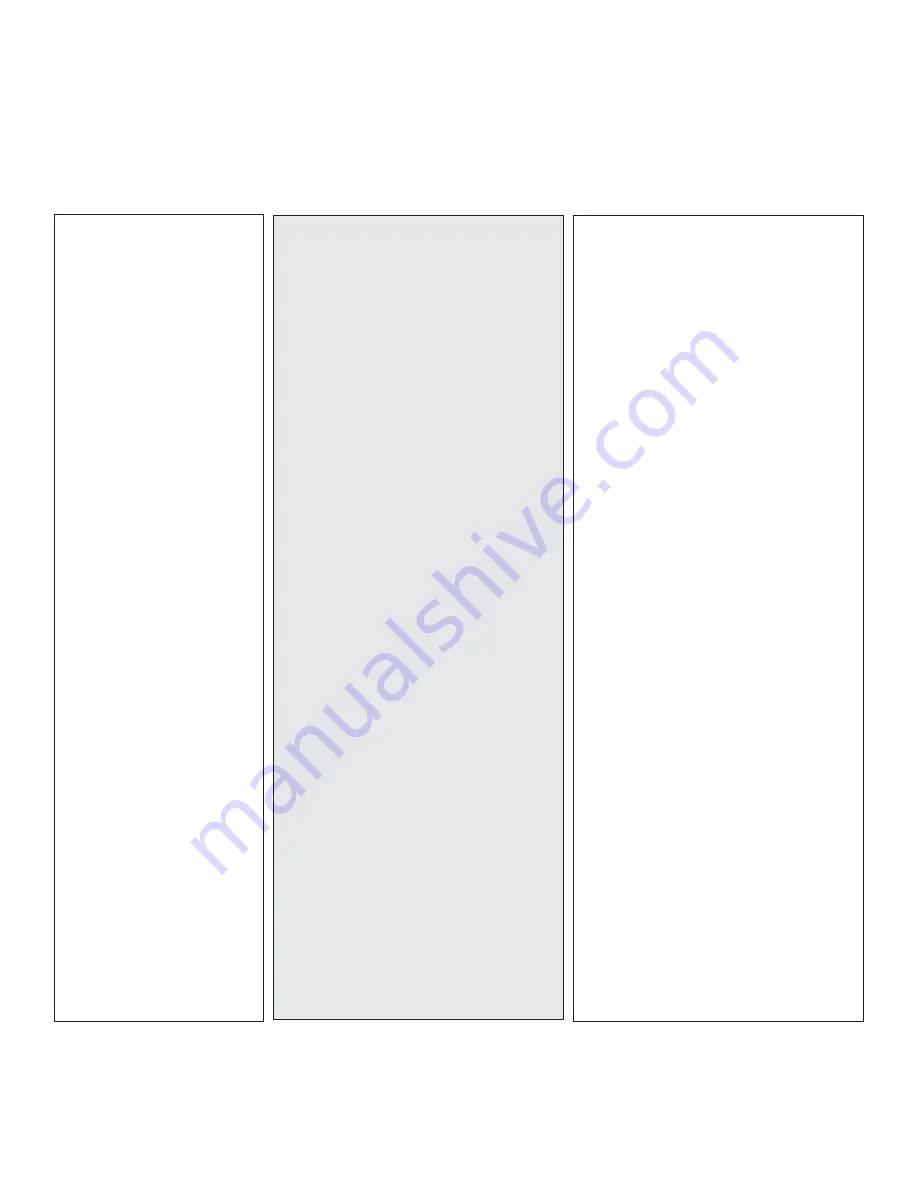
20
H. TROUBLE SHOOTING GUIDE
Identify the problem in the left column, and look for probable causes and solutions in the right hand columns. Probable
causes are listed in “most likely to happen” order. This sequence should be used to isolate the problem. Once the cause
is found, refer to OPERATION and PARTS AND LOCATION sections for explanation of function or repair part needed.
Wiring diagram is located inside electrical control box cover.
PROBLEM
PROBABLE CAUSE
SOLUTION
1. All elements go out or fail
to heat up.
2. Some elements are on,
but others refuse to heat.
3. Elements appear hotter or
colder than usual.
4. Meat Holding Platen won’t
heat.
5. Conveyor belts won’t
advance.
6. Motor control switch
trips.
1. Unit not plugged in properly.
2. Breaker switch on wall panel tripped.
3. Broiler circuit breakers tripped.
4. Broiler on/off switch defective.
5. Main contactor not closing.
6. Main contactor not staying closed.
1. Defective element.
2. Circuit breaker tripped.
3. Loose or broken wire.
1. Supply voltage is different than the ele-
ment ratings.
1. Unit not plugged in properly.
2. Wall cicuit breaker tripped.
3. Defective thermostat/temperature con-
troller.
4. Loose or broken wire.
5. Temperature set too low.
1. Conveyor belt jammed.
2. Machine not plugged in properly.
3. Wall circuit breaker tripped.
4. Motor control switch off.
5. Motor speed dial turned to zero.
6. SCR unplugged or defective.
7. Drive chain broken.
8. Drive sprocket loose.
9. Gear motor defective.
10. Speed pot defective.
11. Loose or broken wire.
12. Motor unplugged.
1. Conveyor chains jammed.
2. SCR defective.
3. Motor brushes worn out.
4. Drive chain binding.
5. Shorted wire to motor.
6. Motor defective.
7. Switch defective.
1. Plug in properly.
2. Reset circuit breaker.
3. Reset circuit breaker.
4. Replace.
5. Replace contactor coil.
6. Replace on/off switch and check for
loose wires.
1. Replace.
2. Reset.
3. Check all wires. Tighten or replace.
1. Correct supply voltage or install ele-
ments that are rated for the supply volt-
age.
1. Plug in properly.
2. Reset circuit breaker.
3. Replace.
4. Check all wires. Tighten or replace.
5. Increase setting on digital display.
1. Remove jam. Reset motor switch.
2. Plug in properly.
3. Reset circuit breaker.
4. Turn on.
5. Increase setting.
6. Plug in or replace.
7. Repair or replace.
8 Tighten set screw on the sprocket.
9. Replace.
10. Replace.
11. Check all wires. Tighten or replace.
12. Plug in. Check for grease or dirt in the
socket.
1. Remove jam. Reset motor switch.
2. Replace.
3. Replace.
4. Adjust chain tension. Lubricate.
5. Repair wire.
6. Replace.
7. Replace.
Summary of Contents for 522E
Page 2: ...2...
Page 8: ...8 C PARTS AND LOCATION Model 732 735 Electric Feed End View...
Page 9: ...9 C PARTS AND LOCATION Model 732 735 Electric Left Side View...
Page 10: ...10 C PARTS AND LOCATION Model 732 735 Electric Right Side View...
Page 11: ...11 C PARTS AND LOCATION Model 532 535 Electric Feed End View...
Page 12: ...12 PARTS AND LOCATION Model 532 535 Electric Left Side View...
Page 13: ...13 PARTS AND LOCATION Model 532 535 Electric Right Side View...
Page 22: ...22 I WIRING DIAGRAM Models 732 735 Electric Domestic U S A...
Page 23: ...23 I WIRING DIAGRAM Models 732 735 Electric Export...
Page 24: ...24 I WIRING DIAGRAM Models 532 535 Electric Domestic...
Page 25: ...25 I WIRING DIAGRAM Models 532 535 Electric Export...
Page 26: ...26 I WIRING DIAGRAM Models 522 Electric Domestic...
Page 27: ...27 I WIRING DIAGRAM Models 522 Electric Export...