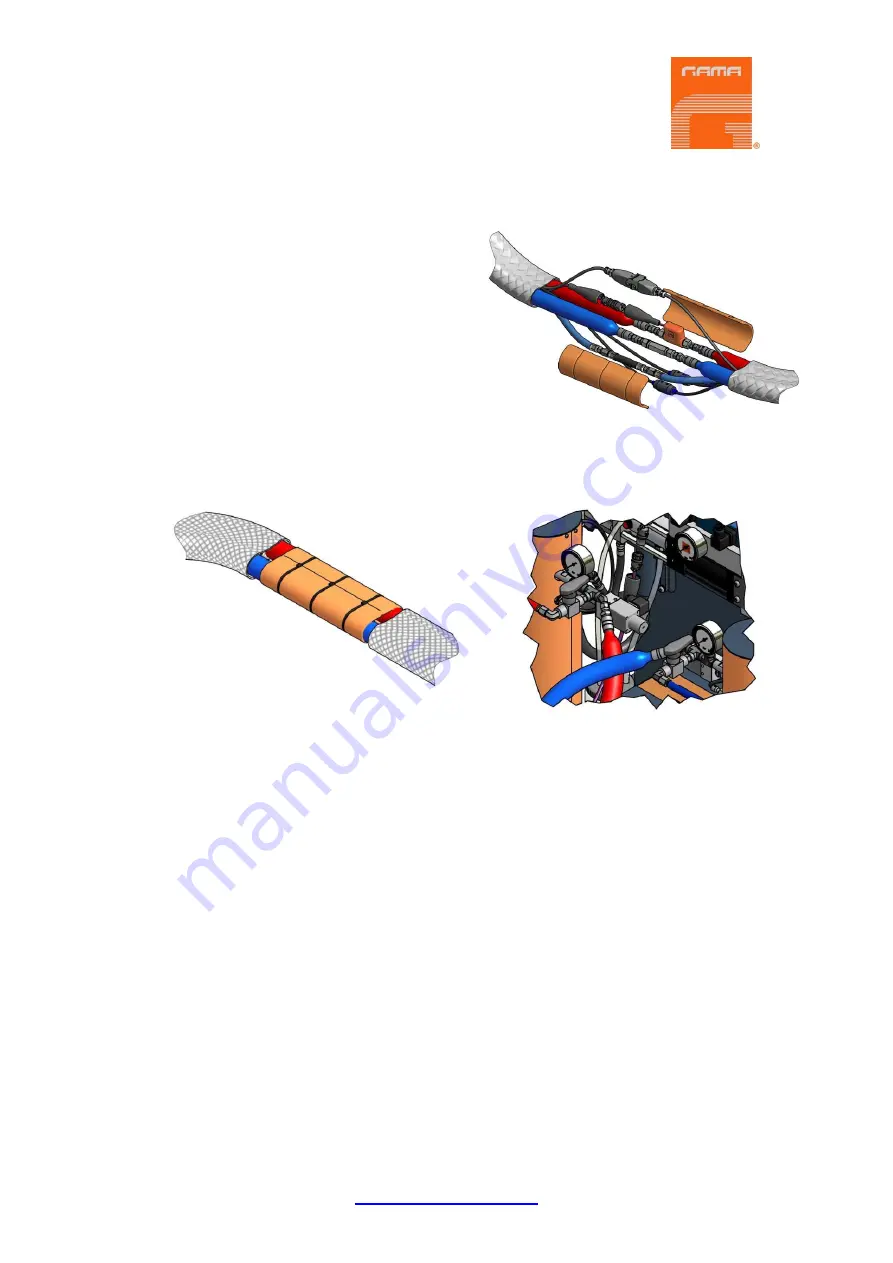
evolution G-30 H
Service Manual
21/44
Issue 3.1
Ref. NR-00040-ENG
http://www.gamapur.com/
h) Install the probe of control of temperature
TCS between the last stretch of hose of
product and the final stretch connected to
the gun. Stretch carefully the cable of the
probe inserting it in the Isocyanate hose.
i)
Wind the connector of the probes to the
connector of the hose. Realize so many
connections as stretches of 15 m hose you
have.
j)
Realize the connections between the
connector of exit of the probe TCS of the
first stretch of hose and the connector
proceeding from the machine
k) As soon as the connections were completed, place the protections for the union fixing
them with three plastic bridles. Later cover the union with the ends of the cases.
NB:
To protect the TCS sensor, you must pay special attention not to kink or
excessively bend the hoses. Do not roll up the hoses with a radius of under one meter / 4
feet.
l)
Connect the air hoses.
m) Connect the hoses to the connectors of the coupling block of the gun, making sure that
the manual valves are closed.
Having performed the above operations, you must note the direction in which the motor turns.
To make sure that it is turning clockwise, do the following:
a) Turn the hydraulic pressure regulator counter clockwise.
b) Turn the general switch ON. The top pilot light will come on.
c) Press the POWER CONTROL key.
d) Go to the side of the machine to be able to see the motor fan. Press the MOTOR key to
start the motor and press it again to stop it. Check that the blades of the fan are turning
clockwise, otherwise turn the general switch OFF and disconnect the machine from the
source of electrical supply.
e) Open the console of the control panel and change the position of two of the three wires
of the electrical connection of the unit. Check the turning direction once more.