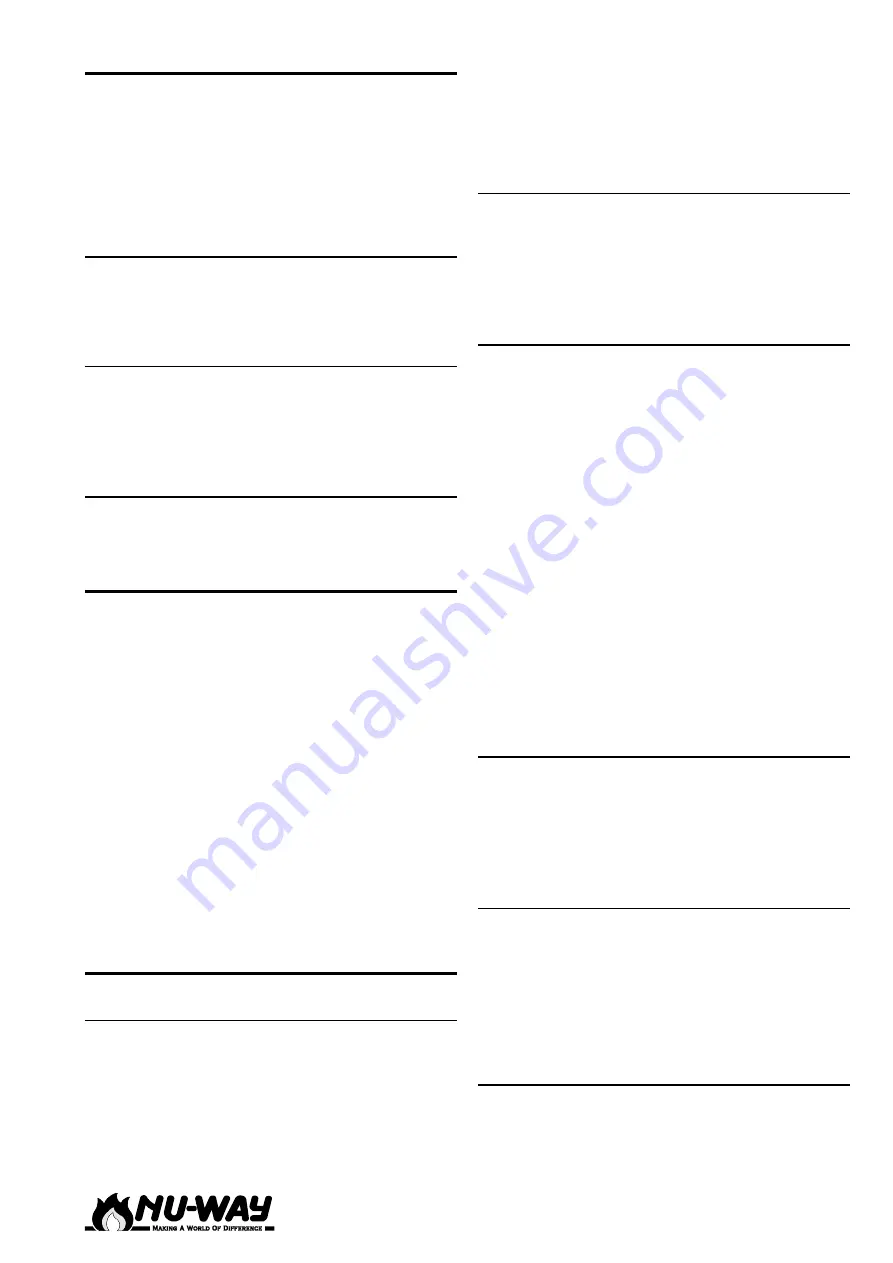
Page 15
NDFL100-38 / BR003211 / Rev. 220900A
Developed from Worldwide field experience, the
NDFL100-38 sets new standards in efficient and
reliable operation. The burner is designed to meet
the requirements of all international markets.
Delivered ready to install with prewired packaged
control system and plug in gas train.
Air Regulation
Air for combustion can be adjusted to give
maximum efficiency. A closed position air control
is incorporated as standard.
Controls & Operation
Flame supervision is by U.V. cell (Gas) and
photocell (Oil). Microprocessor controllers are
employed for automatic start-up, running, and
shutdown of the burner.
Fuel
Natural gas and light distillate oil Class D (1.5-5.5
cSt @ 40°C).
G
ENERAL
This manual is structured to enable the user to
proceed from the delivery of the burner to its
commissioning and use.
The conditions to be fulfilled and the controls and
adjustments to be used are dealt with in the
sequence that should be followed for the correct
installation and use. Pre-commissioning and Live
Run are described, and the location of necessary
controls and adjustments to undertake these are
illustrated and supported by appropriate tabular
matter and graphs.
Routine Maintenance, Fault Finding, and Spare
Parts identification complete the manual.
literature on proprietary components is available
on request.
S
ERVICES
& S
ITE
C
ONDITIONS
Gas Supply
The gas supply pipework must be constructed and
installed in compliance with the appropriate Codes
and Standards, and comply with all local
conditions. It shall be of sufficient size to satisfy
the pressure and volume flow requirements of the
burner under all firing conditions.
F
EATURES
A 90° manual isolation valve must be fitted
upstream of the gas control train to allow the
burner to be isolated for maintenance.
To avoid any restriction in gas flow the size of this
valve should not be less than that of the gas train.
Fuel Oil Storage and Handling
The requirements of BS2869 will ensure that the
fuel is suitable. Under sustained cold and exposed
conditions, class D grade of fuel should be stored
and supplied to the burner at a minimum
temperature of 5°C (14°F).
Fuel Oil Supply
The oil line should consist of copper tube (NEVER
galvanised steel). The final connection to the pump
inlet port is made with a flexible pipes supplied
with the burner. Joints should be made with
compression fittings.
When gravity feed is used, the maximum head
should not exceed 4m, (35 kPa). The return side of
the burner pump
MUST
be piped into the oil
supply line at a distance of no less than 1 Metre
from the pump inlet connection This will prevent
the oil attaining temperature from the oil pump
whilst the burner is firing on gas.
On installations where the fuel tank is situated
below the level of the burner the maximum
suction permitted is 40 kPa (300 mm HG) and a
two-pipe (supply and return) fuel supply system
MUST
be used.
Gravity feed system
On a single pipe (gravity feed) system, the pump
should be primed under gravity from the tank and
not by running the pump mechanically. To prime
the pump remove the purge plug, connect the
purge port to a suitable container.
Suction lift System
The suction line will require priming before
energising the pump mechanically. It is essential
to ensure that the return pipe is not obstructed in
any way. Any obstructions will damage the pump.
The fuel supply line may need priming if the oil
storage is allowed to drain completely.
Flue and Chimney Requirements
The flue and chimney must be constructed and
installed to the appropriate local conditions, Codes
and Standards. It shall be of sufficient size to satisfy
the volume of flue gases at all firing conditions.