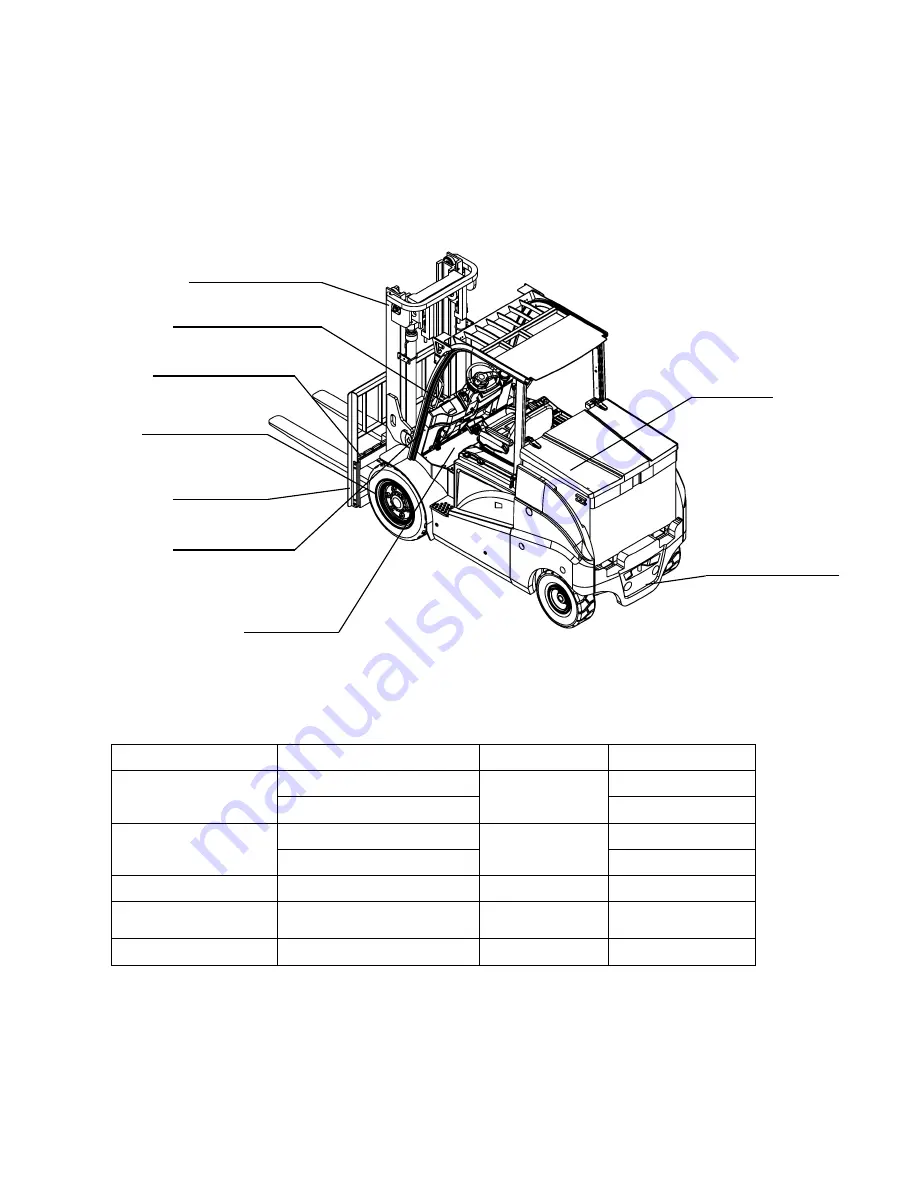
104
Ⅴ、
Area lubricated and lubricant recommended
1. Area lubricated
○
:
Change FO
:
Hydraulic oil
◎:
reinforce GO
:
Gear oil
□
:
Check and adjust
CG
:
Grease
BO
:
Brake fluid
W
:
Distilled water
2. Lubricant recommended
Name
Trademark
Capability(L)
Remark
Hydraulic oil
L-HM32
Max70
≥
-5
℃
L-HV32
≥
-20
℃
Gear oil
85W/90GL-5
12 (single drive)
3 (double drive)
-15
℃
~ +49
℃
80W/90GL-5
-25
℃
~ +49
℃
Brake fluid
Caltex DOT3
0.2
Industrial Vaseline
2#
Battery electrode
column
Grease
3# Lithium Grease
Lifting chain
□
◎
CG
Direction pipe column
◎
CG
Tilt cylinder pin
◎
CG
Mast bearing support
◎
CG
Drive axle
◎
□
CG
Brake pedal
□
Steering system
□
◎
CG
Battery
□
◎
W
Brake cylinder
◎
BO