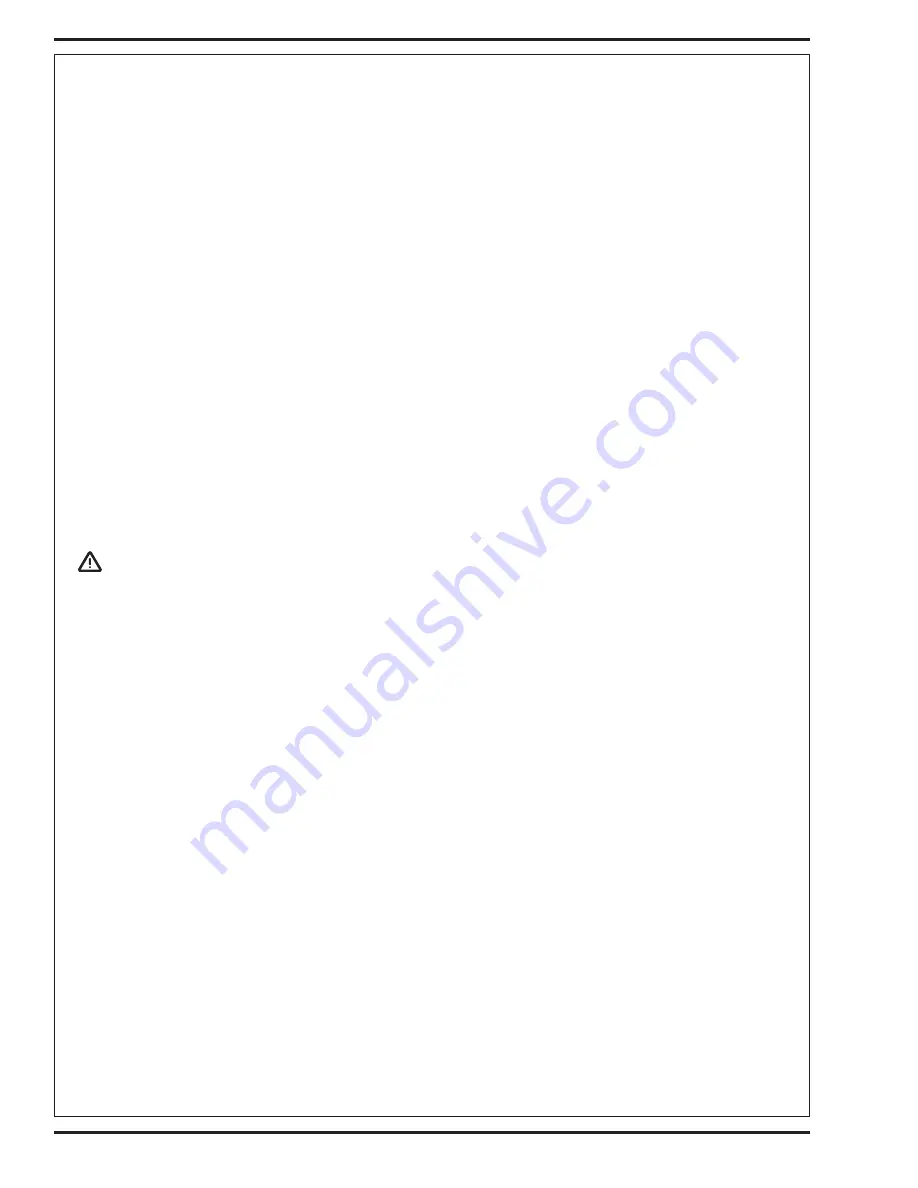
10 - FORM NO. 56043094 / Captor
™
4300, 4800, 5400 / CR 1100, 1200, 1400
STEERING SYSTEM
HYDRAULIC STEERING CYLINDER REMOVAL
1
Remove the recovery tank assembly from the machine.
2
Follow steps in the Solution Tank Removal section.
3
Remove the (2) screws that secure the electrical relay mount assembly and pull it out from the control box compartment.
4
See Figure 3. Remove the Hairpin (F) and then slide out the cylinder Mount Pin (G).
5
Remove the cylinder hoses, then plug and cap to prevent oil lose and system contamination.
6
Mark the steering rack and spur gear location with a center punch to help when reassembling.
7
Lift the rack and cylinder assembly straight up to complete its removal from the chassis.
8
With the rack and cylinder assembly removed inspect the nylon wear plates. Replace when mounting screws are exposed and striking the
rack.
WEAR ADJUSTMENT FOR CYLINDER RACK
1
See Figure 3. Loosen the (2) Hex HD Screws (H). Then using a large flat bladed screwdriver pry between the Adjustment Bracket (I) and
the steer spindle. This will remove any excessive play in the nylon wear plate and the rack, then tighten bracket-mounting screws to secure.
STEERING SPINDLE ASSEMBLY REMOVAL
1
Remove the squeegee tool assembly from the machine then remove the ignition key, set the parking brake and block the front wheels.
2
Remove the solution tank assembly (see Solution Tank Removal section for instructions).
3
See Figure 3. Remove the (2) (H) Hex Screws that fasten the rack adjustment Bracket (I) then rotate the bracket to clear the spur gear and
remove.
4
Remove from the spindle shaft the Cotter Pin (J) and Castle Nut (K). Next remove the (2) Set Screws (L) using a 4mm hex key wrench.
5
Pull the spur gear from its shaft then remove the square shaft Key (M) and Gear Spacer (N). Note: The gear spacer bevel faces down to
reassemble.
WARNING!
Never work under a machine without safety blocks and stands to support machine.
6
Jack up the rear of the machine approximately 24 inches (60cm) and put the jack stands in place under rear corner supports. Note: Guide
the spindle and wheel assembly out from under its frame housing being careful not to damage shaft threads and bearing surfaces.
7
Important Service Tip: Observe the hydraulic wheel motor hoses their routing and correct fitting locations then disconnect the (3) hoses, (2)
P-clamps (plug and cap hoses and fittings).
8
Service Tip: When installing or removing the spindle wheel assembly, use a piece of cardboard underneath the wheel to help in sliding the
assembly around (positioning).
BEARING REPLACEMENT AND SPINDLE INSTALLATION
1
You now have access to the upper and lower bearing cones, cups and seals (O, P & Q). Note: If replacing or inspecting bearings be sure
to (re) pack bearings with white lithium grease before installing.
2
To reassemble, first install the lower bearing cup, cone and seal into the Steering Casting (R). Note: It is important that the shaft goes through
the lower bearing as straight as possible, it may be easier to install the spindle with the tire removed placing the spindle weldment on top of
a movable service jack.
3
Slowly lower the rear of the machine guiding and repositioning the shaft through the center of the housing until the drive wheel supports the
machine.
4
Install the upper bearing cup, cone, seal, spacer and spur gear.
5
Install and tighten the castle nut, torque to 40 ft/lbs. (54Nm). Then loosen nut to align cotter pin.
6
Follow the spindle removal steps 1-4 in reverse order. Check that the drive wheel is positioned straight ahead, align the rack and gear (marked
teeth). Next follow the adjustment instructions for the cylinder rack and spur gear clearance (fit up) to eliminate any sloppy steering operation.