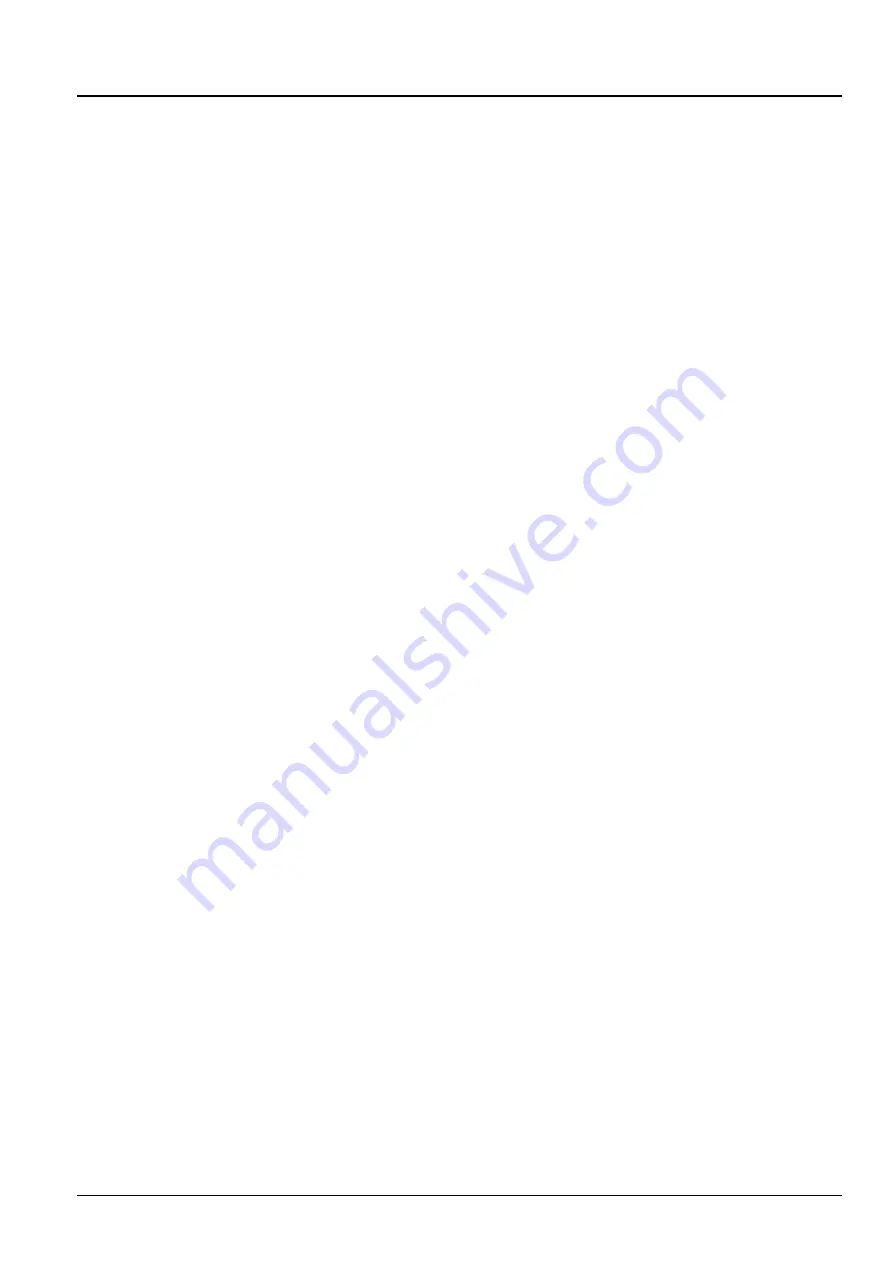
Electrical systems - FAULT CODES
DTC 4E3-12-Level 2 Monitoring : Diagnosis fault check to report the
error to demand for an ICO due to an error in the PoI3 efficiency
factor
Control Module : ECU
Context:
The Engine Control Unit (ECU) A-9000 performs a diagnostic fault check for post injection 3. If the ECU A-9000
determines that there is a post injection 3 plausibility error, this fault will occur.
Solution:
1. Check the ECU A-9000 for the appropriate software and re-flash, if necessary.
A. If the fault has been resolved, return the machine to service.
B. If the fault has not been resolved, escalate an ASIST concern.
47866583_ 02/12/2015
55.12 [55.DTC] / 239
Summary of Contents for Workmaster 50
Page 2: ...SERVICE MANUAL Workmaster 50 Workmaster 60 Workmaster 70 47866583_ 02 12 2015 EN ...
Page 7: ...47866583_ 02 12 2015 ...
Page 8: ...INTRODUCTION 47866583_ 02 12 2015 1 ...
Page 12: ...INTRODUCTION Advice BT09A213 1 47866583_ 02 12 2015 5 ...
Page 20: ...SERVICE MANUAL Engine Workmaster 50 Workmaster 60 Workmaster 70 47866583_ 02 12 2015 10 ...
Page 53: ...47866583_ 02 12 2015 10 3 10 202 10 ...
Page 59: ...47866583_ 02 12 2015 10 4 10 206 6 ...
Page 65: ...47866583_ 02 12 2015 10 5 10 216 6 ...
Page 73: ...47866583_ 02 12 2015 10 6 10 310 8 ...
Page 80: ...47866583_ 02 12 2015 10 7 10 400 7 ...
Page 82: ...SERVICE MANUAL Clutch Workmaster 50 Workmaster 60 Workmaster 70 47866583_ 02 12 2015 18 ...
Page 98: ...Clutch Clutch and components GNIL14TR04659GB 1 47866583_ 02 12 2015 18 2 18 110 5 ...
Page 116: ...SERVICE MANUAL Transmission Workmaster 50 Workmaster 60 Workmaster 70 47866583_ 02 12 2015 21 ...
Page 121: ...Transmission Mechanical transmission GNIL14TR00824GA 1 47866583_ 02 12 2015 21 1 21 114 4 ...
Page 157: ...47866583_ 02 12 2015 21 2 21 130 10 ...
Page 199: ...Contents Four Wheel Drive 4WD system 23 23 314 Drive shaft 23 1 47866583_ 02 12 2015 23 ...
Page 216: ...Front axle system Powered front axle GNIL14TR04347HA 2 47866583_ 02 12 2015 25 1 25 100 7 ...
Page 241: ...47866583_ 02 12 2015 25 1 25 100 32 ...
Page 247: ...47866583_ 02 12 2015 25 2 25 102 6 ...
Page 255: ...47866583_ 02 12 2015 25 3 25 108 8 ...
Page 263: ...47866583_ 02 12 2015 25 4 25 310 8 ...
Page 330: ...47866583_ 02 12 2015 27 3 27 120 15 ...
Page 363: ...Contents Brakes and controls 33 33 120 Mechanical service brakes 33 1 47866583_ 02 12 2015 33 ...
Page 395: ...47866583_ 02 12 2015 35 1 35 000 10 ...
Page 421: ...Hydraulic systems Main lift system GNIL14TR04655FB 4 47866583_ 02 12 2015 35 2 35 100 26 ...
Page 433: ...47866583_ 02 12 2015 35 3 35 104 8 ...
Page 445: ...47866583_ 02 12 2015 35 4 35 204 12 ...
Page 451: ...47866583_ 02 12 2015 35 5 35 300 6 ...
Page 463: ...Hydraulic systems Main control valve GNIL14TR00834GA 1 47866583_ 02 12 2015 35 7 35 359 4 ...
Page 466: ...Hydraulic systems Main control valve GNIL14TR00836GA 3 47866583_ 02 12 2015 35 7 35 359 7 ...
Page 470: ...47866583_ 02 12 2015 35 7 35 359 11 ...
Page 472: ...SERVICE MANUAL Steering Workmaster 50 Workmaster 60 Workmaster 70 47866583_ 02 12 2015 41 ...
Page 478: ...Steering Steering control GNIL14TR04488JB 2 47866583_ 02 12 2015 41 1 41 101 5 ...
Page 479: ...Steering Steering control 47866583_ 02 12 2015 41 1 41 101 6 ...
Page 528: ...47866583_ 02 12 2015 41 4 41 216 11 ...
Page 530: ...SERVICE MANUAL Wheels Workmaster 50 Workmaster 60 Workmaster 70 47866583_ 02 12 2015 44 ...
Page 531: ...Contents Wheels 44 44 511 Front wheels 44 1 44 520 Rear wheels 44 2 47866583_ 02 12 2015 44 ...
Page 541: ...47866583_ 02 12 2015 44 1 44 511 10 ...
Page 546: ...Index Wheels 44 Rear wheels 520 Rear wheel Adjust 3 47866583_ 02 12 2015 44 2 44 520 5 ...
Page 570: ...Electrical systems Harnesses and connectors SHT_2 1 47866583_ 02 12 2015 55 4 55 100 5 ...
Page 572: ...Electrical systems Harnesses and connectors SHT_3 1 47866583_ 02 12 2015 55 4 55 100 7 ...
Page 574: ...Electrical systems Harnesses and connectors SHT_4 1 47866583_ 02 12 2015 55 4 55 100 9 ...
Page 576: ...Electrical systems Harnesses and connectors SHT_5 1 47866583_ 02 12 2015 55 4 55 100 11 ...
Page 578: ...Electrical systems Harnesses and connectors SHT_6 1 47866583_ 02 12 2015 55 4 55 100 13 ...
Page 580: ...Electrical systems Harnesses and connectors SHT_7 1 47866583_ 02 12 2015 55 4 55 100 15 ...
Page 582: ...Electrical systems Harnesses and connectors SHT_8 1 47866583_ 02 12 2015 55 4 55 100 17 ...
Page 584: ...Electrical systems Harnesses and connectors SHT_9 1 47866583_ 02 12 2015 55 4 55 100 19 ...
Page 586: ...Electrical systems Harnesses and connectors SHT_10 1 47866583_ 02 12 2015 55 4 55 100 21 ...
Page 588: ...Electrical systems Harnesses and connectors SHT_11 1 47866583_ 02 12 2015 55 4 55 100 23 ...
Page 590: ...Electrical systems Harnesses and connectors SHT_12 1 47866583_ 02 12 2015 55 4 55 100 25 ...
Page 597: ...Electrical systems Harnesses and connectors 47866583_ 02 12 2015 55 4 55 100 32 ...
Page 667: ...47866583_ 02 12 2015 55 4 55 100 102 ...
Page 715: ...47866583_ 02 12 2015 55 10 55 408 18 ...
Page 1032: ...47866583_ 02 12 2015 55 12 55 DTC 311 ...
Page 1049: ...47866583_ 02 12 2015 90 2 90 110 6 ...
Page 1062: ...47866583_ 02 12 2015 90 4 90 118 7 ...
Page 1066: ...47866583_ 02 12 2015 ...