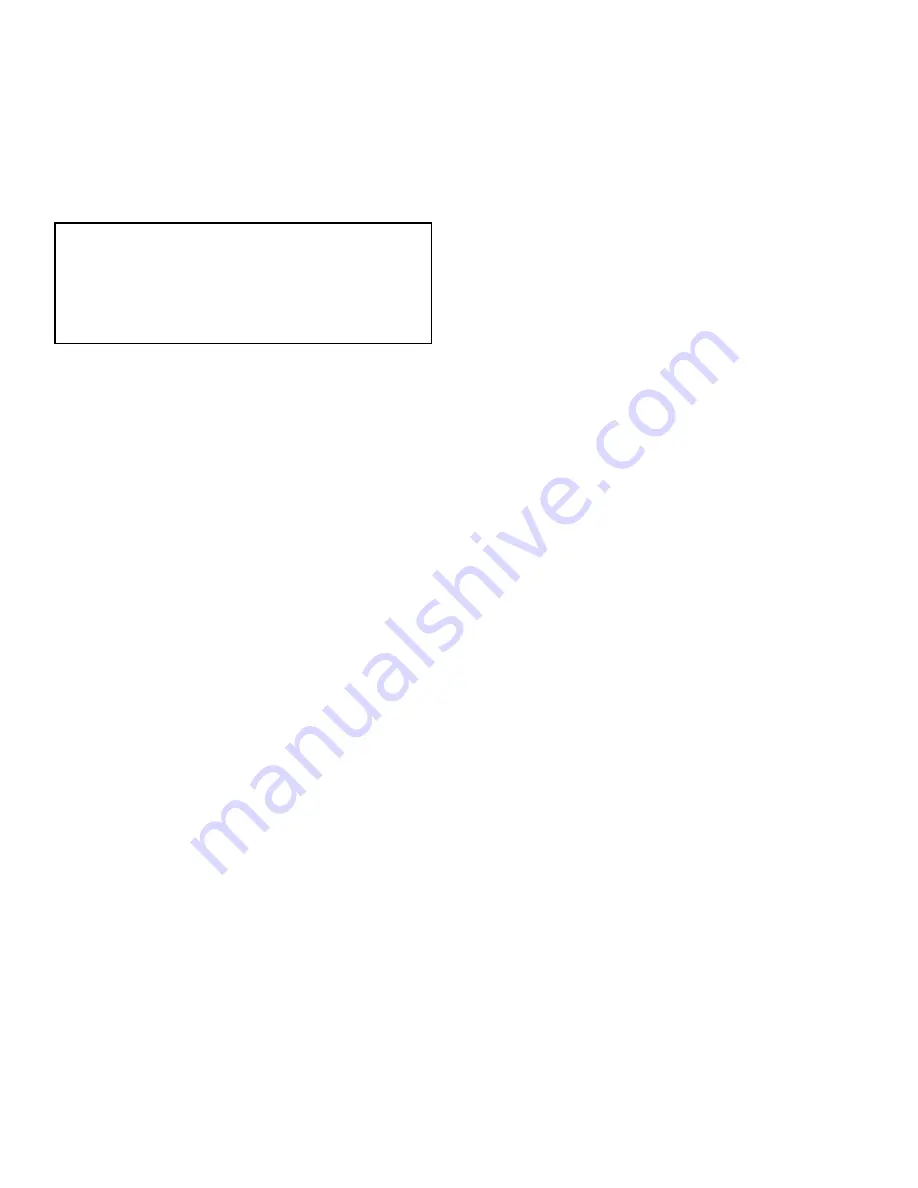
for obvious signs of deterioration, accumulation of
dirt and debris and any heat or water related dam-
age. Any damaged or deteriorated parts should be
replaced before the unit is put back into service.
2. Clean burners, heat exchanger, draft inducer and
vent ducts. Periodically clean the screens in the vent
terminal (where applicable).
3. Check heat exchanger for cracks. If any are present,
replace heat exchanger before putting unit back into
service.
4. Check the attachment point of the furnace module to
the cabinet or ducts to verify that they are air-tight.
5. Check the automatic gas valve to ensure that the
gas valve seat is not leaking.
Furnace Module Operation Check
1. Turn on power to the unit and set thermostat or heat
controller to call for heat, allowing furnace module to
operate.
2. Check for proper start-up and ignition as outlined in
the Start-up section.
3. Check the appearance of the burner flame (see Fig-
4. Return thermostat or heat controller to normal setting.
5. Refer to the Appliance Manufacturer’s instructions
for annual maintenance procedures on the complete
unit.
Replacement Parts
Replacement parts for the gas-fired furnace module are
available through our Parts and Service Department at:
Nortek Air Solutions
1502 D Quebec Avenue
Saskatoon, SK S7K 1V7
Email:
Phone: 1-866-483-6627
Fax: 1-800-667-3716
SN Sequence of Operation – On/Off
Operation
Fenwal 35-61 Series Direct Ignition Control with
Two-stage Gas Valve
When system is powered up 24 VAC will be applied to the
ignition control (IC) terminals 24 VAC/R. The control will
reset, perform a self-check routine, initiate full time flame
sensing, flash the diagnostic LED for up to four seconds
and enter the thermostat scan standby state.
Call for Heat
1. Thermostat (controller) closes on call for heat power-
ing terminal T2.
2. 24 VAC to is supplied to IC terminal TH, provided
limit switch is in closed position.
3. The control will check that pressure switch contacts
are open (IC terminal PSW is not powered).
4. Combustion blower is then energized at high speed
through IC terminal IND.
5. When the air switch (APS-1) closes, a 15 second
pre-purge period begins.
6. At end of pre-purge period, the spark commences
and the gas valves (both first and second stage) are
energized for the trial for ignition period.
7. Burners ignite and cross light, operating at maximum
input rate (manifold pressure set at 3.3” to 3.5“ w.c.).
8. When flame is detected by flame sensor the spark is
shut off immediately and gas valve(s) and combus-
tion blower remain energized.
9. During heating operation, the thermostat, pressure
switch and main burner flame are constantly moni-
tored to assure proper system operation.
10. When the thermostat (controller) is satisfied and
the demand for heat ends, the main valves are de-
energized immediately, the control senses loss of
flame and a 30 second post-purge occurs before
de-energizing the combustion blower.
11. If flame is lost during an operational cycle, the control
will respond within 0.8 seconds. The spark will be
energized for a trial for ignition period to attempt to
re-light burners and prove flame sensor. If flame is
re-established, normal operation resumes.
Ignition and Operational Failures During a Call for
Heat Result in Lockout of the Ignition Control
1. If the burners fail to light or carryover during a trial for
ignition, the control will attempt two additional igni-
tion trials. If no flame is present at the flame sensor
within 10 seconds, the spark and gas valve will be
de-energized. A 15 second inter-purge period begins
and the combustion blower continues to run. After
the inter-purge period another ignition trial will take
place.
2. If burner fails to light or prove the flame sensor fol-
lowing the two additional trials the control will go into
lockout. The valve relay in the IC will be de-energized
shutting off the gas valve immediately and the com-
bustion blower following a 30 second post-purge
period.
Recovery from Lockout
1. If the thermostat is still calling for heat one hour after
a lockout occurs, the control will automatically reset
and initiate a call for heat sequence.
CAUTION
If any of the original wiring needs to be replaced, it must
be replaced with wiring materials suitable for 105°C.
Label all wires prior to disconnection when servicing unit.
Wiring errors can cause improper or dangerous opera-
tion. Verify proper operation after servicing.
VCES-VHC-IOM-1F – VHC-36, -42 & -50
73