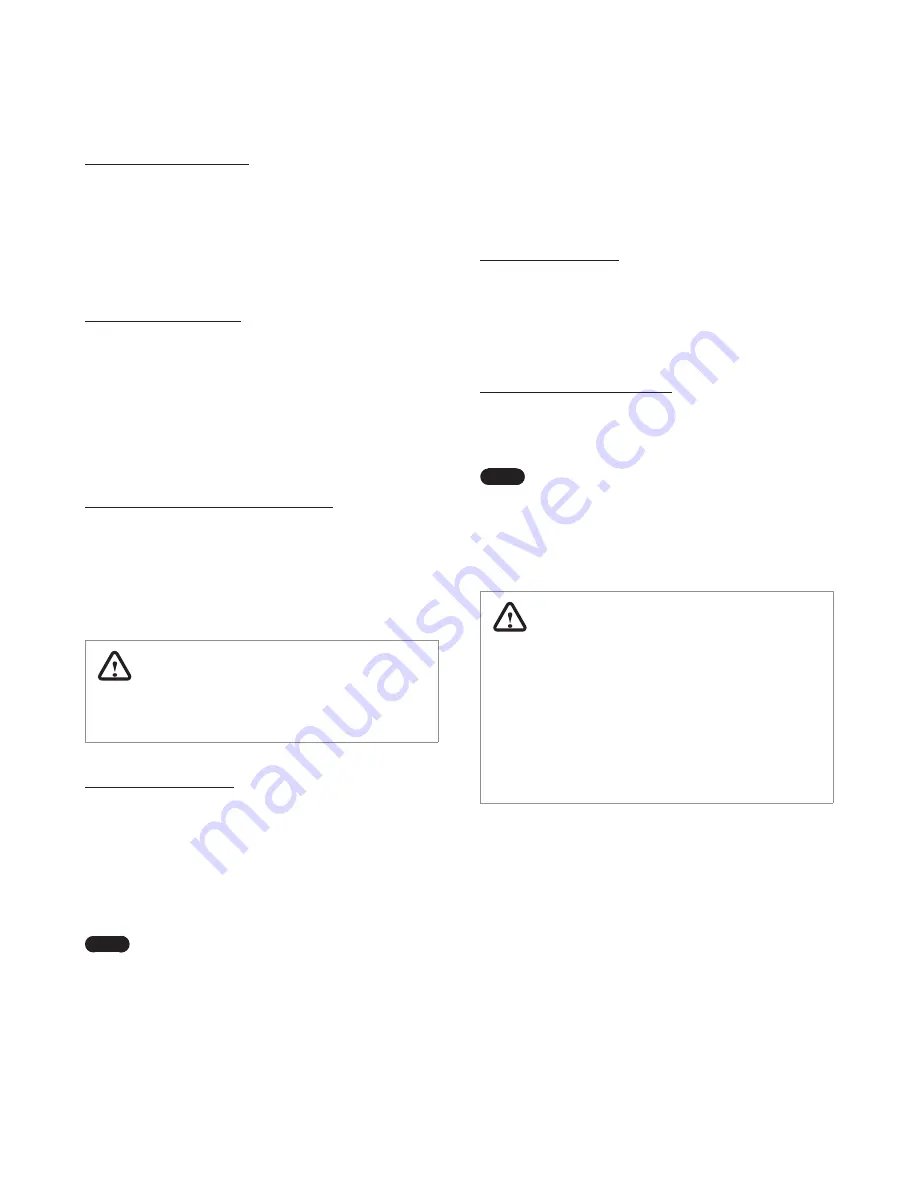
18 Maintaining the Boiler
Cleaning the Condensate Trap
1. Inspect the condensate drain line, condensate fittings, and
condensate trap.
2. Remove any sediment in the trap.
3. Fill with fresh water until the water begins to pour out of the
drain.
Checking all Piping for Leaks
Eliminate all system or boiler leaks. Continual fresh makeup water
will reduce boiler life. Minerals can build up in sections, reducing
heat transfer, overheating heat exchanger, and causing heat
exchanger failure. Leaking water may also cause severe property
damage.
1. Inspect all water and gas piping and verify to be leak free.
2. Look for signs of leaking lines and correct any problems found.
Checking the Flue Vent System and Air Piping
1. Visually inspect the entire flue gas venting system and air
piping for blockage, deterioration or leakage. Repair any
joints that show signs of leakage. Verify that air inlet pipe is
connected and properly sealed (if installed).
2. Verify that boiler vent discharge and air intake are clean and
free of obstructions.
WARNING
Failure to inspect for the above conditions and have them
repaired can result in severe personal injury or death.
Checking the Water System
1. Verify all system components are correctly installed and
operational.
2. Check the cold fill pressure for the system. Verify it is correct
(must be a minimum of 12 psi).
3. Watch the system pressure as the boiler heats up (during
testing) to ensure pressure does not rise too high.
Note
●
If the system contains glycol, test for proper
concentration as recommended by manufacturer.
●
Excessive pressure rise indicates expansion tank
sizing or performance problem.
4. Inspect automatic air vents and air separators. Remove air vent
caps and briefly press push valve to flush vent.
5. Replace caps. Make sure vents do not leak. Replace any leaking
vents.
Checking Expansion Tank
●
Expansion tanks provide space for water to move in and out as
the heating system water expands due to temperature increase
or contracts as the water cools.
●
Perform annual checks as recommended by manufacturer to
ensure proper operation.
Checking the Pressure Relief Valves
1. Inspect the relief valve and lift the lever to verify flow. Before
operating any relief valve, ensure that it is piped with its
discharge in a safe area to avoid severe scald potential.
Note
Safety relief valves should be re-inspected
at least
once every three years
, by a licensed plumbing
contractor or authorized inspection agency, to ensure
that the product has not been affected by corrosive
water conditions and to ensure that the valve and
discharge line have not been altered or tampered
with illegally.
WARNING
Certain naturally occurring conditions may corrode the valve
or its components over time, rendering the valve inoperative.
Such conditions are not detectable unless the valve and its
components are physically removed and inspected. This
inspection must only be conducted by a plumbing contractor
or authorized inspection agency – not by the owner. Failure
to re-inspect the boiler relief valve as directed could result in
unsafe pressure buildup, which can result in severe personal
injury, death, or substantial property damage.
Summary of Contents for NCB-180
Page 26: ...Memo...