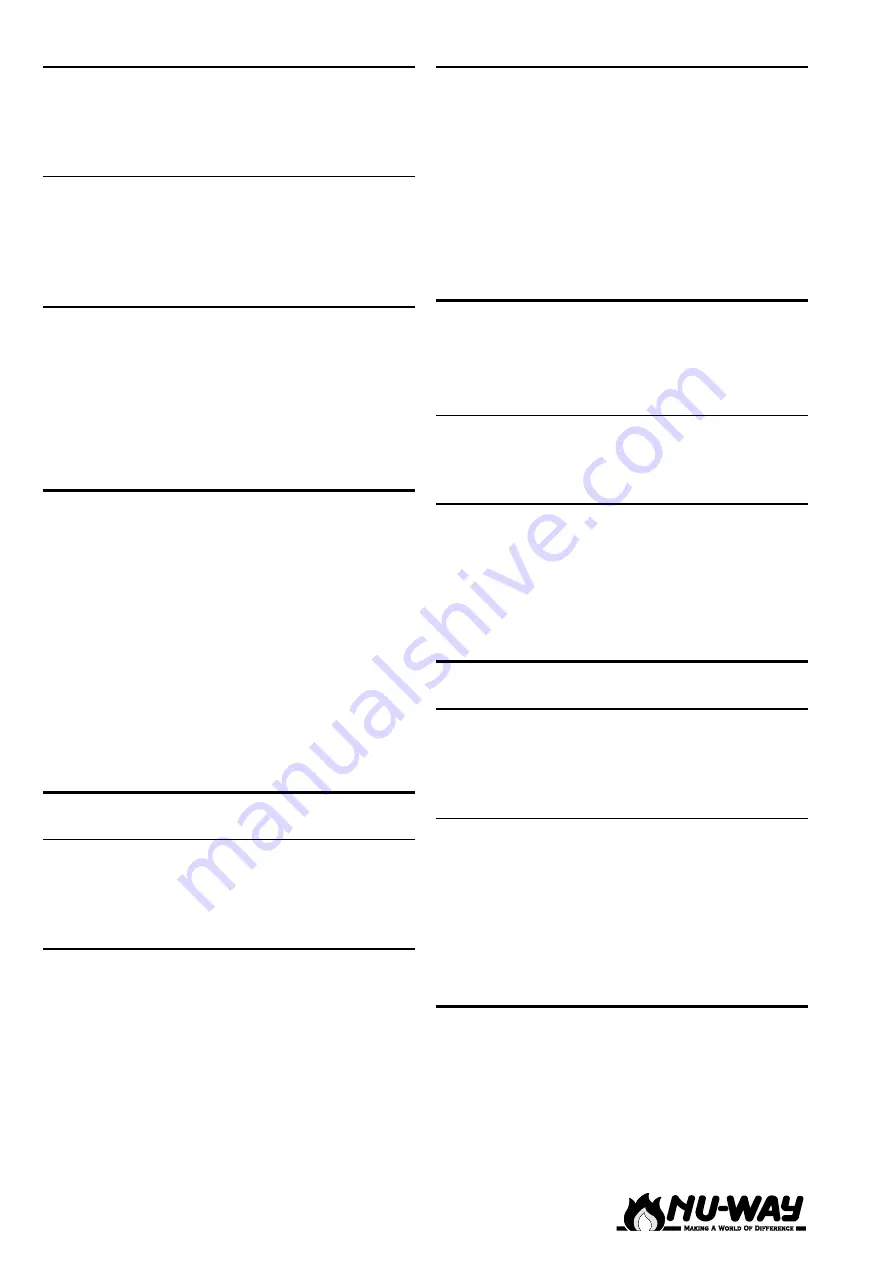
NDFL100-38 / BR003211 / Rev. 220900A
Page 16
Plant Room Ventilation
An adequate dust free supply of fresh air is required
for the burner at both high and low level in
accordance with the appropriate standards.
Existing Appliances
In preparing the appliance to receive the burner, a
careful inspection should be made of its condition
after it has been cleaned thoroughly to remove all
adhering tars, scale and dirt.
Combustion Chamber Conditions
When the burner is fitted to an appliance designed
to work under balanced or negative combustion
chamber conditions, the over-fire draught must not
exceed 0.25 mbar.
Should the over-fire draught exceed this figure,
then steps should be taken to reduce it to this level.
A
SSEMBLY
Fit the gas train to the gas inlet mounting flange
using the gasket nuts and washers provided.
Ensure that the gasket is seated correctly when
tightening the assembly.
Connect the four number-coded plugs from the
gas valves V1 and V2, the gas pressure switch and
the gas butterfly valve to the
GAS
MPA22 controller
sockets 2,3,7 & 14 respectively.
Do not force the plugs into the sockets. If difficulty
is encountered, check the coding to ensure correct
location.
I
NSTALLATION
General
Check that the burner is appropriate for the
appliance rating. Detailed burner performance
data is given on page XX.
Fitting to the Appliance
If the burner is to be fitted to a new packaged unit,
refer to the manufacturers recommendations.
If the burner is to being fitted to an existing
appliance, prepare the mounting flange as detailed
on page 5.
Ensure the joint between appliance and burner is
effectively sealed with the gasket provided.
Unless otherwise specified, the flame tube should
be flush with the inner face of the appliance
combustion chamber.
Electrical Power Supply
Connect a three phase 50Hz electrical supply to
the burner observing all applicable IEE Regulations.
Connect all of the applicable external auxillary
controls.
Refer to the electrical supply specifications and
connection diagrams shown on pages 8 to 14.
If supplied as a packaged appliance/burner unit
refer to the manufacturers instructions.
B
URNER
A
IR
C
ONTROLS
A motorised air flap controls the air for
combustion. It is located inside the air inlet, see
page 5.
Air Diffuser
The air diffuser creates a pressure drop to ensure
good fuel/air mixing and flame stability.
Air Pressure Switch
The air pressure switch is required to prove ad-
equate air flow throughout the burner operating
cycle. Air flow failure at any stage after pre-purge
will result in a lockout, failure during pre-purge
will result in four restarts before a lockout.
B
URNER
G
AS
C
ONTROLS
Gas Nozzle
The hole in the gas nozzles is designed to suit the
output of the particular burner model and gas type
being used.
Gas Pressure Switch
The low gas pressure switch is located between
the two gas valves and has two functions: -
To monitor the gas pressure during the burner
operating cycle. A low gas pressure will result
in the safe shutdown of the burner.
The check the gas leak integrity of the valves.
I
NTEGRATED
V
ALVE
P
ROVING
S
YSTEM
The burner comes complete with an integrated
Valve Proving System.
A leakage test is performed after every controlled
shutdown.
A leakage test is performed before the burner is
started after a power failure or fault reset.