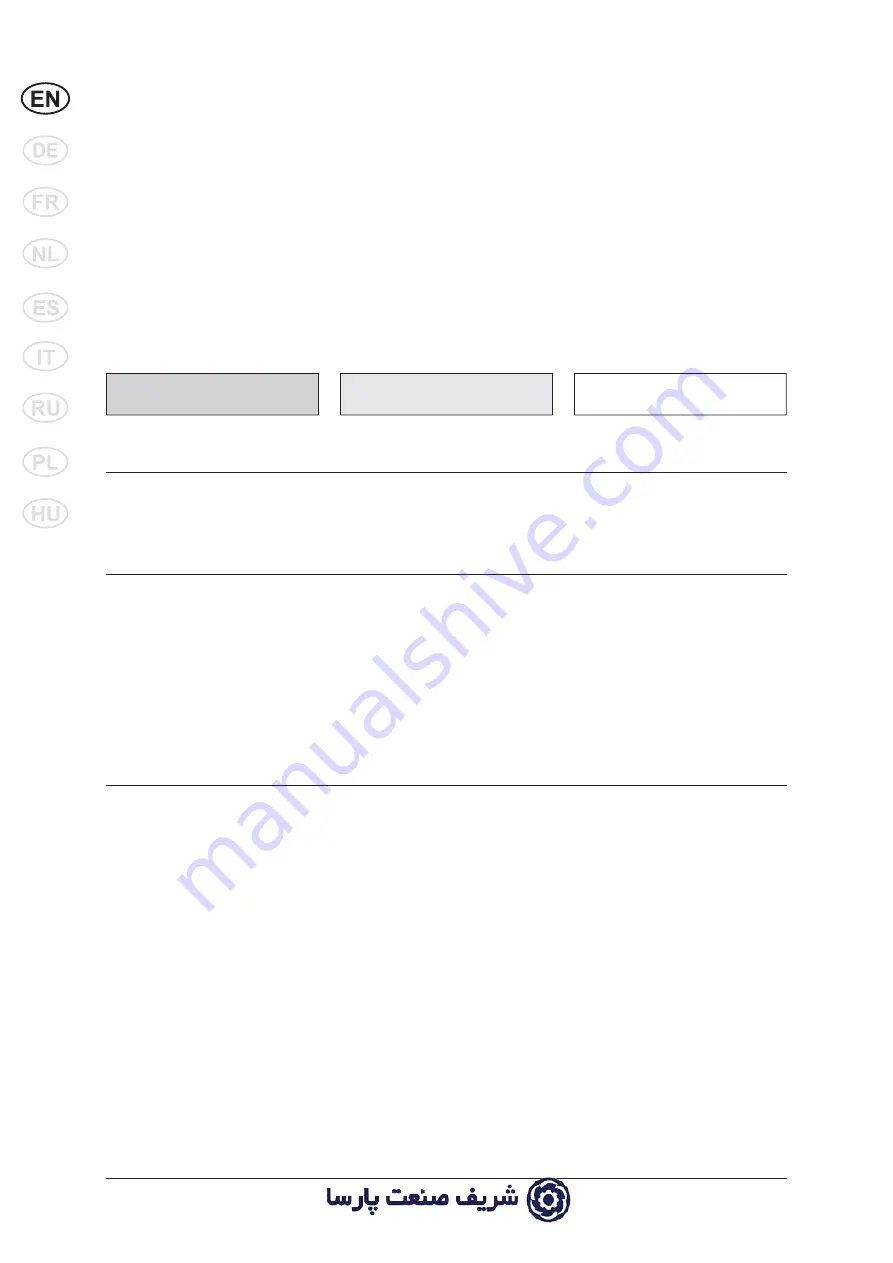
26
TRUCK BOOSTER
Original Instructions
7 Trouble
Shooting
You have chosen the best quality and therefore deserve the best service. The TRUCK BOOSTER
features an “Error detection system” that will stop the TRUCK BOOSTER in case of a severe error that
needs immediate attention. The red light of the STOP button will fl ash, and the display in the inspection
window will indicate the nature of the error.
Though the user can correct some of these errors, you should note the error and contact the nearest
Nilfi sk-ALTO service organization. To avoid unnecessary disappointments, you should check this sec-
tion before contacting the nearest Nilfi sk-ALTO service organization.
7.1 General trouble shooting
Symptom
Reason
Action
Machine will not start
> A fuse has blown
• Change the fuse.
(NO ERROR indication)
> Power disconnected
• Connect power.
Fuses blow
> Installation does not
• Change to an installation.
correspond to the ampere
corresponding to the ampere
consumption of the machine
consumption of the machine
at
a
minimum.
Change
the
fuse.
Working pressure too low
> Nozzle worn
• Replace the nozzle.
> Wrong spray lance
• Replace the spray lance
(see
section
4.1.4).
> Reduction valve of spray
• Turn reduction valve com-
lance not adjusted to max.
pletely counter-clockwise
pressure.
(see
section
4.1.4).
> Nozzle partly clogged up
• Clean the nozzle
(see
section
6.4).
Working pressure fl uctuating
> Insuffi cient water supply
• Check that the water tank is
not drained of water during
operation of the machine. If it
is, clean the water inlet fi lter
of the machine. If that does
not solve the problem, the
water supply for the machine
is
insuffi
cient.
NB!
Avoid long, thin hoses
(min.
3/4").
> High-pressure hoses too long
• Dismount high-pressure
extension hoses and retry.
Extension hose max. 50 m.
NB!
Avoid long extension
hoses with many couplings.
> Air in the system
• Vent the system
(see
section
3.7).
> Detergent container empty
• Refi ll or close dosing valve.