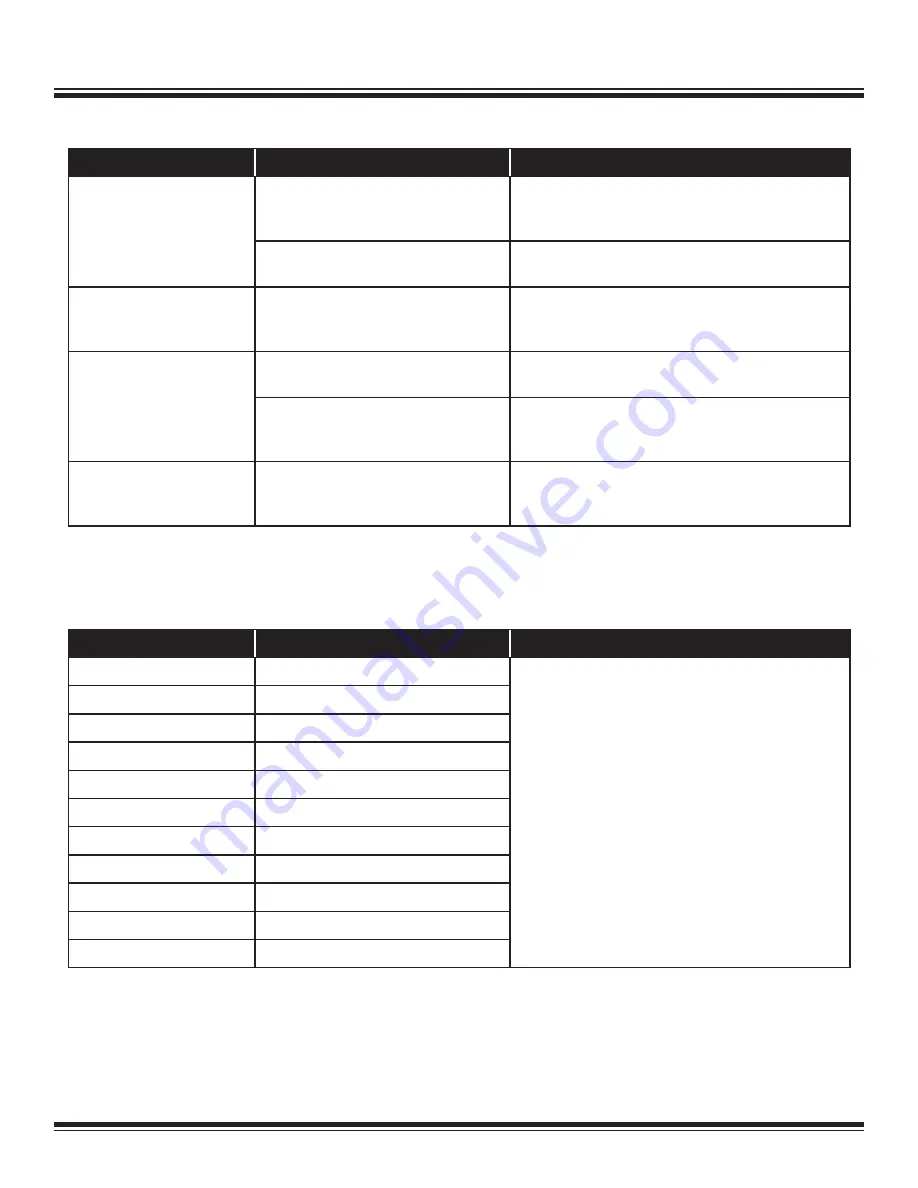
TROUBLESHOOTING
49
407170_ROGUE_RevA
PROBLEM
CAUSE
SOLUTION
Wheels unexpectedly engage
while in freewheel mode.
Debris from wheel turns the coupling flange
and re-engages the wheel.
Remove flange retaining screw, washer and spring. Clean
debris that could be contacting the flange pins causing
them to engage.
Missing or improperly installed wheel
retaining ring
Remove flange retaining screw, washer and spring. Ensure
retaining ring is present and fully seated.
Machine is difficult to tilt back.
Slide weights are positioned forward.
Before tilting machine back, position the slide weights rear-
ward to make tilting easier. Block up machine to prevent
machine from falling forward unexpectedly.
Can’t remove front weight.
Locking screws not sufficiently loosened
Loosen the four locking screws a few turns so screws clear
the locating posts. It is not necessary to remove screws.
Weight is binding with locating posts.
Pulling the weight forward during removal causes weight to
bind with the locating posts. See “MACHINE OPERATION”
section for the proper removal procedure.
Can’t remove middle weights.
Locking screws not sufficiently loosened
Each middle weight is secured with two locking screws.
Loosen the locking screws a few turns so screws clear the
locating posts. It is not necessary to remove screws.
TROUBLESHOOTING GUIDE (CONT’D)
FAULT BLINK CODE
DESCRIPTION
SOLUTION
1
Left VFD CAN communication
Contact NFE technical services to further diagnose.
2
Left VFD error active
3
Right VFD CAN communication
4
Right VFD error active
5
Left control handle signal
6
Right control handle signal
7
Max Speed pot signal
8
Straight Trim pot signal
9
Orbital VFD CAN communication
10
Orbital VFD error active
11
Orbital Speed pot signal
FAULT CODES