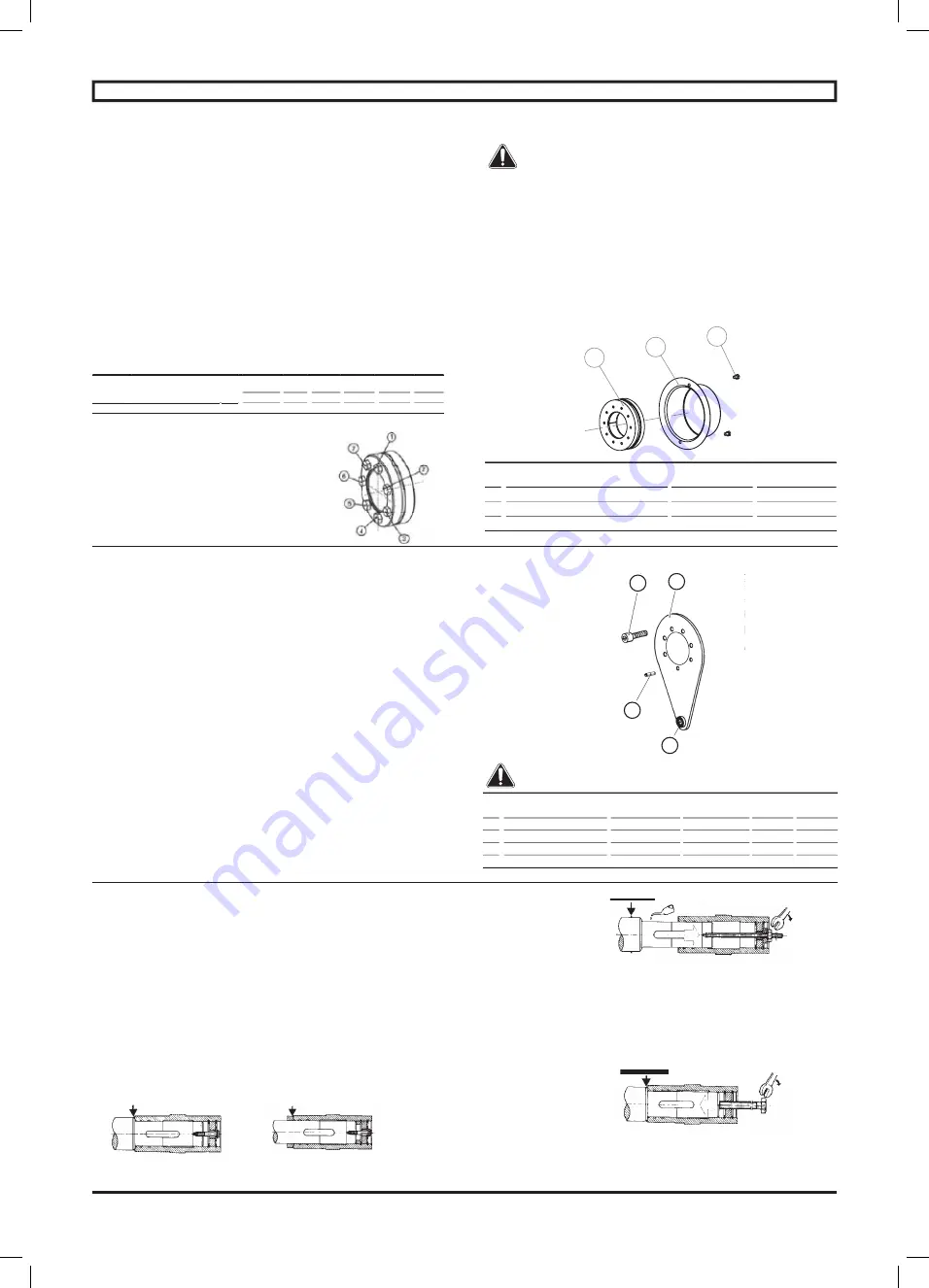
12
Installation guide - ORTHOBLOC 3000
3996 en - 2019.03 / n
4.2 - Torque arm kit
4.2.1 - Torque arm mounting
Screw the torque arm (17) on the fi xing side and machinery by
using screws (195) class 8.8 minimum (according to NFE 27-
005). Centre torque arm. Place the pin.
The screws must be stopped by an anaerobic adhesive (Loctite
Freinfi let normal 243 for example). This adhesive must resist
to vibrations and may allow dismounting of torque arm if
necessary.
Braking torque of fi xing screws
Tighten screws simultaneously and progressively.
4.2.2 - Torque arm exploded view/parts list
195
17
213
281
All the bolts must be screwed up to 70% of their
elastic strength.
Ot 3132 to Ot 3533 Ot 3633, Ot 3733
Ot 3833
Ot 3933
Rep
Description
Qty
Qty
Qty
Qty
17 Torque arm
1
1
1
1
195 Torque arm fi xing screw
3
4
8
10
213 Pin
1
1
2
2
281 Flexible mounting
1
1
1
1
4.3 - Hollow shaft
1-
Check that the cylindrical shaft has been machined in
accordance with standard NF - E 22 - 175, with a slide fi t: g6,
(the hub is: H7).
2 -
Check that the key is standard and the shaft is the minimum
length tapped at the end (O.Z).
3 -
Before mounting, degrease all the parts, taking care not to
splash any solvent on the seals.
Use grease (PAO compound) to lubricate any parts in contact,
to avoid corrosion.
Fixing on an untapped shaft Fixing on a shouldered shaft
Mounting
Mounting should be performed as described in the procedure
above, without jolting.
The gearbox is mounted on the machine shaft using a threaded
rod, screwed into the shaft.
By screwing the nut down onto the washer, the shaft is
smoothly inserted into the cylindrical hub.
Dismantling
Use a spanner with a diameter corresponding to the shaft
thread and turn until the shaft comes out.
4 - ASSEMBLY OF THE OPTIONS
4.1 - Shrink-disc Ot 3132 to Ot 3933
4.1.1 - Mounting
Remove the cover. Remove all grease from shaft and hollow
shaft bore.
1 -
Lightly oil the seating of the shrink-disc on the hollow shaft.
2 -
Draw shrink-disc onto hollow shaft. Slide shaft and hollow
shaft into one another.
3 -
Tighten diametrically opposed clamping screws by hand
whilst aligning the shrink-disc so that the clamping fl anges lie
parallel to each other.
Tighten the shrink disc screws, increasing the torque very
progressively to tightening torque indicated in the chart bellow.
It is normal that each screw must be tightened several times
until the torque is obtained.
Ot 31 to 34 Ot 35 Ot 36
Ot 37
Ot 38
Ot 39
Tightening torque for bolts of shrink-disc
Tightening torque for bolts of shrink-disc
Tightening torque for bolts of shrink-disc
Tightening torque for bolts of shrink-disc (N.m)
(N.m)
12
30
30
59
100
100
Ø shrink disc screws
M6
7xM8 10xM8 12xM10 10xM12 12xM12
Do not tighten “cross-shaped” but “in one rotation”, starting at
the top right and following sketch bellow.
Tighteness of shrink disc screws to be controlled
periodically.
Dismantling
1 -
Part-release the clamping screws evenly in stages in order
to avoid any tilting of the clamping fl anges whilst taking great
care for safety reasons that the clamping screws are not
completely released from the thread bore as the pretensions in
the shrink-disc could cause the discs to jump apart.
2 -
Draw the shrink-disc off the hollow shaft, and if applicable,
clean oxidizing on shaft and hollow shaft bore.
4.1.2 - Shrink-disc exploded view/parts list
302
016
204
Ot 3132 to Ot 3733
Ot 3833, Ot 3933
Rep
Description
Qty
Qty
16 Shrink disc cover
1
1
204 Cover fi xing screw
2
4
302 Shrink disc
1
1
O ring seal
O ring seal
O ring seal
O ring seal
DRIVE SYSTEMS - ORTHOBLOC 3000
Summary of Contents for LEROY-SOMER ORTHOBLOC 3000
Page 2: ......
Page 27: ...25 NOTES ...