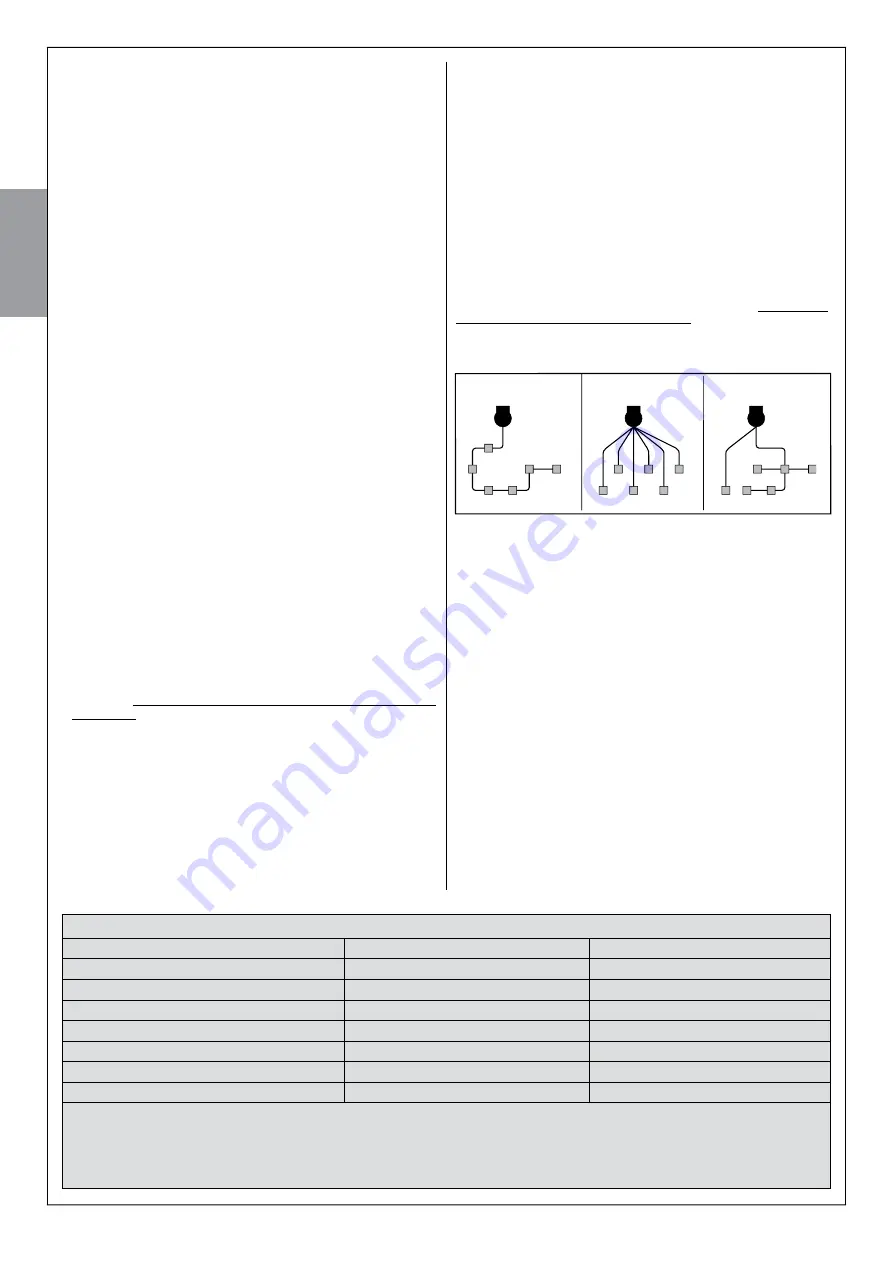
4
– English
English
––– STEP 4 –––
4.1 - WORKS PRIOR TO INSTALLATION
4.1.1 - Establish the position of the devices in the system
With reference to
fig. 1
and
fig. 5
, locate the approximate position for
installation of each device envisaged in the system. The
fig. 1
shows
a system built with this product plus other optional accessories from
the Nice Home line. The various elements are positioned according to a
standard and usual layout. The devices used are:
a)
- 1 FL200 flashing indicator with built-in antenna
b)
- 1 pair of PH200 photocells (made up of a TX and an RX)
c)
- MAESTRO200C gearmotor with incorporated CL205 control unit
d)
- MAESTRO200M gearmotor
e)
- Closure stop (not supplied)
WARNING! - Some of these devices are optional and may not be
present in this package (see the Nice Home product catalogue).
WARNINGS:
• The gearmotors must be affixed to the column/wall, laterally to the
respective gate leaves;
• Fixed type control devices must be positioned:
- in view of the automation;
-
away from its moving parts;
- at a minimum height of 1.5 m from the floor/ground;
- not accessible to strangers.
4.1.2 - Establish the position of all the connecting cables
Refer to the instructions in section 4.2 to determine the space in which to
dig the routes for the cable ducts for the electrical cables.
4.1.3 - Obtain the tools and materials required for the work
Before beginning work, make sure you have all the tools and materials
required to carry out the work. Make sure that these are in good condi-
tion and comply with local safety regulations.
4.1.4 - Carry out the preparatory works
Prepare the environment for the subsequent installation of the devices,
carrying out preliminary work such as, for example:
- excavation of routes for the cable ducting for the electrical cables (alter-
natively, external raceways may be used);
- installation of the cable ducting and their attachment in the concrete;
- sizing of all electrical cables to the desired length (see section 4.2) and
their passage in the ducting.
Caution! - At this stage do not implement any type of electrical
connection.
Warnings
:
• Ducting and raceways are used to protect the electrical cables from
damage due to accidental impacts.
• When laying the ducting, also take into account that due to possible
deposits of water in the routing ducts, the ducting might create con-
densation in the control unit, with consequent damage to the electronic
circuits.
• Place the ends of the ducting in the vicinity of the points provided for
affixing the devices.
4.2 - ELECTRICAL CABLES PREPARATION
To prepare all connection cables, proceed as follows.
a)
- Observe
fig. 5
to understand how the various devices should be
connected to the control unit and the terminals to be used for each
connection.
Important
- Only devices which support “ECSbus”
technology can be connected to the “ECSbus” terminal.
b)
- Observe
fig. 1
to understand how to position the electrical cables in
the environment. Then, draw a similar diagram on paper, adapting
it to the specific needs of your system.
Note
- This diagram will be
useful, both to guide the excavation of the routes for the cable duct-
ing, and for drawing up a complete list of the cables required.
c)
- Read
Table 2
to determine the type of cables to use; then use the
diagram you just drew and the environmental measurements to
determine the length of each individual cable.
Caution! - Each cable
must not exceed the maximum length indicated in Table 2.
WARNING
-
The “ECSbus” technology allows you to connect multiple
devices together, using, between one device and the next, a single “bus”
cable, with two internal electrical conductors. The connection between
the devices can adopt a “
cascade
”, a “
star
” or a “
mixed
” configuration,
between the first two.
cascade
star
mixed
TABLE 2 – Technical specifications of electric cables
Connection
Cable type
(minimum gauge values)
Maximum admissible length
A
- Electric power line
Cable 3 x 1.5 mm
2
30 m
(note 1)
B
- FLASH flashing indicator output
Cable 2 x 1 mm
2
6 m
C
- Antenna cable
RG58 type shielded cable
20m
(less than 5m recommended )
D
- ECSbus devices cable
Cable 2 x 0.5 mm
2
20 m
(note 2)
- STOP input
Cable 2 x 0.5 mm
2
20 m
(note 3)
- SbS input
Cable 2 x 0.5 mm
2
20 m
(note 3)
E
- Gearmotor power supply cable
Cable 3 x 1.5 mm
2
10 m
Note 1
- A power supply cable longer than 30m may be used provided it has a larger gauge (3 x 2.5mm
2
), and that a safety earthing system is
provided near the automation.
Note 2
- If the “ECSbus” cable is longer than 20m, up to 40 m, a larger gauge (2 x 1mm
2
) cable is needed.
Note 3
- These two cables may be replaced by a single 4 x 0.5 mm
2
cable.
CAUTION! – The cables used must be suited to the type of environment of the installation site.
Summary of Contents for MAESTRO200 Series
Page 2: ......
Page 9: ...Français 7 Français E B A 6 Distance E minimum 400 mm 8 9 M8 V6 x 70 M6 10 11 12 13 7 ...
Page 10: ...8 Français Français OK b c d a Maximum 14 14 15 16 17 18 19 21 20 M8 M8 M8 M8 ...
Page 33: ...English 7 English E B A 6 Distance E minimum 400 mm 8 9 M8 V6 x 70 M6 10 11 12 13 7 ...
Page 34: ...8 English English OK b c d a Maximum 14 14 15 16 17 18 19 21 20 M8 M8 M8 M8 ...
Page 57: ...Italiano 7 Italiano E B A 6 Distanza E minimo 400 mm 8 9 M8 V6 x 70 M6 10 11 12 13 7 ...
Page 58: ...8 Italiano Italiano OK b c d a Massimo 14 14 15 16 17 18 19 21 20 M8 M8 M8 M8 ...
Page 81: ...Polski 7 Polski E B A 6 Odległość E minimum 400 mm 8 9 M8 V6 x 70 M6 10 11 12 13 7 ...
Page 82: ...8 Polski Polski OK b c d a Maksymalny 14 14 15 16 17 18 19 21 20 M8 M8 M8 M8 ...
Page 111: ......