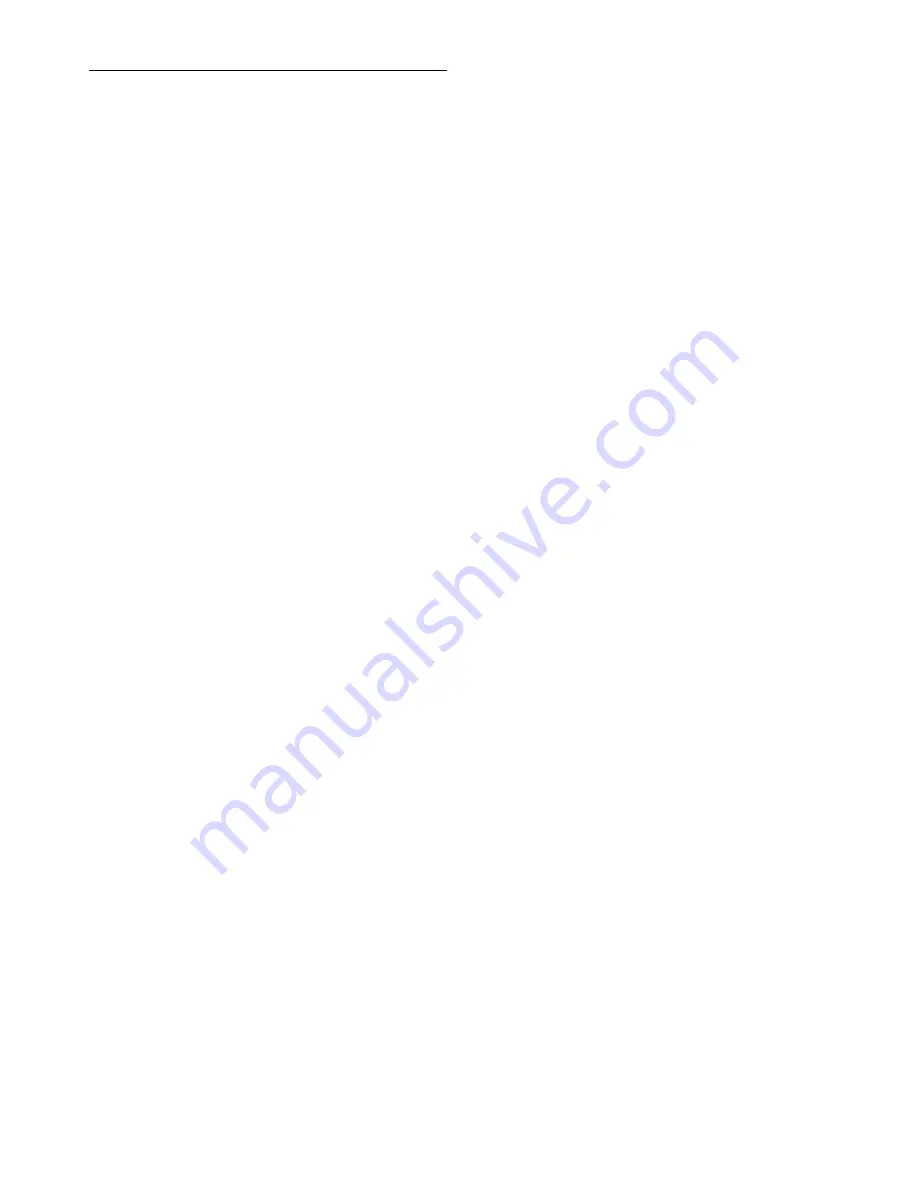
V. GENERAL MAINTENANCE PROCEDURES
A. Fuel System
The fuel system works from vacuum created by the engine running. Turning the fuel cylinder service valve ON
pressurizes the system for flow to the carburetor once the engine starts to crank.
1. Adjusting the Regulator
NOTE:
The regulator and carburetor have been "factory preset" and should not require any modification.
Only Kent authorized personnel, trained and certified in propane systems, should modify or adjust the
system or its setting.
N.F.P.A. 58 8-1.4 states, "In the interest of safety, each person engaged in installing, repairing, filling, or
otherwise servicing an LP-Gas engine fuel system shall be properly trained in the necessary
procedures."
2. Engine Dust Filter
The engine dust filter should be
cleaned each hour
and after each use by shaking out the dust and then
rinsing with mild detergent. Squeeze out the excess water (do not wring). Allow the filter to air dry.
Failure to maintain a clean engine filter will cause the engine to overheat. Also, it may cause the
exhaust emissions to elevate to harmful levels.
3. Carburetor Air Filter
a. Loosen wing nut on top of the air cleaner cover.
b. Remove foam pre-cleaner and paper filter element.
c. Clean foam pre-cleaner using the same procedure as "2" above.
d. Clean filter seal, making sure no dust is allowed in the carburetor inlet.
e. Inspect paper element. Replace if dirty, bent or damaged.
f. Install the clean paper element, pre-cleaner, air filter cover and wing nut.
NOTE:
Failure to service the carburetor air cleaner may produce excessive carbon monoxide
emissions and cause the SmartAir™ system to shut the engine down.
4. Hose and Fuel Connections
a. Inspection
(1) Inspect hoses for abrasions and other signs of wear; replace all worn or damaged hoses.
(2) Check for gas leaks by spreading soapy water solution around all the connections while the
service valve is turned ON and the fuel system is pressurized.
b. Fixing Leaking Joints
(1) Uncouple bad joint, clean joint then apply pipe sealing compound (Loc-Tite Pipe Sealant with
Teflon or equivalent) to the clean joint.
(2) Recouple the joint finger tight plus 1/2 turn.
(3)
Recheck for leaks using soapy water solution. Watch for bubbles at the joint with the
fuel cylinder service valve turned on and the fuel system pressurized.
B. Engine Maintenance
1. Cooling Fin Maintenance
a. Remove the blower housing and other cooling shrouds.
b. Clean the cooling fins as necessary using compressed air or pressure washer.
c. Reinstall all housings and shrouds.
2. Head Bolt Maintenance
a. Refer to Engine Manufacturer's "Service Manual".
5