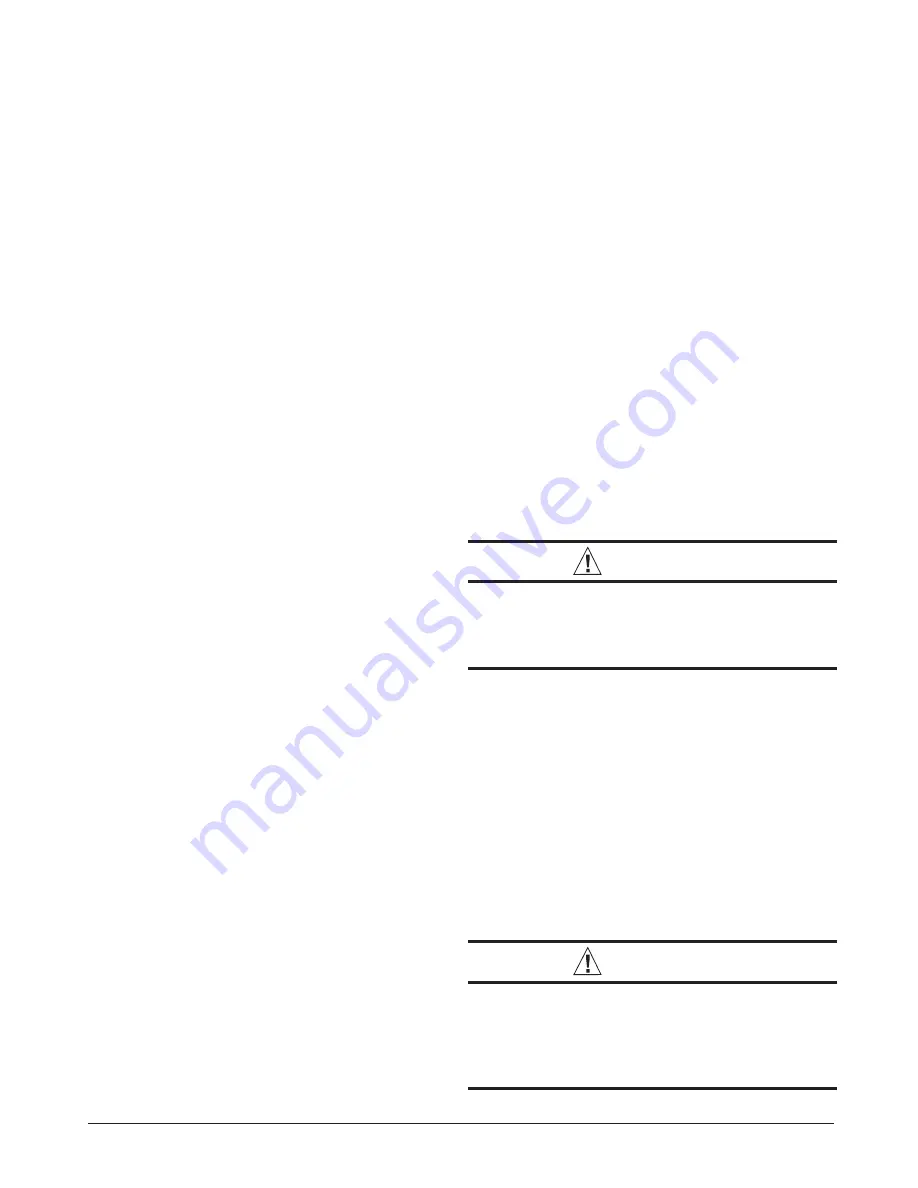
20
for 120 seconds at the selected HEAT speed. The
Indoor blower motor is de-energized after a blower
off delay as selected by the movable jumper.
Cooling Cycle
1. The thermostat calls for cooling by energizing the
Y
terminal with 24VAC.
2. The control energizes the blower in the cooling speed
and sends 24VAC to the contactor in the condensing
unit.
3. When the thermostat removes the call for cooling,
the contactor in the outdoor condensing unit is de-
energized and the control continues to run the fan for
a period of 60 seconds.
Fan Mode
• When the thermostat energizes the
G
terminal for
continuous fan (without calling for heat or cooling), the
indoor fan is energized on the selected FAN speed.
• If a call for cooling occurs during continuous fan, the
blower will switch over to the selected COOL speed.
• If the
W
terminal receives a call for heat during continuous
fan, the blower will de energize.
• A call for fan is ignored while in lockout.
MAINTENANCE
WARNING:
These maintenance instructions are primarily
intended to assist qualified technicians
experienced in the proper maintenance and
operation of this appliance.
Proper maintenance is most important to achieve the best
performance from a furnace. Follow these instructions for
years of safe, trouble free operation.
• Always replace the doors on the furnace after servicing
or cleaning/changing the fi lters.
Do not operate the
furnace without all doors and covers in place.
• Verify the thermostat is properly installed and is not being
affected by drafts or heat from lamps or other appliances.
• To achieve the best performance and minimize
equipment failure it is recommended that a yearly
maintenance checkup be performed. At a minimum,
this check should include the following items:
Air Filter(s)
WARNING:
Never operate the furnace without a fi lter in
place. Dust and lint in the return air can build
up on internal components, resulting in loss
of effi ciency, equipment damage, and possible
fi re.
Verify Operation of the Supply Air Limit Switch
Note:
A properly functioning limit switch should turn off
the gas valve when the return is blocked (time depends
on how well the return air is blocked). The circulating air
and combustion blowers should continue to run when the
limit switch opens.
1. Verify the blower door is securely mounted in place
and that there is power to the furnace.
2. Block the return airfl ow to the furnace by installing
a close-off plate in place of or upstream of the
fi lter(s).
3. Set the thermostat above room temperature and
observe the Operating Sequence.
4. Remove the close-off immediately after the limit
switch opens. If the furnace continues to operate
with no return air, set the thermostat below room
temperature, shut off the power to the furnace, and
replace the limit switch.
OPERATING SEQUENCE
The operating sequences for the heating, cooling, and
fan modes are described below. Refer to the fi eld and
furnace wiring diagrams: (Figures 12-13, page 17) and
(Figure 17, page 30).
Heating Cycle
1. The thermostat calls for heat by energizing the
W
terminal with 24VAC.
2. The control verifi es the pressure switch is open.
3. If the pressure switch is open, the control energizes
the inducer and waits for the pressure switch to close.
The pressure switch must close within 10 seconds.
4. The control runs the inducer for a 30 second pre-
purge.
5. The control energizes the igniter output for the
appropriate warm-up time limit.
6. The control energizes the main gas valve for 3
seconds.
7. If the fl ame proved and ignites the gas, the control
de-energizes the igniter. The gas valve and inducer
remains energized. The control goes to blower on
delay.
8. If fl ame is present, the control energizes the blower
on the selected HEAT speed 30 seconds after the
gas valve opened. The gas valve and inducer remain
energized.
9. When the thermostat demand for heat is satisfi ed, the
control de-energizes the gas valve. The inducer output
remains on for a 30 second post-purge period.
10. Blower off timing begins when the thermostat is
satisfi ed. The control will operate at the selected HEAT
speed of 60, 90, 120, or 180 seconds. If the blower off
delay jumper is not present, the fan should still operate
Summary of Contents for 045C-23ASA
Page 34: ...34...