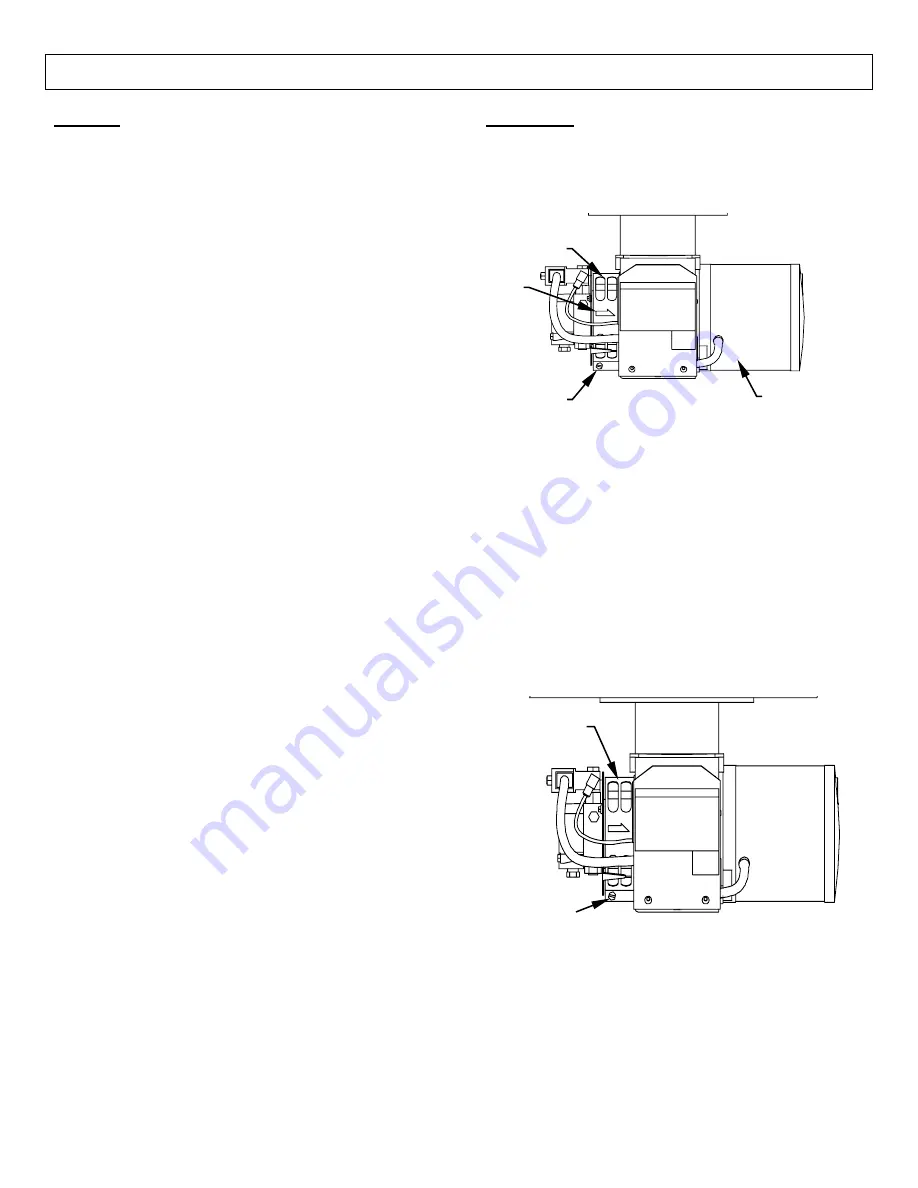
Installation Instructions
6
Venting
DANGER: Do not run machine indoors or in an
enclosed area without adequate ventilation, or in
areas where flammable vapors, (gasoline, solvents,
etc.) may be present. Do not vent exhaust gases into
a wall, a ceiling, or a concealed place.
CAUTION: All venting must be in accordance with
applicable state and federal laws, and local
ordinances. Consult local heating contractors.
If the pressure washer is to be used in an enclosed area,
a flue must be installed to vent burner exhaust to the
outside atmosphere. Be sure the flue is the same size
as the burner exhaust vent on the pressure washer lid.
Poor draft will cause the pressure washer to soot and
not operate properly. When selecting the location for
installation, beware of poorly ventilated locations or
areas where exhaust fans may cause an insufficient
supply of oxygen. Proper combustion can only be
obtained when there is a sufficient supply of oxygen
available for the amount of fuel being burned. If it is
necessary to install a unit in a poorly ventilated area,
outside fresh air may have to be piped to the burner and
a fan installed to bring sufficient air into the unit. Locate
the pressure washer in such a manner that the flue will
be as straight as possible and protrude through the roof
at a proper height and location to provide adequate draft.
This oil fired unit must have a draft controller installed in
the flue. A draft controller will permit proper upward
airflow of exhaust flue gases.
Oil Burner
Burner Air Adjustment: The oil burner is preset and
performance tested at the factory (elevation 1100 feet).
Different altitudes may require a one-time initial burner
correction.
1.) Turn the engine and heat switches ON (Refer to
“
Operation
” for details). Have someone operate the
spray gun so the burner fires.
2.) Loosen the locking screw and close the air band until
black smoke appears from the burner exhaust vent.
Note the position of the white arrow on the air band.
3.) Slowly open the air band until white smoke just starts
to appear.
4.) Turn the air band half way back to the black smoke
position previously noted. Tighten the locking
screw.
5.) Fine tune the burner air by loosening the shutter lock
screw and turning the shutter until the exhaust is
cleanest. Tighten the shutter lock screw.
CAUTION: If white smoke appears from the burner
exhaust vent during start-up or operation,
discontinue use and readjust air bands.
NOTE: If a flue is installed, have a professional
serviceman adjust your burner for a #1 or #2 smoke
spot on the Bacharach scale
.
Locking
Screw
Air Band
Burner
White
Arrow
Shutter
Lock Screw
Shutter
Summary of Contents for M157598L.1
Page 17: ...Parts Breakdown 157598 Rev L 1 17...
Page 19: ...Parts Breakdown 157597 Rev L 1 19...
Page 21: ...Wiring Diagram Rev L 1 21...
Page 22: ...Pump Breakdown 22...
Page 23: ...Pump Breakdown 23...
Page 27: ...27 This page has intentionally been left blank...