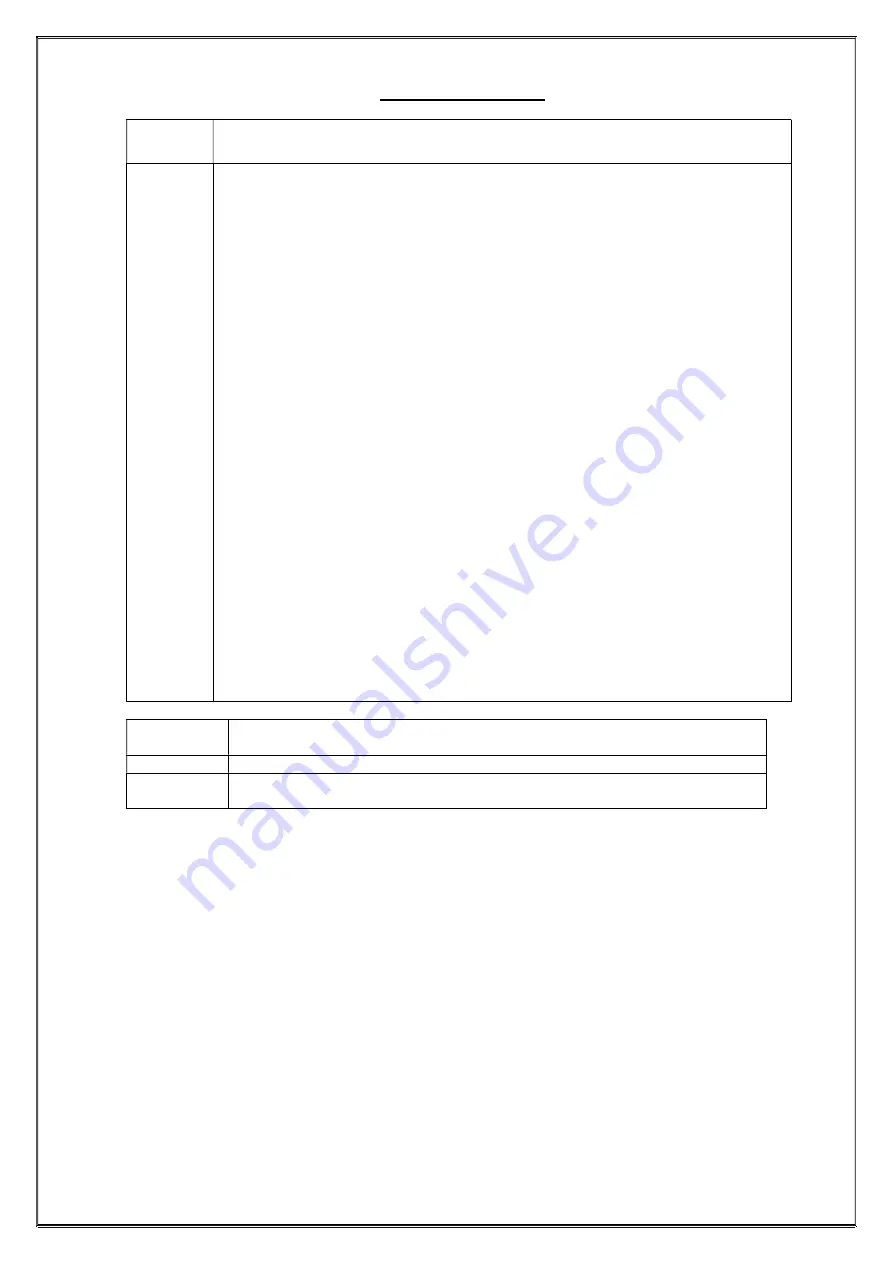
Rev 8, Dated 27-2-2018
53
MISCELLANEOUS
Problem
1.
Treadmill becomes non-functional again and again.
Possible Cause:
6.
No Servo make voltage stabilizer is used for Treadmill even though
the supply voltage is fluctuating.
7.
Voltage Stabilizer is not stabilizing the voltage.
8.
Type of Stabilizer is other than Servo.
9.
There might be leakage of current.
10.
Problems due to slower configuration.
Solution:
6.
Use 3.5 KVA Servo Stabilizers for Treadmill.
7.
Ensure that in spite of changes in supply voltage at mains, the output
voltage is stable. For this, change the analog meter switch of
stabilizer to INPUT mode, Connect digital voltmeter (D.M.M.) to
output of the stabilizer. Now you are observing input voltage to
stabilizer and output voltage of the stabilizer. Here the out put voltage
displayed on D.M.M. should not vary by more than 2-3 volts even
though the input voltage changes by more than 10-20 volts.
8.
If this output voltage to Treadmill is also varying with changes in
supply voltage, the stabilizer needs to be repaired immediately.
9.
There are different types of voltage stabilizers used for voltage
stabilization. One is the On-OFF type of stabilizer. Here depending
upon the input voltage range, the relay inside the stabilizer operates
to stabilize the output voltage. But this relay operation generates a
spike at the output. This spike creates a problem to DC motor speed
control circuit and hence the Treadmill stops working. Another type of
stabilizer is SERVO STABILIZER. This stabilizer has built-in servo-
motor, which rotates continuously with change in supply voltage. The
shaft of this motor selects the appropriate winding of the VARIAC so
as to stabilize the output voltage at 230 volts. Hence there are no
spikes in the output voltage of the stabilizer.
10.
This SERVO type is recommended for Treadmill.
Problem
2.
Spike in ECG
Solution
Use branded SMPS for PC
Material
Req.
Intex make SMPS