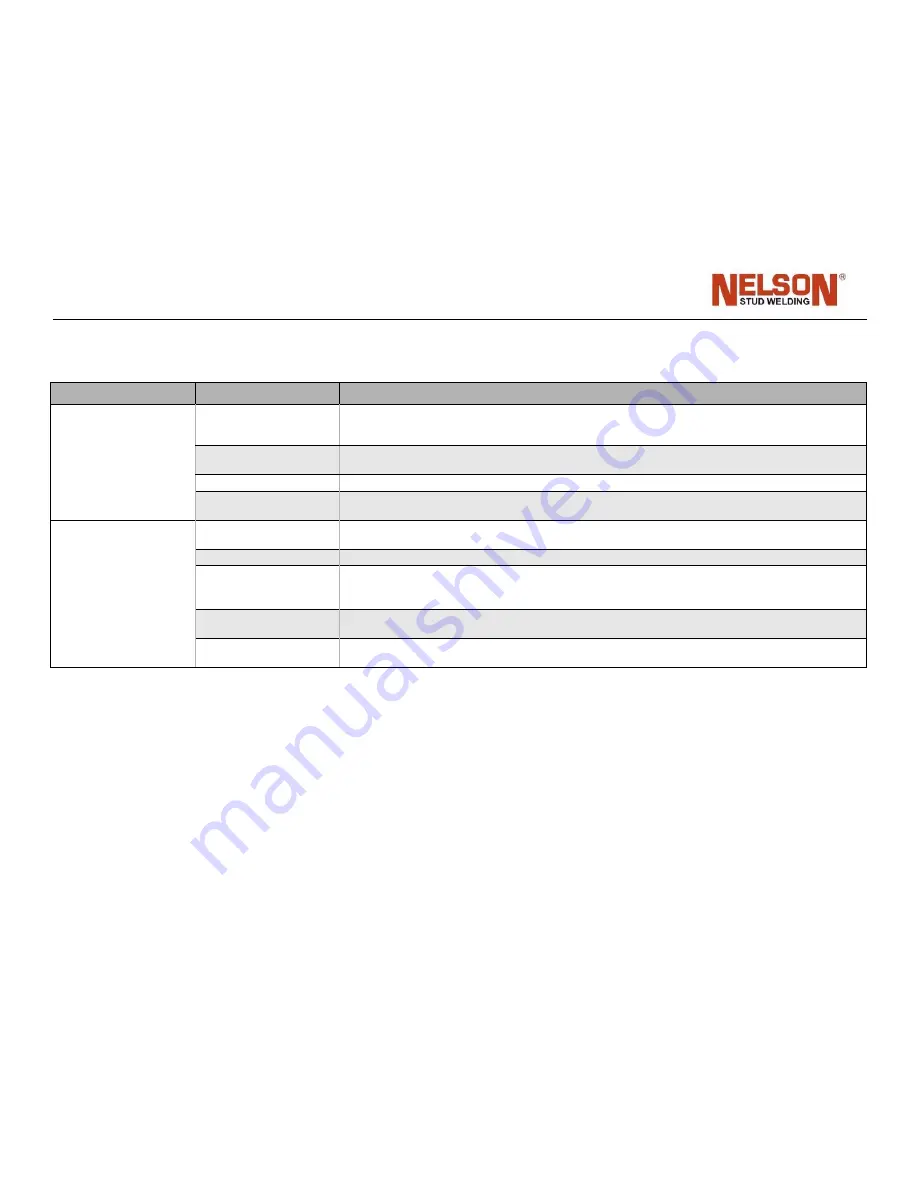
Stud welding unit N1500i
Version 1.31 7.June.2013
Manual part number: 729-110-027
31
Nelson Stud Welding, Inc. • 7900 West Ridge Road • Elyria, Ohio 44035 • USA
3.3
Weld Process Problems
Problem
Possible Cause
Solution
Weld appears “hot”
Time setting or current set-
ting is too high.
Check the stud burn-off. If the burn-off is much greater than what is typical for that diameter stud, the time and
current settings may not be correct. Ensure proper current and time settings are being used. Reduce the current
setting and perform weld inspections.
Plunge is too short.
Plunge is measured by the amount of stud protruding beyond the bottom edge of the ferrule. Ensure proper
plunge settings are being used, and correct, if necessary.
Incorrect ferrule.
Ensure that the ferrule being used in the welding process is the proper ferrule for the stud size and application.
Plunge dampening is too
great.
If the gun is a Heavy Duty gun, it is equipped with Tranquil Arc®. Back out the clear plastic plunge dampener
housing to decrease the free travel.
Weld appears “cold”
Time setting or current set-
ting is too low.
Check the stud burn-off. If the burn-off is much less than what is typical for that diameter stud, the time and cur-
rent settings may not be correct. Ensure proper current and time settings are being used.
Incorrect ferrule.
Ensure that the ferrule being used in the welding process is the proper ferrule for the stud size and application.
Inconsistent gun lift.
Perform a Lift Check. Ensure proper lift settings are being used. Correct the lift to the proper setting if the lift is
improperly set.
Perform weld inspections.
Inconsistent gun lift.
Perform a Lift Check, several times. Ensure proper lift settings are being used. If lift results are inconsistent, disas-
semble and clean the gun.
Too much plunge.
Plunge is measured by the amount of stud protruding beyond the bottom edge of the ferrule. Ensure proper
plunge settings are being used, and correct, if necessary.