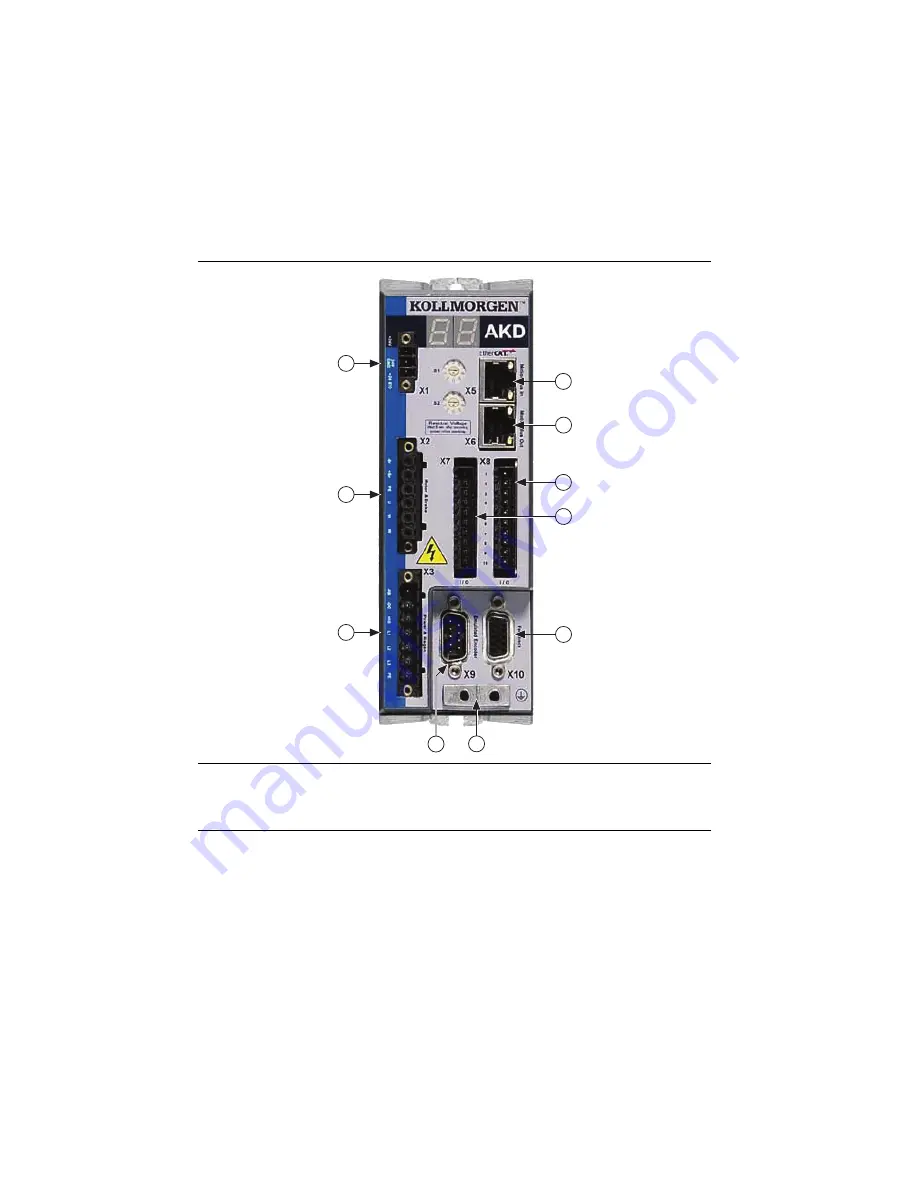
8
|
ni.com
|
Getting Started with AKD EtherCAT Drives and NI SoftMotion
Step 2: Connect the AKD EtherCAT Drive
Figure 6 shows an overview of the connectors on the AKD EtherCAT servo drive.
Figure 6.
AKD EtherCAT Servo Drive Connectors
Mount the Drive and Connect the Protective Earth
1.
Mount the drive to a conductive metal plate. Refer to the
AKD Installation Manual
for
dimensions and additional information specific to the drive model.
2.
Connect the protective earth (PE) to either ground screw on the drive grounding lug.
Figure 6 shows the location of the grounding lug on the drive.
1
24 V Supply, STO (X1)
2
Motor, Brake (X2)
3
AC Input Power (X3)
4
Encoder Emulation (X9)
5
Drive Grounding Lug
6
Feedback (X10)
7
I/O Connector (X7)
8
I/O Connector (X8)
9
Motion Bus OUT (X6)
10 Motion Bus IN (X5)
1
2
3
6
10
8
5
7
9
4