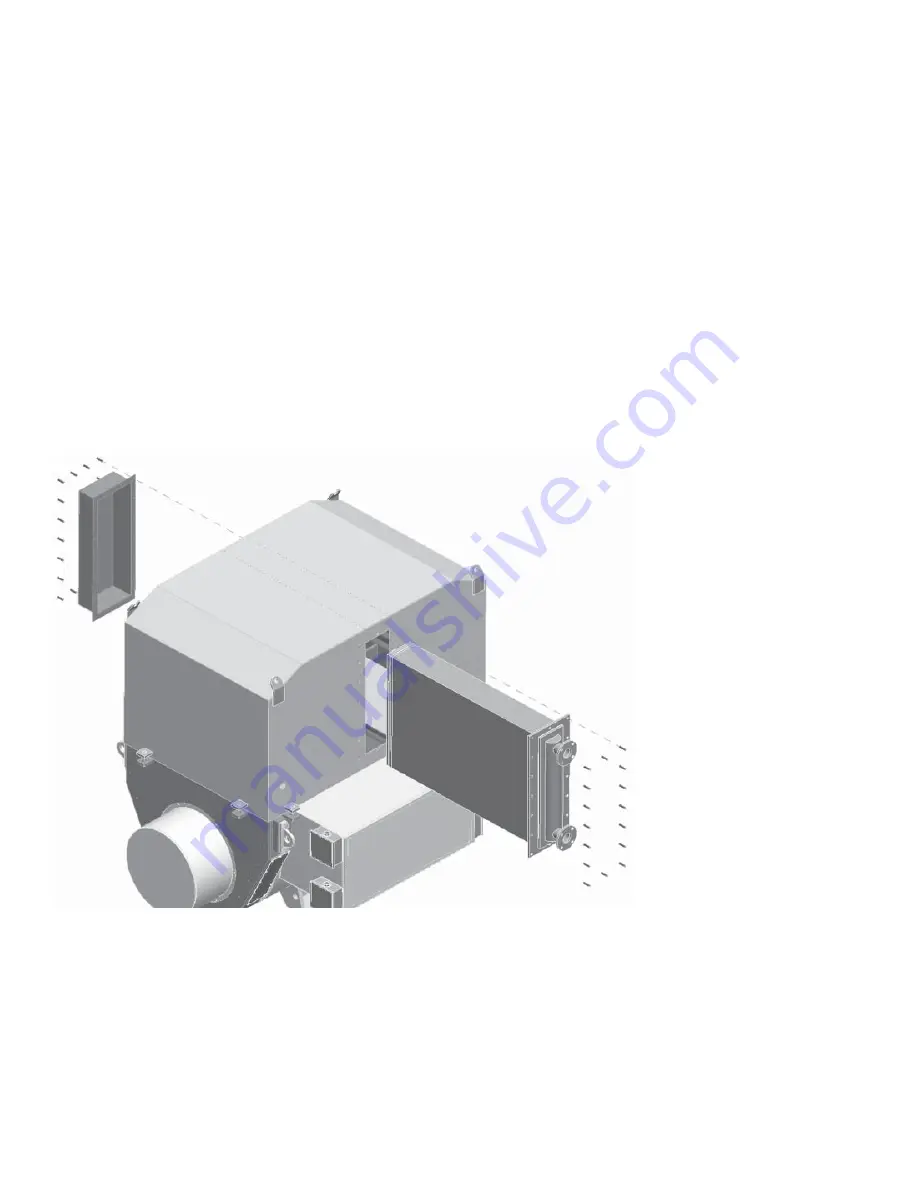
Cooler Removal
Shut off water to the cooler, and disconnect the water input and output lines from the
cooler.
Note: The cooler can usually be removed by two methods; removing the cooler by slid-
ing it out from the cooler housing, or by removing the cooler housing with the cooler
in place. See your drawings for details.
Removing the cooler leaving the cooler housing in place:
1.
Disconnect and remove the cooler RTDs and leak detector.
2.
Remove the fasteners that attach the cooler cover on the non inlet/outlet side.
3.
Remove the fasteners that attach the cooler on the inlet/outlet side.
See Figure 3.
4.
If your generator cooler is attached to a drip tray, remove the fasteners.
Figure 3
Bolt removal for cooler cover and cooler
5.
Slide the cooler out of the cooler housing. Attach a hoist with chains or a strap
suitable for lifting the cooler. See the cooler weight on your drawings or the
cooler plate. See Figure 4.
This manual show a vertically posi-
tioned cooler. Removal of a horizontally
mounted cooler is basically the same.
refer to the drawing section in your
Instruction Manual.
Use safe lifting practices to avoid dam-
age to the cooler or injury to personnel.
See the cooler weight on your draw-
ings or the cooler plate
CAUTION
The cooler is a delicate part. Be careful
not to cause tube and fi n damage on
the cooler. Damage may cause leakage
or loss of cooling ability.
Summary of Contents for 22765-01
Page 2: ......
Page 3: ......
Page 4: ......
Page 25: ......
Page 26: ......
Page 27: ......
Page 28: ......
Page 29: ......
Page 30: ......
Page 31: ......
Page 32: ......
Page 33: ......
Page 34: ......
Page 35: ......
Page 36: ......
Page 37: ......
Page 38: ......
Page 39: ......
Page 40: ......
Page 41: ......
Page 42: ......
Page 43: ......
Page 44: ......
Page 45: ......
Page 46: ......
Page 47: ......
Page 48: ......
Page 49: ......
Page 50: ......
Page 51: ......
Page 52: ......
Page 53: ......
Page 54: ......
Page 55: ......
Page 56: ......
Page 57: ......
Page 58: ......
Page 59: ......
Page 60: ......
Page 61: ......
Page 62: ......
Page 63: ......
Page 64: ......
Page 65: ......
Page 66: ......
Page 67: ......
Page 68: ......
Page 69: ......
Page 70: ......
Page 71: ......
Page 72: ......
Page 73: ......
Page 74: ......
Page 75: ......
Page 76: ......
Page 77: ......
Page 78: ......
Page 79: ......
Page 80: ......
Page 81: ......
Page 82: ......
Page 83: ......
Page 84: ......
Page 85: ......
Page 86: ......
Page 87: ......
Page 88: ......
Page 89: ......
Page 90: ......
Page 91: ......
Page 92: ......
Page 93: ......
Page 94: ......
Page 95: ......
Page 96: ......
Page 97: ......
Page 98: ......
Page 99: ......
Page 100: ......
Page 101: ......
Page 102: ......
Page 103: ......
Page 104: ......
Page 105: ......
Page 106: ......
Page 107: ......
Page 108: ......
Page 109: ......
Page 110: ......
Page 111: ......
Page 112: ......
Page 113: ......
Page 114: ......
Page 115: ......
Page 116: ......
Page 117: ......
Page 118: ......
Page 119: ......
Page 120: ......
Page 121: ......
Page 122: ......
Page 123: ......
Page 124: ......
Page 125: ......
Page 126: ......
Page 127: ......
Page 128: ......
Page 129: ......
Page 130: ......
Page 131: ......
Page 132: ......
Page 133: ......
Page 134: ......
Page 135: ......
Page 136: ......
Page 137: ......
Page 138: ......
Page 139: ......
Page 140: ......
Page 141: ......
Page 142: ......
Page 143: ......
Page 144: ......
Page 145: ......
Page 146: ......
Page 147: ......
Page 148: ......
Page 149: ......
Page 150: ......
Page 151: ......
Page 152: ......
Page 153: ......
Page 154: ......
Page 155: ......
Page 156: ......
Page 157: ......
Page 158: ......
Page 159: ......
Page 160: ......
Page 163: ...Figure 1 Typical Kato generator equipped with a water to air cooler...
Page 224: ......
Page 225: ......
Page 226: ......
Page 227: ......