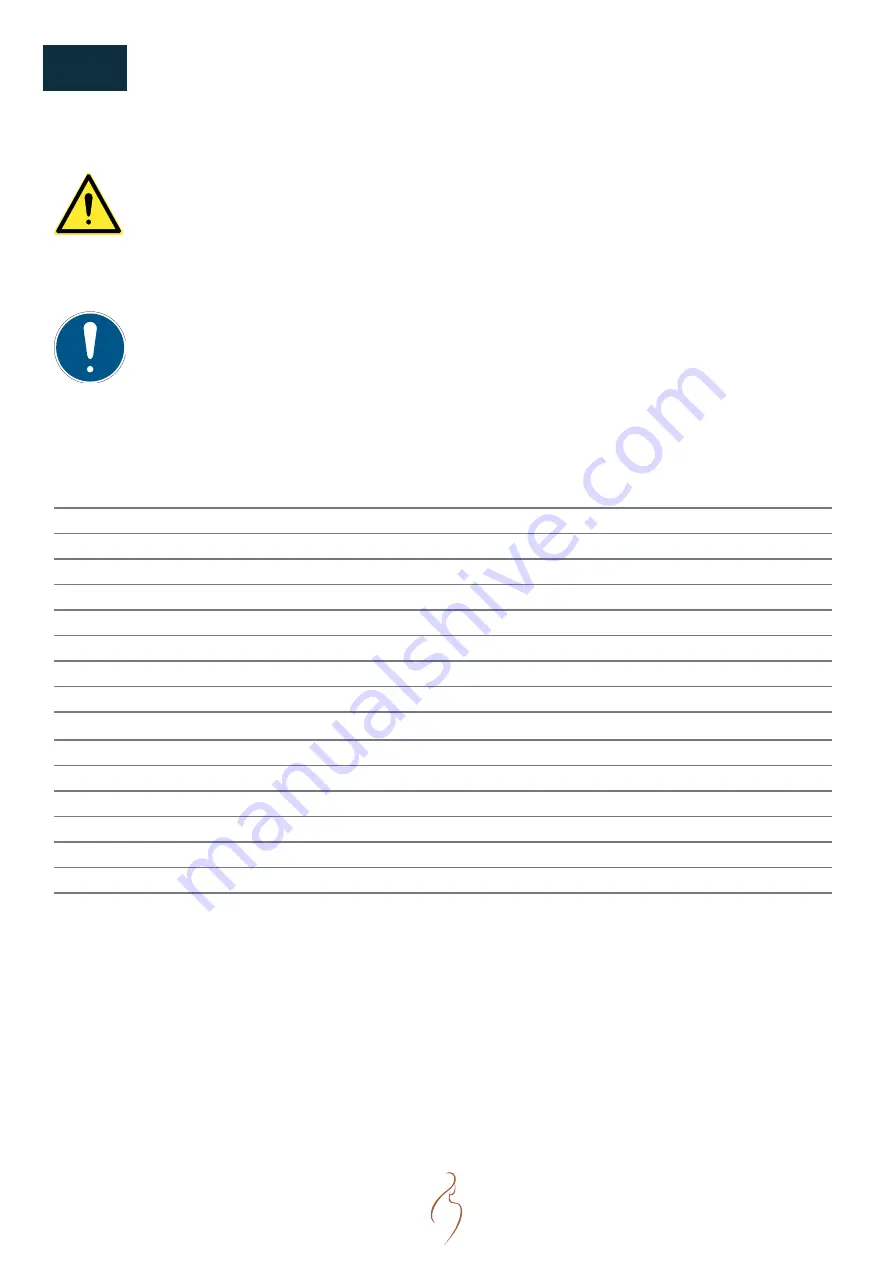
98
S10
TROUBLESHOOTING
CAUTION !
If the engine does not function properly, use the following chart to identify the cause. If the cause of trouble can not be
found, contact to Nanni authorized workshop.
NOTE !
Some components may not be part of the engine orderes. This list is not exhaustive and is only ab assistance in case
of emergencies.
PROBABLE CAUSES
The engine fails to start
1, 2, 3, 4, 5, 6, 7, 8, 9, 10, 11, 13
The engine starts but suddenly stops
1, 2, 3, 4, 5
The engine is difficult to start
1, 2, 3, 4, 5, 6, 8, 9
The starter motor is not turning or turn slowly
8, 9
The starter motor turns but the engine does not start
1, 2, 3, 4, 5, 6, 7
The engine does not reach its rated speed at wide open throttle 2, 3, 4, 5, 6, 7, 12, 14, 15, 16, 17, 26, 28
The engine operate unevenly
1, 2, 3, 4, 5, 6, 7, 14, 15, 16, 17, 18, 19, 20, 24, 28
The engine vibrates a lot
16, 27
Black exhaust smoke
4, 5, 14, 15, 16, 19, 20, 28, 29
White exhaust smoke
4, 5, 23, 25
High fuel consumption
4, 7, 14, 15, 16, 19, 20, 22, 28
The engine overheats / coolant temperature too high
14, 15, 16, 18, 19, 20, 21, 22, 28
The control lever is hard to operate
12, 14, 15, 16, 17, 26
No shift between ahead and astern
9, 11, 12, 16, 17, 26
Battery charge warning lamp comes on
8, 9, 11, 18
The numbers refer to the possible causes indicated on the following page.*
Contact a Nanni authorized workshop.
Summary of Contents for N13.700 CR3 HD
Page 2: ......
Page 4: ......
Page 40: ...40 S05 INSTRUMENTATION SYSTEM LAYOUT INCLUDING OPTIONS...
Page 44: ...44 NOTES...
Page 120: ......