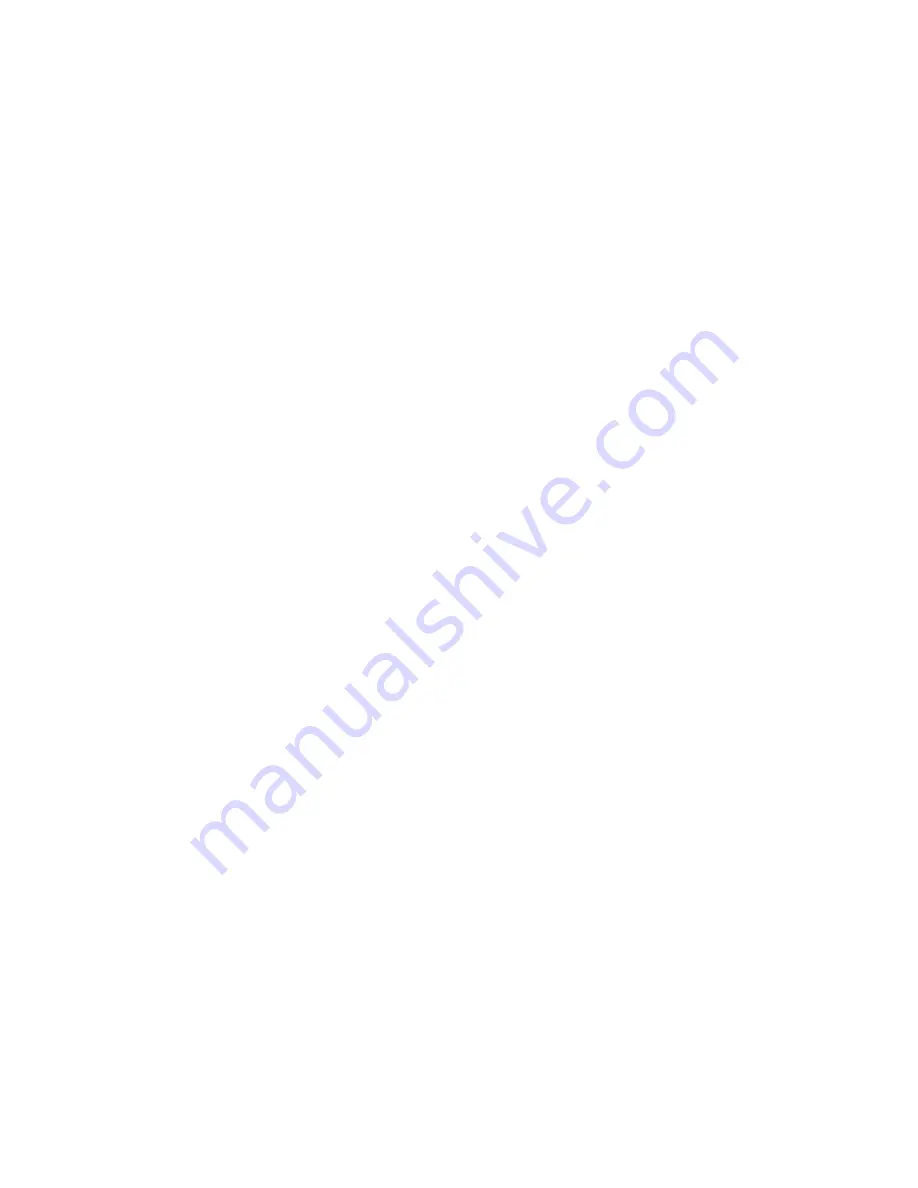
MINOR ADJUSTMENTS IN THE UPPER GROUP OF THE
ZIG-ZAG MECHANISM
When the needle positioning lever no. A85662 is in the center
notch and the zig-zag stitch lever handle No. 85620 is set at " O ",
namely at the extreme left (after the cams have been
removed
from the machine), the needle must be in the center of the hole
of the zig-zag stitch needle plate. If the needle is not in the center
of the hole, make the adjustment as explained in chapter " Im-
portant adjustments to be made after re-assembling the
upper
group of the zig-zag mechanism ".
The machine runs noisily when sewing zig-zag with
disconnected
" automatic " mechanism. The cause of the noise can be
located
somewhere in the upper group of the zig-zag mechanism, and
it
is advisable to check all the connections between the various
parts,
to see whether any undue play sxists. Dismantle mechanism
and
check if and where excessive play exists. Especially check
the
fit of the sector No, 26106 and the roller No. 26105. If necessary,
replace the worn-out parts with new ones.
Zig-zag sewing is noisy due to excessive play between the
gears
No. 26240 and No. C 85664. To adjust, proceed as follows:
loosen
screw No. 048050 GEB which holds the gear No. C 85664 in the
arm. By means of a screw-driver, to be inserted in the notch at
the upper end of the gear No. C 85664 (Fig. 53), turn slightly the
eccentric support of this gear clockwise; the gear No. C 85664
will then get closer to the gear No. 26240 and the play between
the two gears will thus be reduced. Tighten the screw No. 048050
GEB firmlv after this adjustment.
59
Copyright -2004
Summary of Contents for Supernova
Page 1: ...Instructions For Servicing The Necchi Supernova Sewing Machine 1 Copyright 2004...
Page 15: ...15 Copyright 2004...
Page 17: ...Fig 11 Fig 12 Fig 13 17 Copyright 2004...
Page 23: ...False needle Fig 18 False needle Fig 19 23 Copyright 2004...
Page 43: ...Fig 38 43 Copyright 2004...
Page 49: ...49 Copyright 2004...