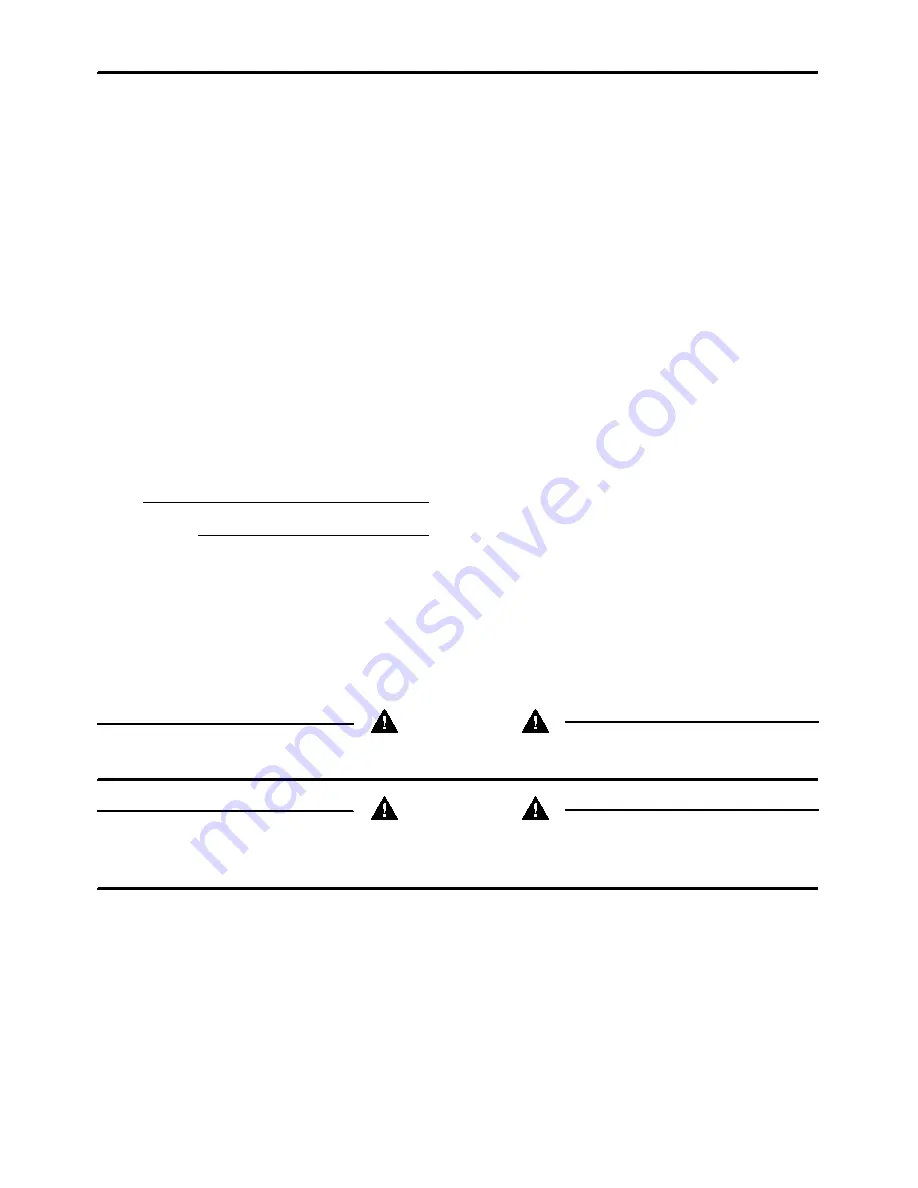
0-1
fully and keep it available for ready reference.
mended and approved by New Holland should be used with your tractor.
questions that may arise regarding the operation of your tractor.
tion of the model and serial numbers of your skid steer.
carefully read the message that follows and be alert to the possibility of personal injury or death.
Summary of Contents for TC21D
Page 19: ...0 18 N O T F O R R E P R O D U C T I O N...
Page 23: ...SECTION 1 GENERAL INFORMATION 1 4 N O T F O R R E P R O D U C T I O N...
Page 51: ...SECTION 2 OPERATION 2 28 N O T F O R R E P R O D U C T I O N...
Page 87: ...SECTION 3 LUBRICATION AND MAINTENANCE 3 36 N O T F O R R E P R O D U C T I O N...
Page 99: ...4 12 N O T F O R R E P R O D U C T I O N...
Page 101: ...4 14 N O T F O R R E P R O D U C T I O N...
Page 102: ...104 4 02 2002 NEW HOLLAND NORTH AMERICA INC N O T F O R R E P R O D U C T I O N...