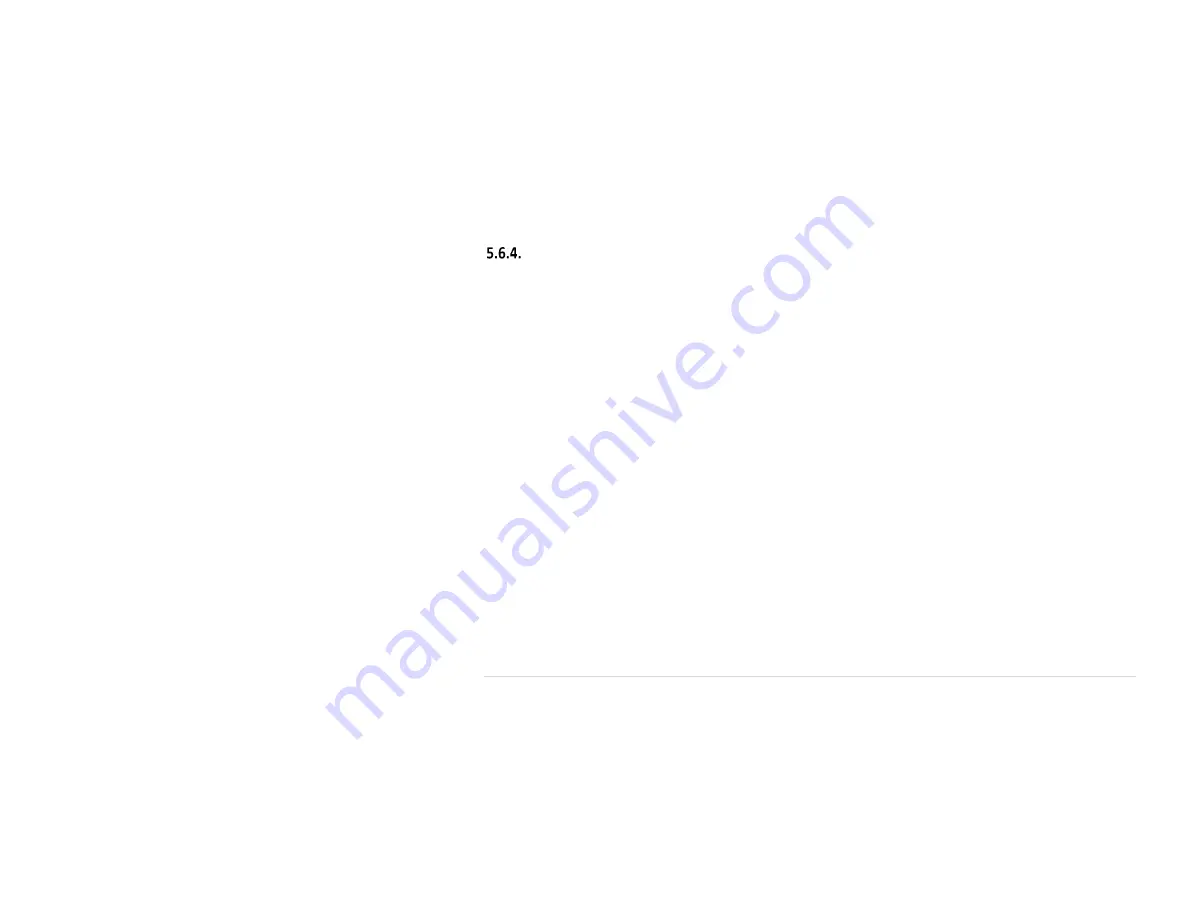
49
Calibrating
Boom
Geometry
1.
Ensure
the
sprayer
is
over
bare
level
soil
or
gravel.
2.
Ensure
the
boom
is
level
and
approximately
3
–
5
feet
(100
‐
150
cm)
above
the
ground.
3.
Navigate
to
the
boom
geometry
test
(Run
Screen
‐
>
Settings
‐
>
Next
‐
>
Setup
‐
>
Boom
Geometry
Test).
4.
The
booms
will
be
moved
into
position
and,
the
display
will
prompt
you
to
exit
the
cab
and
manually
push
either
boom
tip
down.
Stay
at
least
3
feet
from
the
sensor.
5.
Push
either
boom
tip
down
1
–
3
feet
(30
–
90
cm)
for
a
moment
and
then
let
go.
Do
not
push
the
boom
to
the
ground.
Summary of Contents for UC5 Topcon X30
Page 1: ...NORAC UC5 Operator s Manual ...
Page 15: ...13 Select the setup button The setup screen will be displayed ...
Page 22: ...20 The automatic setup diagnostic screen is reached by selecting the diagnostics button ...
Page 36: ...34 5 3 Communication Tests ...
Page 41: ...39 Typical Self Propelled Sprayer Installation ...
Page 42: ...40 Typical Pull Type Sprayer Installation ...
Page 43: ...41 Typical Front Mount Sprayer Installation ...
Page 44: ...42 Typical Setup for Short Circuit Test ...
Page 56: ...54 7 UC5 Menu Structure ...
Page 57: ...55 ...
Page 58: ...56 ...
Page 60: ...58 7 2 Setup Valves ...
Page 61: ...59 7 3 Setup Switches Switches ...
Page 67: ...65 10 Notes ...
Page 68: ...66 ...