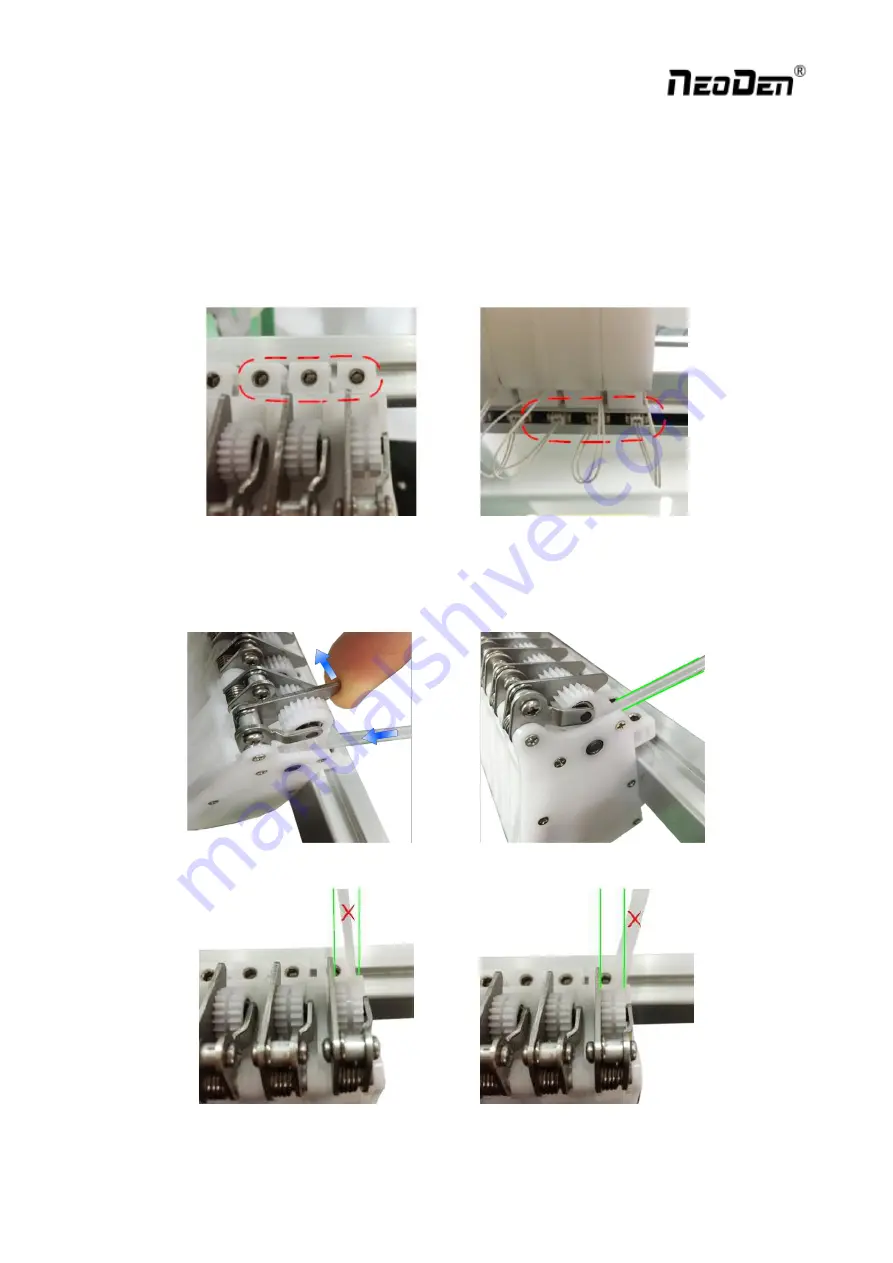
31
3. Structure and maintenance instruction
3.1. Structure Chart
3.1.1. Peel Box
1) Fixation of Peel box
Fix the peel boxes on support bar and plug wires into connectors one by one.
And the ID of each peel box can be changed accordingly.
2) Load Cover Tape
Uplift the gear, while insert the cover tape into it and make sure the cover tape is flat but not kinked.