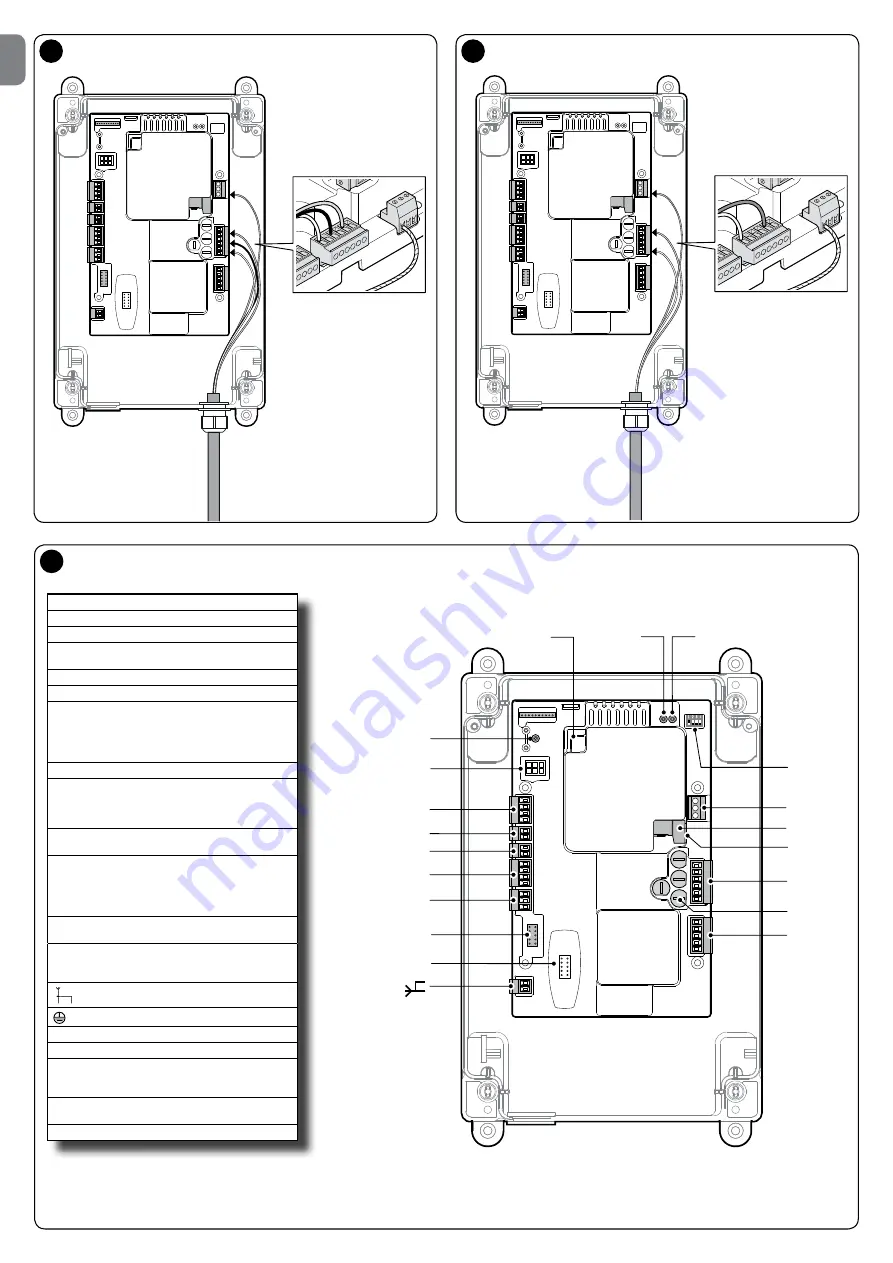
8
– English
EN
V
W
U
L1
L2
L3
3 L
2 L
1 L
U
V
W
1 2
3
BRAKE
BOOST
6
V
W
U
L1
L2
L3
3 L
2 L
1 L
U
V
W
1 2
3
BRAKE
BOOST
5
V
W
U
L1
L2
L3
MOTOR
LINE
PE
BOOST
BRAKE
LED SAFETY
LED L2
LED L1
OUT
FUSES
ALT
INPUT
SAFE
STOP
LIMIT SWITCH
IBT4N
OXI
ENCODER
PROG
7
SAFETY LED
=
safety chain LED
L2 LED
=
OK LED (green)
L1 LED
=
Warning LED (red)
OUT
=
slot for the NDA040 accessory
board for expanding outputs
PROG
=
DIP switch for programming
ENCODER
=
electronic limit switch
INPUT
=
external inputs
8 - com (+24 V DC common)
9 - open
10 - close
11 - photo (ing1)
ALT
=
ALT terminal
SAFE
=
only for motors with mechani-
cal limit switches (leave uncon-
nected with motors which have
electronic limit switches)
LIMIT
SWITCH
=
mechanical limit switch
STOP
=
STOP terminal used for 8K2
safety edge or OSE
5 - positive (+) safety edge
6 - safety edge signal
7 - negative GND (-)
IBT4N
=
IBT4N interface connector (not
supplied)
OXI
=
connector for connecting radio
receivers with SM plug (SMXI/
OXI)
=
aerial
PE
=
earth connection
BOOST
=
starting capacitor
BRAKE
=
motor brake
LINE
=
connector for connecting the
three-phase or single-phase
power line
FUSES
=
F1, F2, F3, F4: see Technical
Specifications
MOTOR
=
motor
(+ com)
(– GND)
Summary of Contents for D-Pro Action Series
Page 2: ......