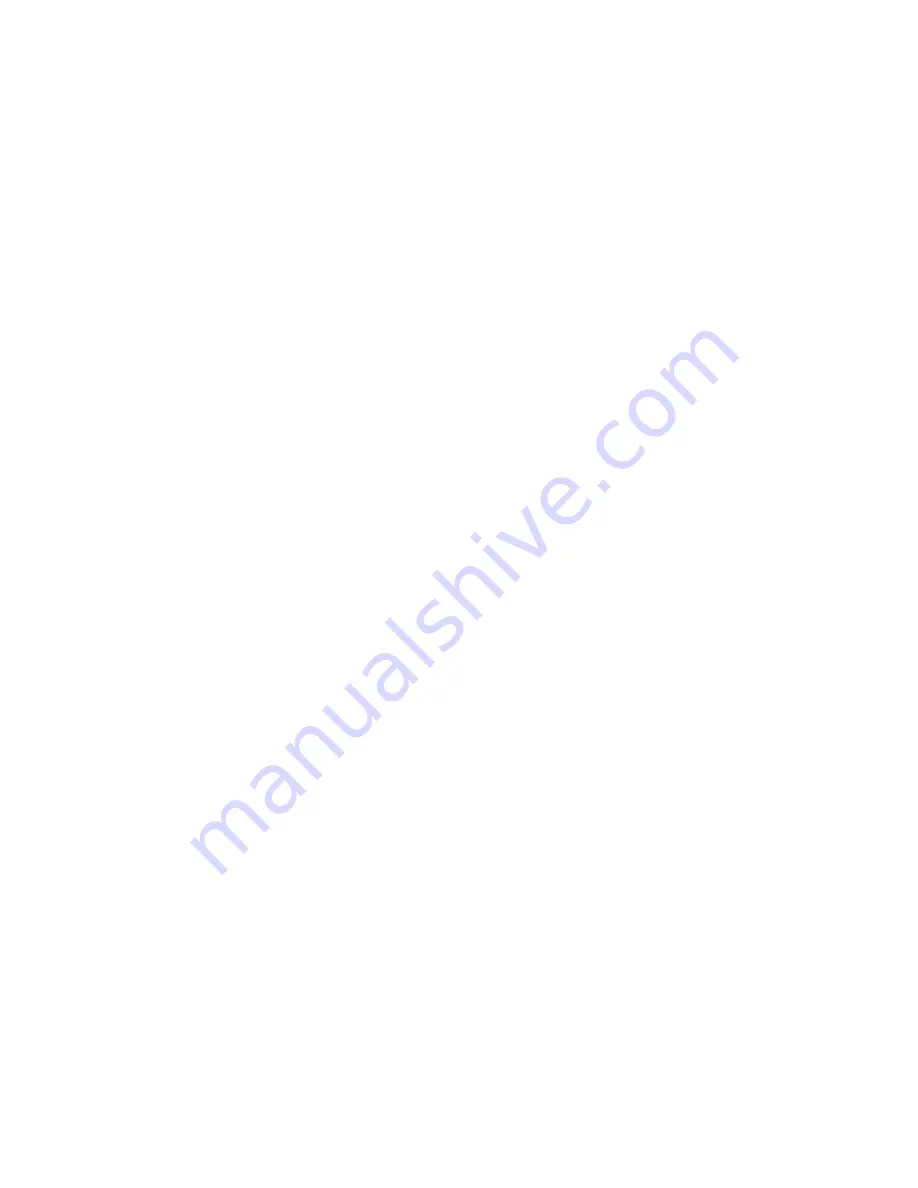
HP Series Installation Manual
|
8
Pre-Installation
Prior to beginning installation of the HP HVAC system, the required tools should be obtained,
and all contractor-supplied parts (indicated as parts “By Others” throughout this manual) should
be gathered.
Required Tools
In order to assemble an HP HVAC system the following tools and supplies are required:
1
Hammer
2
Socket Set, common imperial and sizes
3
Box-end wrenches – various sizes
4
Pipe Bender
5
Screwdriver Set, including standard flathead and Phillips
6
Caulking
7
Caulking Gun
8
Metal Snips
9
Hacksaw
10
Plumbing Tape
Required Components
The following components must also be supplied to complete the installation:
Electrical Disconnect Switches
Disconnect switches must be supplied to isolate the humidifier for maintenance and in the case
of emergency. If the control panel and disconnect is to be located outdoors, NEMA rated
disconnect switches should be used per national and local codes.
Sizing High Pressure Stainless Steel Tubing
Stainless steel piping must be supplied for distances between the HP pump module and the HP
manifolds. These distances should be kept to a minimum to minimize pressure losses and
maximize system performance, however it is important to avoid over-sizing the lines. For most
installations a 1/2” line is appropriate. Stainless Steel Pipe Fittings
Stainless steel compression fittings are required for all high-pressure line connections. When
using swage type fittings to connect feed lines together, use fittings of the same material as the
feel lines. Never use a brass compression fitting on a stainless steel tube, as the brass will not
properly hold the harder stainless steel pipe.
Follow manufacturers instructions when installing fittings.
Recommended tube material: 304L stainless steel tube, ½” Outside Diameter, 0.049” Wall
thickness
Recommended fittings: 316 stainless steel, ½”, double ferrule compression connections.
Summary of Contents for HP Series
Page 7: ...HP Series Installation Manual 4 Figure 1 Typical Installation with Medium Pump ...
Page 8: ...5 HP Series Installation Manual Figure 2 Typical Installation with Large Pump ...
Page 10: ...7 HP Series Installation Manual Installation ...
Page 15: ...HP Series Installation Manual 12 Figure 3 Medium Pump Module Installation Drawing ...
Page 16: ...13 HP Series Installation Manual Figure 4 Large Pump Module Installation Drawing ...
Page 24: ...21 HP Series Installation Manual Figure 15 Typical Valve Block Assembly ...
Page 29: ...HP Series Installation Manual 26 Figure 17 Valve Coils Figure 18 Valve Wiring ...
Page 36: ...33 HP Series Installation Manual ...
Page 37: ...HP Series Installation Manual 34 Startup Operation Maintenance ...
Page 49: ...Troubleshooting 46 Troubleshooting ...
Page 52: ...49 Troubleshooting ...
Page 53: ...Spare Parts 50 Spare Parts ...
Page 61: ...Spare Parts 58 Figure 37 3 and 6 Stage Valve Assembly Spare Parts ...
Page 62: ...59 Spare Parts ...
Page 63: ...Wiring Diagrams 60 Wiring Installation Diagrams ...
Page 64: ...61 Wiring Diagrams Figure 38 Pump Control ...
Page 66: ...63 Wiring Diagrams Figure 40 Pump Controller with Danfoss Integrated VFD ...
Page 67: ...Wiring Diagrams 64 Figure 41 1 Stage Valve Controller ...
Page 68: ...65 Wiring Diagrams Figure 42 3 Stage Valve Controller ...
Page 69: ...Wiring Diagrams 66 Figure 43 6 Stage Valve Controller ...
Page 73: ...Wiring Diagrams 70 Figure 47 HP Valve Controller April 9 2010 ...
Page 74: ...71 Wiring Diagrams ...