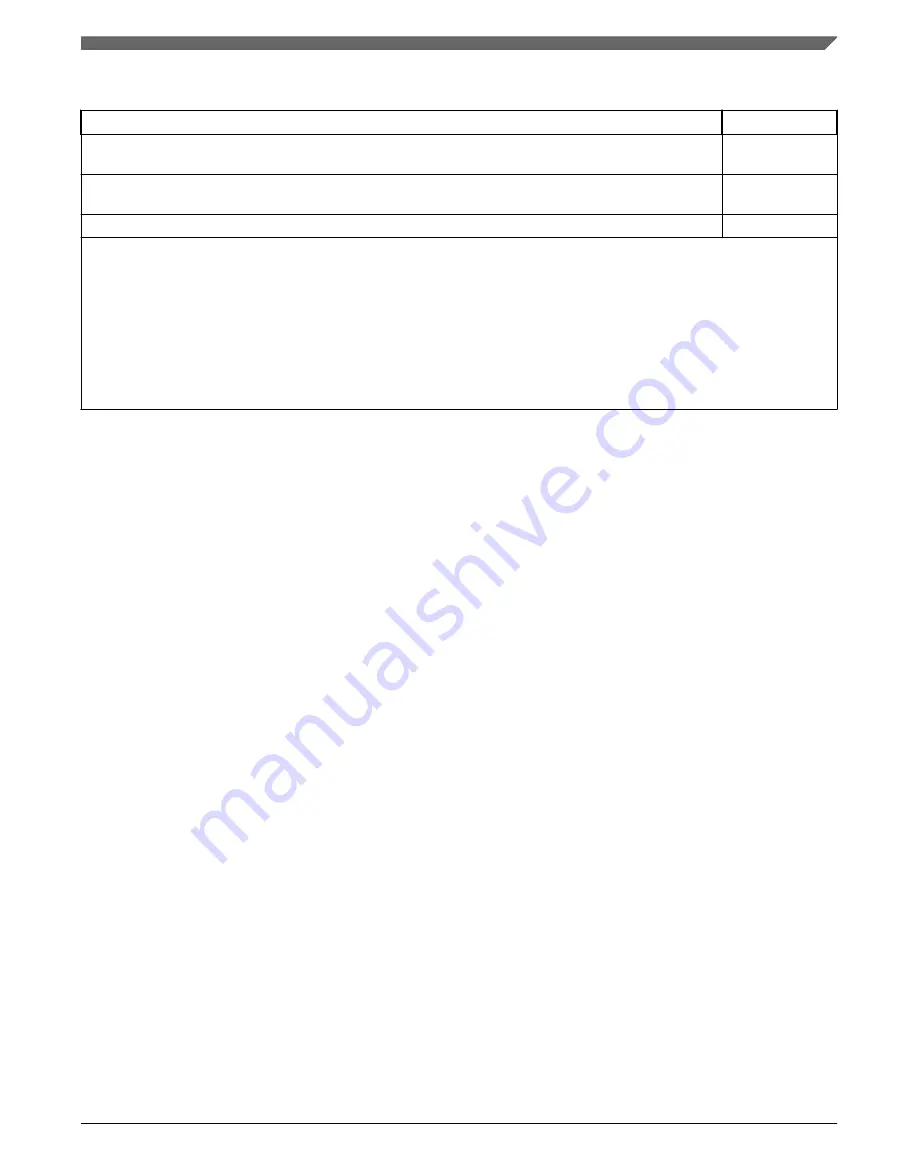
Table 43. Thermal system-level checklist (continued)
Item
Completed
A thermal interface material is required at the package-to-heat sink interface to minimize the thermal
contact resistance.
3
Ensure the method of mounting heat sinks on the package is by means of a spring clip attachment to the
printed-circuit board.
A thermal simulation is required to determine the performance in the application.
4
Notes:
1. The system board designer can choose among several types of commercially available heat sinks to determine the
appropriate one to place on the device. Ultimately, the final selection of an appropriate heat sink depends on factors such as
thermal performance at a given air velocity, spatial volume, mass, attachment method, assembly, and cost.
2. The performance of the thermal interface materials improves with increased contact pressure; the thermal interface vendor
generally provides a performance characteristic to guide improved performance.
3. The system board designer can choose among several types of commercially available thermal interface materials.
4. A Flotherm model of the part is available.
6.3 Internal package conduction resistance
For the package, the intrinsic internal conduction thermal resistance paths are as follows:
• The die junction-to-case thermal resistance
• The die junction-to-lid-top thermal resistance
• The die junction-to-board thermal resistance
This figure shows the primary heat transfer path for a package with an attached heat sink mounted to a printed-circuit board.
Thermal
QorIQ LS1046A Design Checklist , Rev. 2, 06/2020
NXP Semiconductors
55