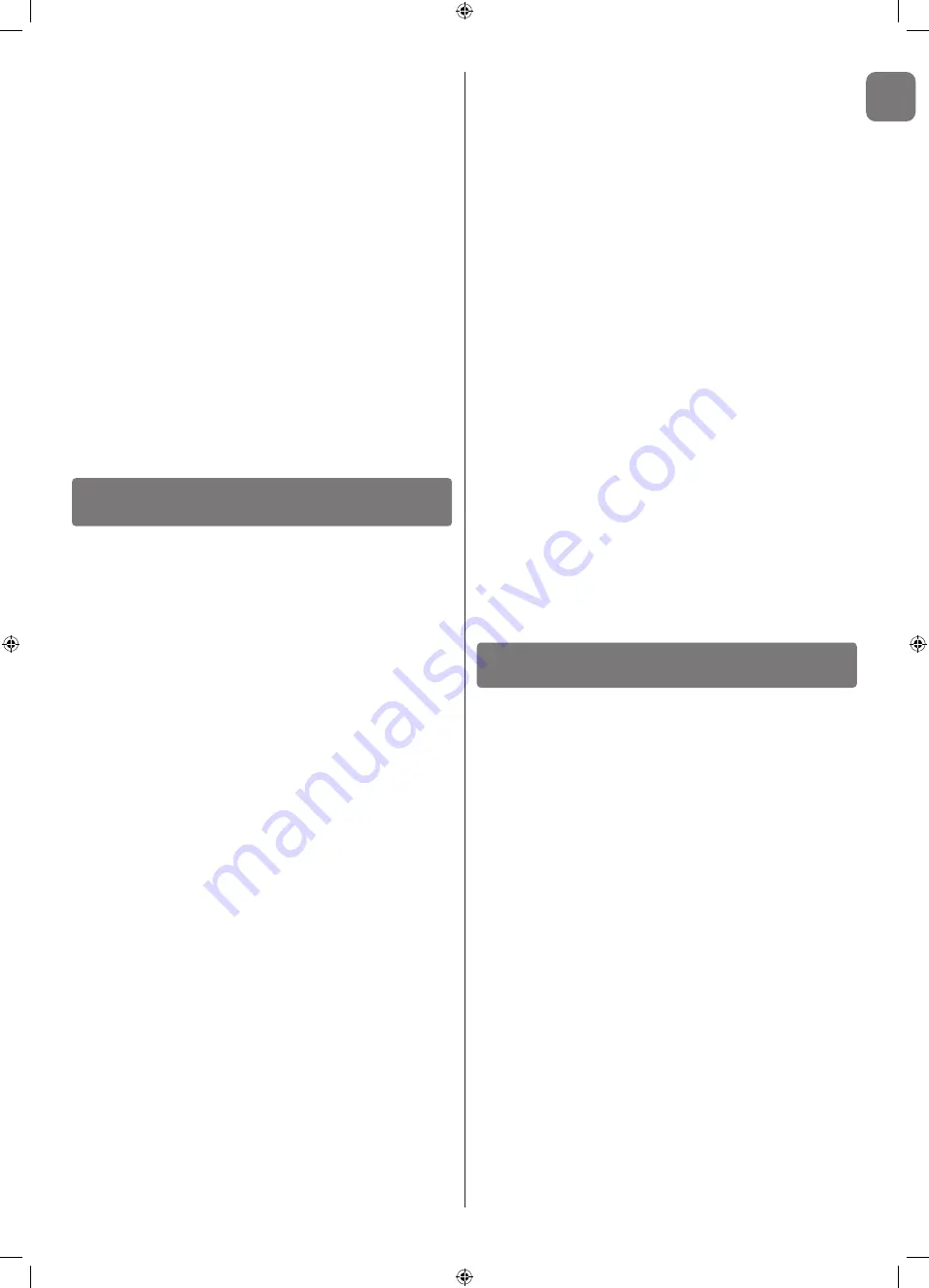
EN
English – 5
The door must be balanced in all positions when assembling the
sectional main door and balancing with the weights according to
the procedures prescribed by the standards. Correct balancing is
ascertained by manually opening and closing the door with identical
activation force in both directions.
1. Mechanical limit switches
The upper and lower deactivation positions of the door are defined
by setting the limit switch.
The gearmotor must be electrically connected for making this setting.
To access the limit switch (
Fig. 8a
: limit switch plate with 7 switches -
Fig. 8b
with 8 switches) unscrew the limit switch guard. It is possible
to move the door in dead man mode using the built-in "OPEN",
"CLOSE" and STOP buttons if the external control devices have not
yet been connected with the control station included in the supply.
Switch off the power and reverse the two L1 and L2 phases of the
gearmotor if the door does not open when pressing the "OPEN"
button.
The door must open even if the gearmotor has been installed upside
down when the "OPEN" button is pressed. Otherwise, switch off the
power and reverse the two L1 and L2 phases.
It is also necessary to properly correct the two emergency stop limit
switches so that they trip after the limit switch.
Switching off with door in low position
The limit switch for switching off with door in low position is to be set
as follows (
Fig. 7-8)
:
Move the door to the desired CLOSE position.
Set the contactor cam 3 E
white) to activate the limit switch.
Tighten the fixing screw
A
.
For accurate adjustment, turn the
screw
B
.
Move the door into the desired OPEN position
Set the contactor cam
1 E
h
(green) in order to activate the limit switch.
Tighten fixing screw A.
For accurate adjustment, turn the
screw B
.
LIMIT SWITCH SETTING
STAR/DELTA VOLTAGE CONNECTION
Warning! Danger of death due to electric shock.
Before starting the assembly operations, exclude the voltage from
the conductors and check that they are really equal to zero.
The commutability of the motor voltage makes it possible to use the
gearmotor on both a 3 x 380 V and 3 x 220 V power grid.
The motor is wired in the factory with star connection for a 3 x 380 V
power grid.
For connection to a 220 V power grid, switch the motor onto a delta
connection.
To commute the voltage onto the motor, wire the ends of the
windings as illustrated in
fig. 9-11
.
When fixing the motor cables, pay attention that the cables are long
enough to consent solid fixing, in order to create a connection able
to remain secure over time.
Pull the conductors to check if the connection is secure.
It is necessary to also adjust the gearmotor (UST1K) by commuting
the motor for connection to a 3 x 380 V power grid. To this regard,
see the UST1K.
Chain version (fig. 5a-d)
- Grasp the red handle / manual control (1) and softly pull until
stopping
- to interrupt the control voltage, and therefore prevent activation of
the door in electric mode.
- Open and/or close the door with the emergency release chain (2)
- Grasp the green handle /motor control (3) and softly pull until stopping to
restore the control voltage, and therefore once again consent operation
of the door in electric mode.
Average duration: 350 cycles!
Modification of the length of the emergency release chain
(fig. 6)
- The emergency release chain opens in the connection point and
therefore can be extended or shortened by adding or removing
links.
- The links must be carefully bent.
- When the emergency release chain length is modified, it is
necessary to pay attention not to twist it.
The safety limit switches
2 SE
and
4 SE
h
(red) must be set in order
to be released right after the overtaking of the control limit switch.
The safety limit switches
2 SE
and
4 SE
h
(red) are factory-set in order to
follow the limit switch at a short distance.
Check that the fixing screws are in the correct position after the
operation test.
The additional limit switches
8 P2
and
7 P2
h
are closing contacts with
zero potential, while the additional limit switches
6 P1
and
5 P1
h
are
switching contacts with zero potential.
In
automatic mode
limit switch 6 is used as a preliminary limit switch.
Therefore it is to be set so that it releases when the door reaches a
distance of 5 cm from the ground.
In
dead man mode
it is not necessary to set it and it is used as a
contact with zero potential.
2. Electronic limit switch (transducer absolute value)
(fig. 12-15)
The EES electronic limit switch is a positioning switch with absolute
value for rolling shutters, doors and main doors. The assessment, or
setting, of the final positions is carried out with gearmotors for doors
tuned to the EES.
During assembly simply insert the six-pole plug.
Particular mechanical settings and positionings are not needed.
The terminals for the safety chain (safety switch) are respectively
located on the EES side (
A type
) and on the plate beneath the EES
(
B type
). (
Fig. 14 and 15
)
See the EES wiring diagram in the gearmotor instruction manual for
the UST1K doors.
Summary of Contents for RDF-1100-10
Page 28: ......
Page 29: ......
Page 31: ...26 RDF 1400 24 KU RDF 1400 24 KE2 15...
Page 32: ...25 RDF 1250 24 KU RDF 1250 24 KE2 15...
Page 33: ...24 RDF 950 24 KU RDF 950 24 KE2 15...
Page 34: ...23 RDF 750 24 KU RDF 750 24 KE2 15...
Page 35: ...22 RDF 500 24 KU RDF 500 24 KE2 12...
Page 36: ...21 12 RDF 350 24 KU RDF 350 24 KE2...
Page 37: ...20 RDF 250 24 KU RDF 250 24 KE2 12...
Page 38: ...19 RDF 1400 7 KU RDF 1400 7 KE2 15...
Page 39: ...18 RDF 850 1100 10 KU RDF 850 1100 10 KE2 15...
Page 40: ...17 RDF 750 9 5 KU RDF 750 9 5 KE2 15...
Page 41: ...16 12 RDF 550 12 KU RDF 550 12 KE2...
Page 42: ...15 RDF 380 450 15 KU RDF 380 450 15 KE2 12...
Page 43: ...14 12 elektronische Endschalter mechanische Endschalter RDF 220 290 15 KU RDF 220 290 15 KE2...
Page 44: ...13 RDF 140 20 KU RDF 140 20 KE2 10...
Page 45: ...12...
Page 46: ...11...
Page 47: ...10...
Page 49: ...8 5 5 8 8 2 8 2 7 1 6 1 5 4 3 2 1 6 7 7 8 2 7 2 6 1 5 4 3 2 1...
Page 50: ...7 Gr n 20 1 3 4 2 5 5...
Page 53: ...4 VDE 0113 4 1 2...
Page 54: ...3 1 1 Nice Service Center 2 1 20 2 5 1 3 MAINTENANCE IN PROGRESS Nice 60 3 1 Nice III s...