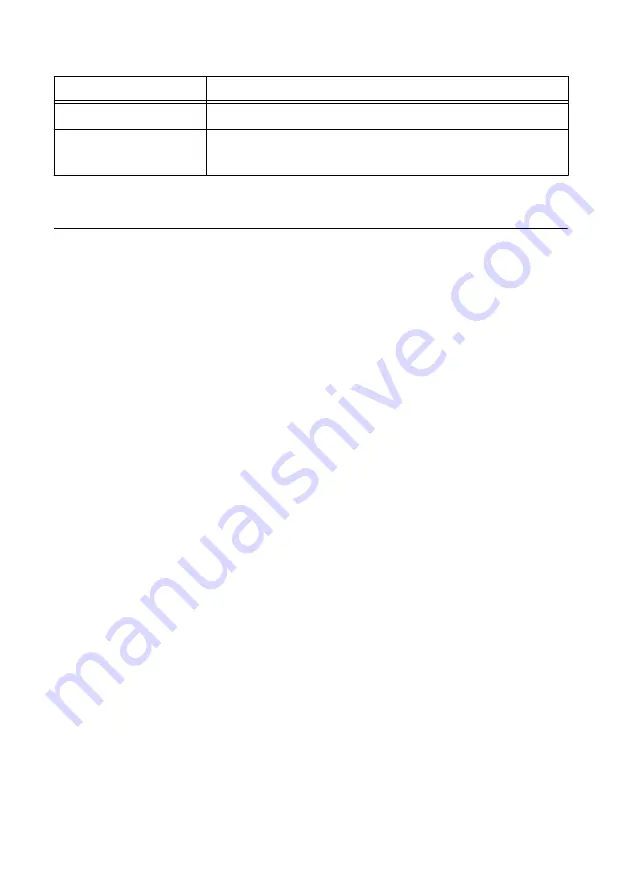
Table 13. Device Default Settings (Continued)
Attribute
Value
Comment
Empty
Default login
User name = admin
Password = no password required
Mounting
FieldDAQ can be mounted on any substrate in any orientation if the ambient temperature is
75 °C or less. However, to ensure proper functionality during use above 75 °C, you must
mount the FieldDAQ device in the reference mounting configuration shown in the following
figure. Observe the following guidelines to mount the FieldDAQ device in the reference
mounting configuration.
FD-11634 User Guide
|
© National Instruments
|
41