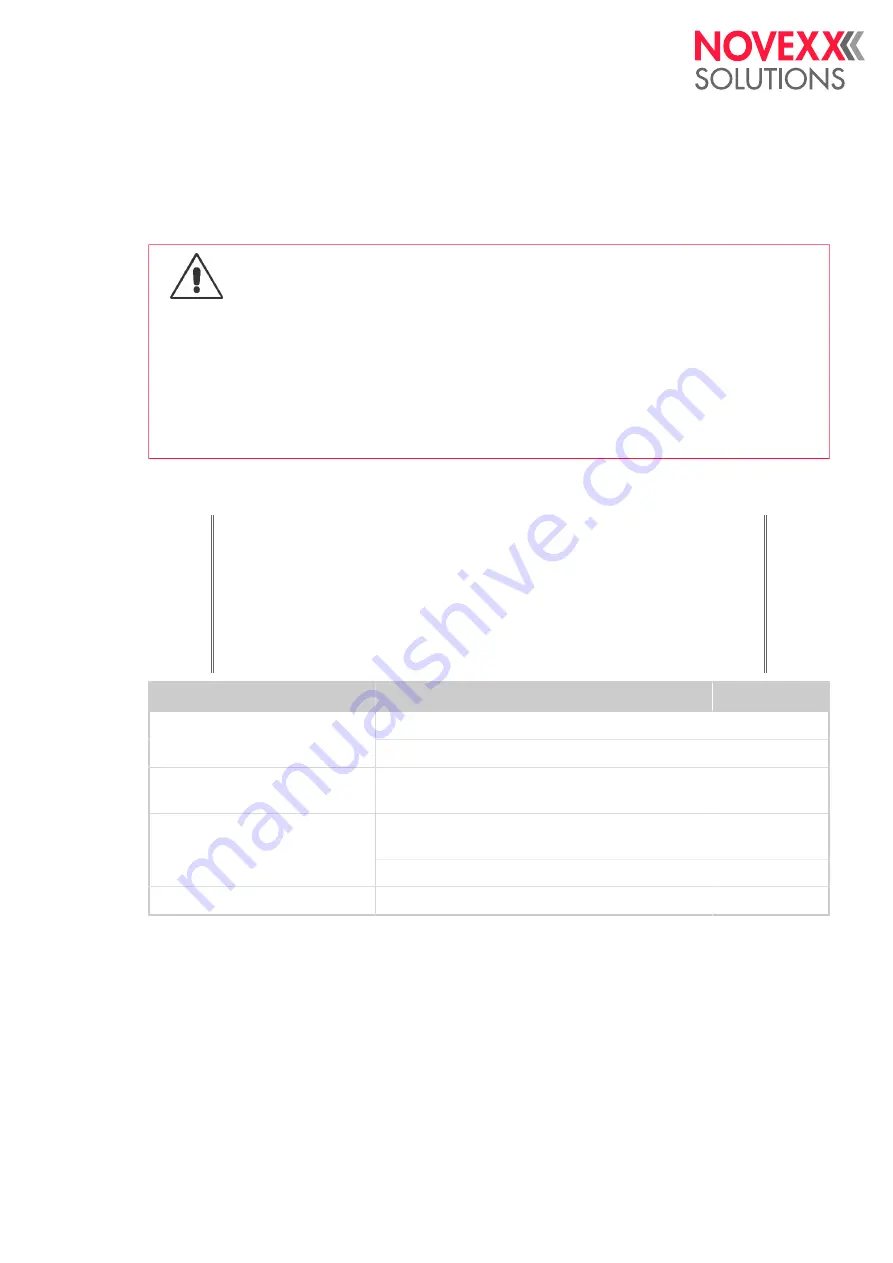
User Manual
XLP 514/516
Cleaning
CLEANING INSTRUCTIONS
WARNING!
Dangerous situations may arise during maintenance and cleaning work. Accidents
may occur due to mechanical or electrical effects if the relevant safety instructions are
not observed!
► Switch off the machine before cleaning or maintenance and pull out the mains pow-
er connecting line!
► Never allow liquid to get into the machine!
► Do not spray the machine with spray bottles or sprays! Use a cloth wetted with
cleaning agent!
► Repairs to the machine must only be made by trained service technicians!
Cleaning agents
CAUTION!
Sharp cleaning materials may damage the printer.
► Do not use any cleaning agents or materials that could damage or destroy
the paint finish, labelling, display, type plates, electrical component, etc.!
► Do not use any scouring cleaning agents or any cleaning agents that could
dissolve plastic!
► Do not use acid or alkaline solutions!
Part to be cleaned
Cleaning agent
Article number
Cleaning pen
95327
Print head
Spirit or isopropyl a cloth
--
Rubber rollers (print roller, draw
roller, ...)
Roller cleaner
98925
Cleaning gasoline, methylated spirit, isopropyl
alcohol
--
Deflection rollers
Label release spray
A103198
Housing
Standard commercial neutral cleaning agent
--
Table 20: Recommended cleaning agents
Cleaning interval
► Clean machine regularly.
The frequency depends on the following factors:
• Operating conditions
• Daily operating duration
• Label material/ribbon combination used
Edition 1 - 8/2021
99
Cleaning
Cleaning Instructions