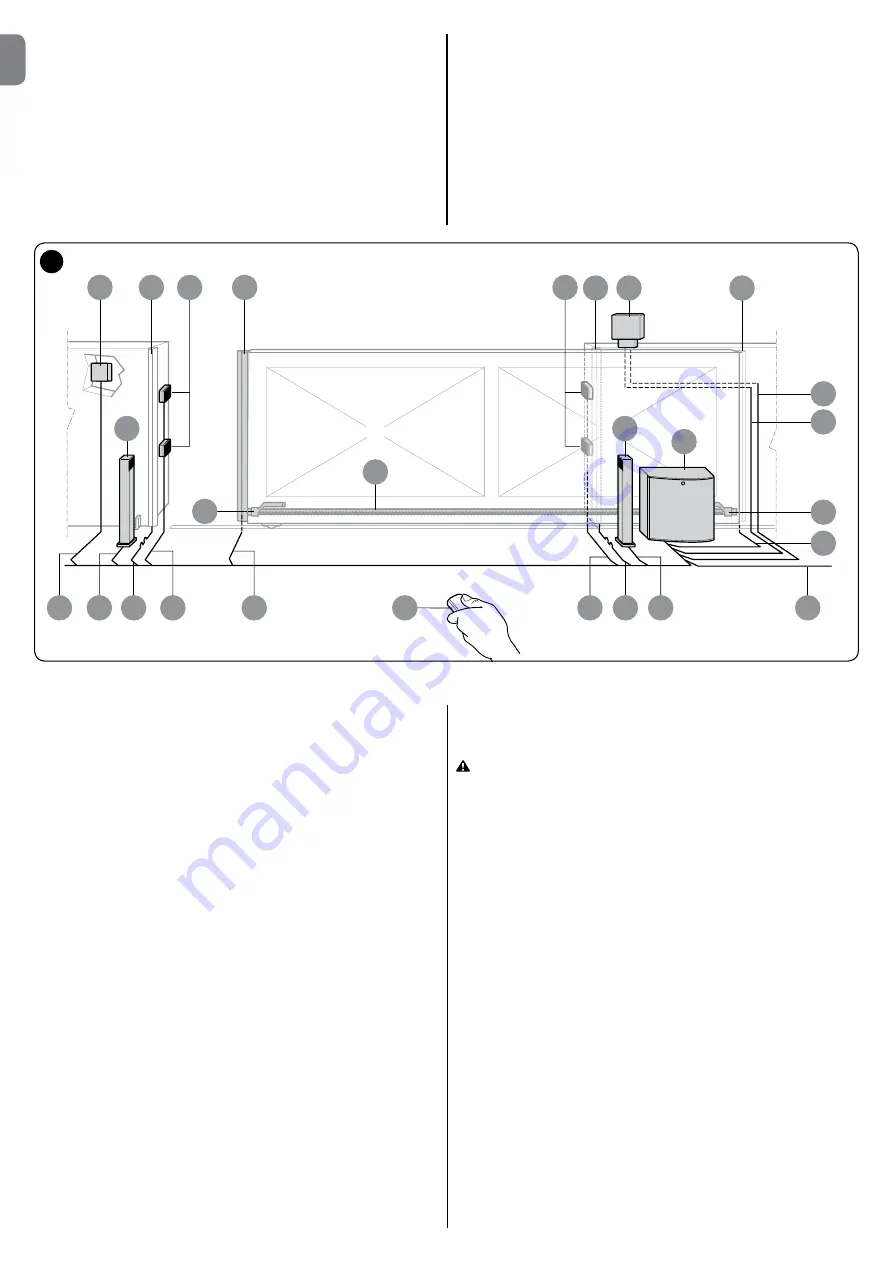
4
– English
EN
3
3
3
13
8
A
14
D
G
D
H
E
H
F
F
5
4
6
1
B
C
G
12
2
2
7
11
2
2.3 - Typical system
The
figure 2
below indicates a typical sliding gate automation system using
the TUB4000.
1
Key operated selector switch
2
Photocell on post
3
FOTO photocells
4
Main fixed edge (optional)
5
Main moveable edge
6
“Open” stop bracket
7
Rack
8
Secondary fixed edge (optional)
9
Flashing light
10
Aerial
11
Motor
12
“Closed” stop bracket
13
Secondary moveable edge (optional)
14
Radio transmitter
2.4 - Installation of the gear motor
If a base for the gear motor already exists, fixing must be performed directly to
the surface by means of expansion bolts.
If this is not so, it is necessary to:
01.
Dig an adequately large foundation hole.
02.
Prepare one or more conduits for the electrical cables as shown in
fig. 5
.
03.
Assemble the four clamps on the foundation plate setting one nut under-
neath and one on top of the plate as in
fig. 3
so that the threaded section
protrudes out of the plate as much as possible.
04.
Pour the concrete and, before it starts to harden, set the foundation plate
checking that it is parallel to the leaf and perfectly level as shown in
fig. 5
Wait for the concrete to harden completely.
05.
Remove the body from the gear motor following the procedure shown in
fig.7
in reverse order.
06.
Place the gear motor on top of the foundation plate and make sure it is
perfectly parallel to the leaf, then secure it by tightening the 4 nuts with
washers to the respective clamps as shown in
fig. 6
.
07.
Release the pinion as shown in the “Release and manual movement” para
-
graph in the Chapter “Instructions and Warnings for users of the TUB4000
gear motor”.
08.
Open the leaf up completely and place the first piece of the rack on the pi
-
nion and check that the beginning of the rack corresponds to the beginning
of the leaf. Make sure that there is at least 2÷3 mm of play between the rack
and the pinion, then fasten the rack to the leaf using suitable means.
09.
Slide the leaf, using the pinion as a reference point for the fastening the
other elements of the rack.
10.
Cut away any excess of the rack.
11.
Open and close the gate several times and make sure that the rack is ali-
gned with the pinion with a maximum tolerance of 10- 15 mm. Moreover,
check that the play of 2-3 mm between the pinion and the rack has been
respected along the entire length.
12.
Fix the two “Opening” and “Closing” limit switch brackets with the relative
dowels to the outer sides of the rack as shown in
fig. 4
. Considering that
the leaf will slide for a further 2÷3 cm after the limit switches have activated,
the brackets should be positioned at a sufficient distance from the mecha
-
nical stops.
13.
Perform the operation described in point 7 in reverse and block the pinion.
14.
Secure the body to the TUB4000 as shown in
fig. 7
and ensure that the
limit switch lever positioned above the pinion moves freely.
15.
Close the gear motor door and make sure that the safety microswitch po-
sitioned to the right of the electric motor is activated.
In order to prevent the weight of the leaf from affecting the gear
motor, it is important that there is a play of 2÷3 mm between the rack
and the pinion.
2.5 - Installation of the various devices to the control unit.
Perform the installation of all foreseen devices following the respective instruc-
tions. Check in Chapter 7 (DPRO500) which devices can be connected to the
TUB4000.
CAUTION! – The electrical connections must be performed by skilled
and qualified personnel in strict observance of current legislation,
standards and regulations with the system disconnected from elec-
tricity supply.
Summary of Contents for TUB4000
Page 2: ......
Page 8: ...6 English EN V W U L1 L2 L3 1 2 3 NDA040 4 5 6 1 2 3 A Neutral wire from the supply plug...
Page 22: ......