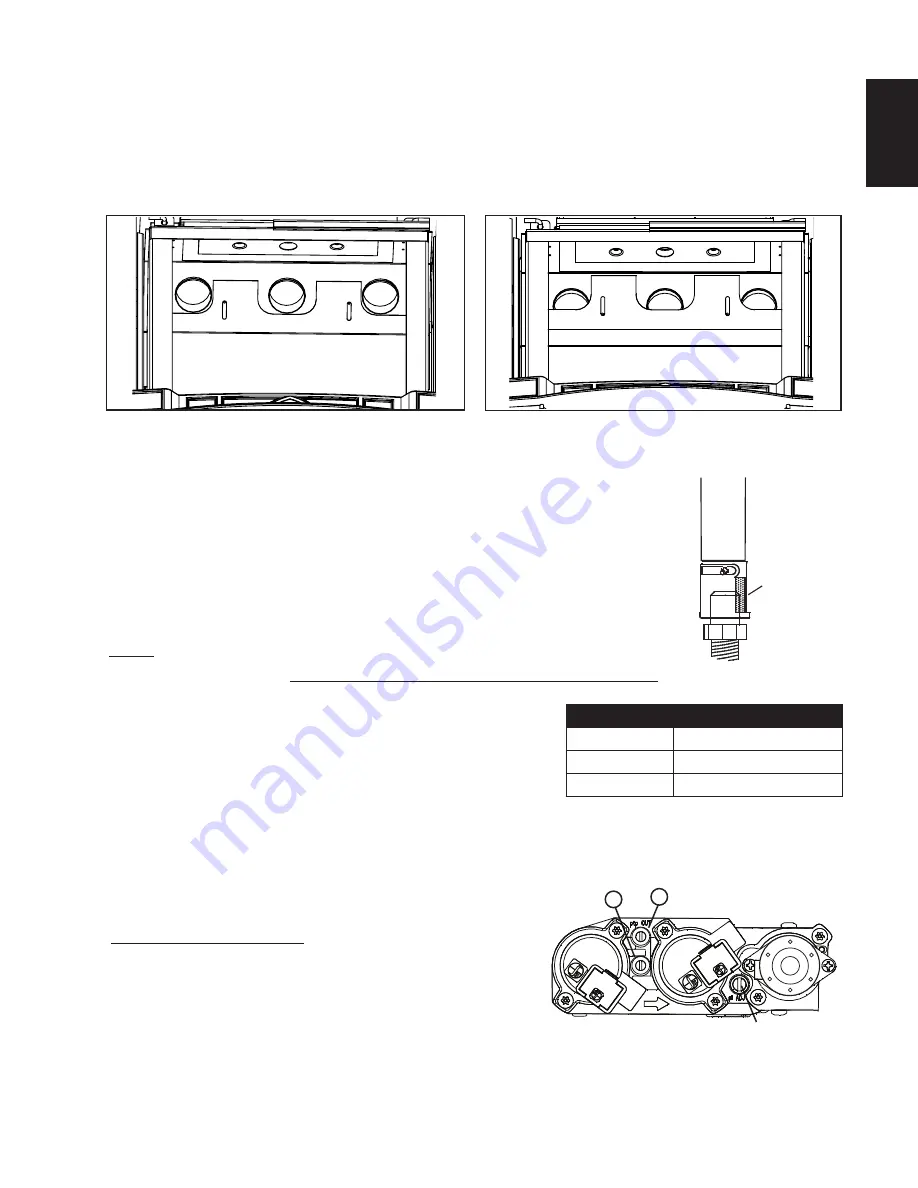
Remove the 2 screws securing the burner. Air shutters have been
factory set open according to the Venturi Adjustment Chart. These
settings are for (maximum) horizontal termination. Adjustment may be
required depending on fuel type, vent configuration and altitude. After
making adjustments replace the burner ensuring that the venturi tube
fits over the orifice and replace the screws.
VENTURI ADJUSTMENT CHART
FUEL
GDS25-1
NG
5/16” (8mm)
P
7/16” (11mm)
9.0 ADJUSTMENT
This appliance has an air shutter that has been factory set open according
to the chart below:
Regardless of venturi orientation, closing the air shutter will cause a more
yellow flame, but can lead to carbonization. Opening the air shutter will
cause a more blue flame, but can cause flame lifting from the burner ports.
The flame may not appear yellow immediately; allow 15 to 30 minutes for
the final flame colour to be established.
AIR SHUTTER ADJUSTMENT MUST ONLY BE DONE BY A QUALIFIED
INSTALLER!
NOTE: It is important that the orifice is securely inserted into the venturi.
AIR
SHUTTER
OPENING
VENTURI
BURNER
ORIFICE
33.1
RESTRICTOR SHOWN IN A
FULLY OPEN POSITION
RESTRICTOR SHOWN IN A
FULLY CLOSED POSITION
Vertical installations may display a very active flame. Loosen the two screws and slide the restrictor plate block-
ing the exhaust path. This reduces the velocity of the exhaust gases, slowing down the flame pattern and creat-
ing a more traditional flame appearance. For vertical vents greater than 15 ft (5m), this restrictor must be fully
closed.
9.1 RESTRICTING VERTICAL VENTS
9.2 VENTURI ADJUSTMENT
9.3 PILOT BURNER ADJUSTMENT
Adjust the pilot screw to provide properly sized fl ame. Turn in a
clockwise direction to reduce the gas fl ow.
Check Pressure Readings:
Inlet pressure can be checked by turning screw (A) counter-
clockwise 2 or 3 turns and then placing pressure gauge tubing
over the test point. Gauge should read as described on the chart
below. Check pressure with main burner operating on “HI”.
Outlet pressure can be checked the same as above using
screw (B). Gauge should read as described on the chart
below. Check pressure with main burner operating on “HI”.
AFTER TAKING PRESSURE READINGS, BE SURE TO
TURN SCREWS CLOCKWISE FIRMLY TO RESEAL. DO
NOT OVERTORQUE.
Leak test with a soap and water solution.
Prior to pilot adjustment, ensure that the pilot assembly
has not been painted. If overspray or painting of the pilot
assembly has occurred remove the paint from the pilot
assembly, or replace. Fine emery
cloth or a synthetic scrub pad (such as
Scotch-Brite
™)
can be used to remove
the paint from the pilot hood, electrode
and fl ame sensor.
*Maximum inlet pressure not to exceed 13”.
39.1E
A
B
PILOT SCREW
3/8” - 1/2”
(9,5mm - 12,7mm)
FLAME MUST ENVELOP
UPPER 3/8” (9.5mm) TO 1/2”
(12.7mm) OF FLAME SENSOR
PILOT
BURNER
ELECTRODE
FLAME
SENSOR
LA FLAMME DOIT
ENVELOPPER LA PARTIE
SUPÉRIEURE DE LA SONDE
DE FLAMME DE 3/8” (9,5mm)
À 1/2” (12,7mm)
ÉLECTRODE
LA SONDE
DE FLAMME
VEILLEUSE
3/8” - 1/2”
(9.5mm - 12.7mm)
Pressure
Inlet
Outlet
Natural Gas
(inches)
Natural Gas
(millibars)
Propane
(inches)
Propane
(millibars)
*13"
(MIN. 4.5”)
3.5"
13"
(MIN. 11")
10"
17.4mb
(MIN. 11.2mb)
8.7mb
32.4mb
(MIN. 27.4mb)
24.9mb
W415-2207 / A / 08.28.17
37
EN