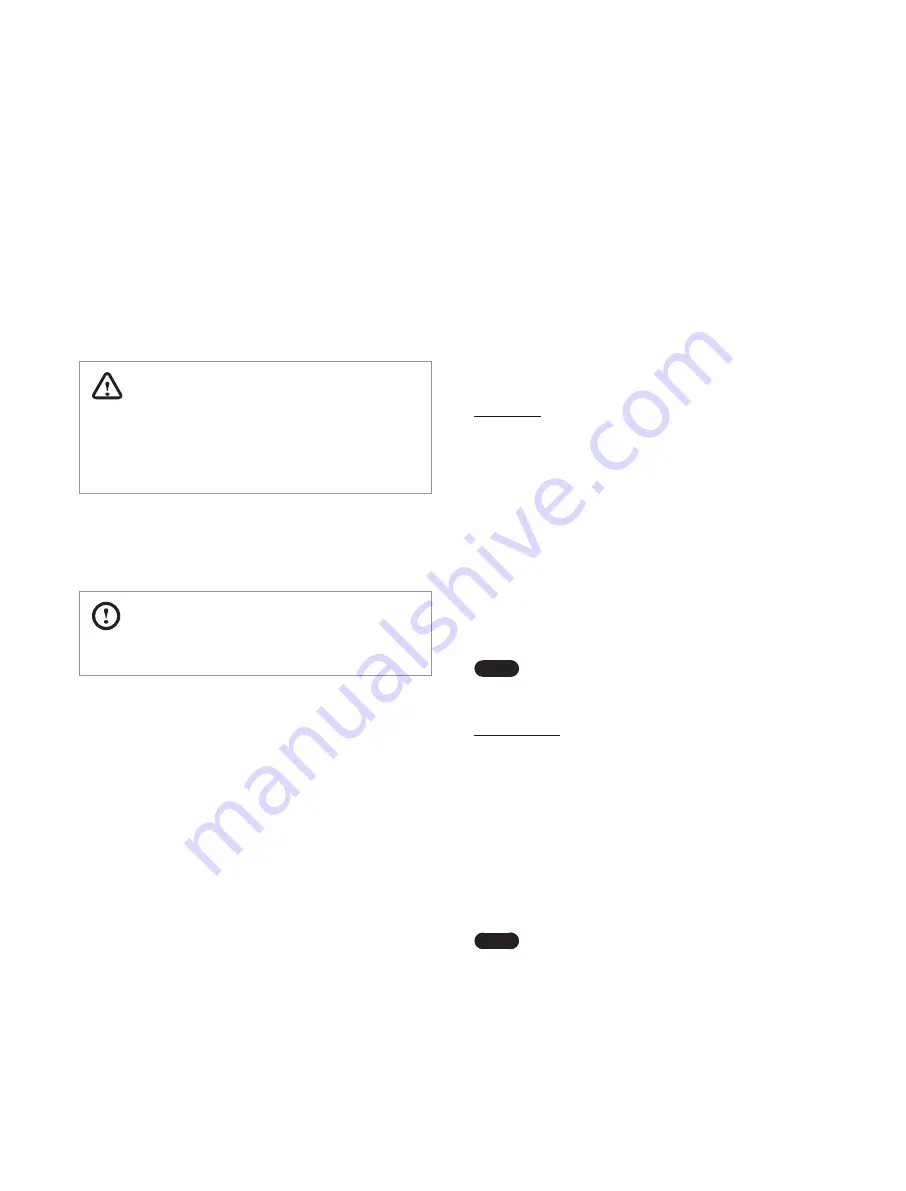
31
Installing the System Piping
2. Close the manual and automatic air vents and the boiler drain
valve.
3. Fill the boiler to the correct system pressure. The correct
pressure will vary with each application. The typical cold water
fill pressure for a residential system is 12 psi. The pressure
will rise when the boiler is turned on and the system water
temperature increases. The operating pressure must never
exceed the relief valve pressure setting.
4. At initial fill and during boiler start-up and testing, check
the system thoroughly for leaks. Repair any leaks before
proceeding further.
WARNING
Eliminate all system leaks. The continual introduction of fresh
makeup water will reduce boiler life. Minerals can build up in
the heat exchanger, reducing heat transfer, overheating the
heat exchanger and causing heat exchanger failure.
The system may have residual substances that could affect water
chemistry. After the system has been filled and leak tested,
verify that water pH and chlorine concentrations are within the
acceptable range by performing sample testing.
CAUTION
Purge the air inside the system to avoid damage to the boiler.
3.5 Considerations for System Applications
Read and follow the guidelines listed below when installing system
piping for the Navien NFB boiler:
Ɣ
System application drawings are intended to explain the system
piping concept only.
Ɣ
When installing a mixing valve on the DHW piping, ensure that
the cold water pressure does not exceed the hot water pressure.
Ɣ
For the upstream side of all pumps, use straight pipes with a
minimum inside diameter of
1
/
2
in (12 mm).
Ɣ
Provide a system expansion tank following the guidelines on
page 22.
Ɣ
System installations must comply with all local codes.
Air Removal
The boiler and system piping layout must be configured to
promote the removal of air from the system. Air vents and bleeders
must be strategically placed throughout the system to aid in
purging the air from the system during commissioning of the
boiler. The system must also employ the use of an air removal
device, such as an air scoop or an air eliminator designed to
remove the air from the water as it flows through the system.
Follow the installation instructions included with the air removal
device when placing it in the system; air removal devices generally
work better when placed higher in the system. Always locate air
removal devices in areas of the system that have a guaranteed
positive pressure, e.g., in close proximity to the water fill and
expansion tank.
Note
Connecting an air vent on top of the boiler is
recommended.
Expansion Tank
The expansion tank must be sized in accordance with the water
volume of the system as well as the firing rate of the appliance.
It is important to locate the expansion tank, and make-up water
connection, on the inlet side of any pump in the system, as doing
so will guarantee the lowest pressure in the system will be at least
equal to the tank and make-up water pressure.
Ensure the expansion tank cannot become isolated from the
boiler anytime the system is operating. Failure to follow these
instructions may lead to discharge from the pressure relief valve,
which may result in property damage or injury.
Note
The installation of check valves, motorized valves or
other shutoff devices (other than for the purpose of
servicing) are not permitted between the location of
the “Closely Spaced Tees” and the expansion tank.
Summary of Contents for NHB Series
Page 120: ...120 Appendixes 12 6 Component Assembly Diagrams and Part Lists 12 6 1 Case Assembly NFB 301C...
Page 122: ...122 Appendixes 12 6 2 Case Assembly NFB 399C...
Page 124: ...124 Appendixes 12 6 3 Heat Exchanger and Waterway Assembly NFB 301C...
Page 126: ...126 Appendixes 12 6 4 Heat Exchanger and Waterway Assembly NFB 399C...
Page 128: ...128 Appendixes 12 6 5 Combustion Parts Assembly NFB 301C...
Page 131: ...131 Appendixes 12 6 6 Combustion Parts Assembly NFB 399C...
Page 134: ...Memo...