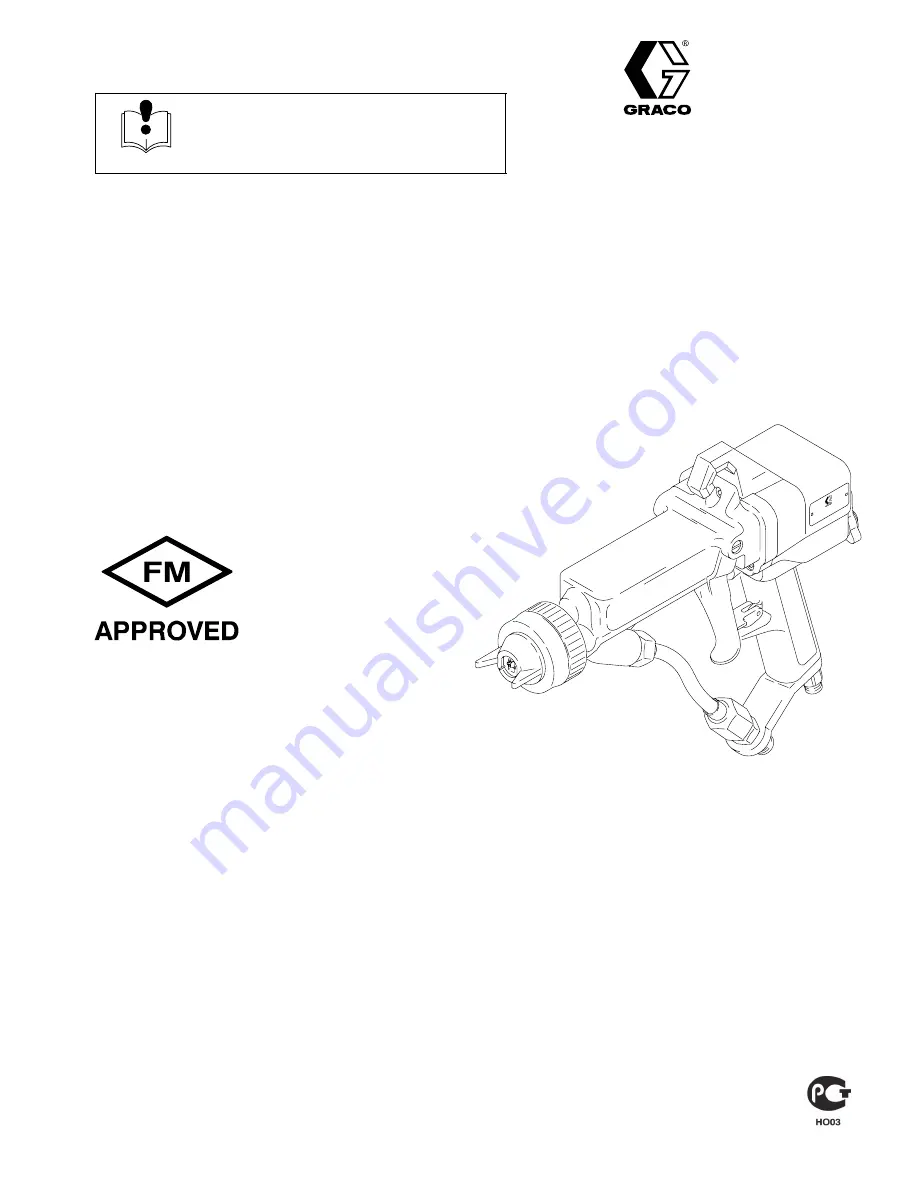
308936
Rev. B
Supersedes Rev. A
First choice when
quality counts.
01944A
NOTE:
Any modification of genuine Graco parts or replacement of parts with non-Graco parts will void agency approvals.
U.S. Patent No. 4,290,091; 4,219,865; 4,497,447; 4,462,061; 4,660,774; 5,063,350; 5,080,289; 5,289,977
Patented 1986, 1987 Canada
Brevete 1986, 1987
U.K. Patent No. 2,147,158; 2,142,559B; 2,140,327–B
Other U.S. and Foreign Patents Pending
UNICARB IS A REGISTERED TRADEMARK OF UNION CARBIDE, DANBURY CT.
INSTRUCTIONS-PARTS LIST
INSTRUCTIONS
This manual contains important
warnings and information.
READ AND KEEP FOR REFERENCE.
85 KV ELECTROSTATIC
Model PRO AA4500
/UNICARB
Air-Assisted Spray Gun
100 psi (7 bar, 0.7 MPa) Maximum Working Air Pressure
3000 psi (207 bar, 20.7 MPa) Maximum Working Fluid Pressure
For use with Class
I
, Group D paint spray materials
Part No. 965722, Series B
Spray Gun with basic power supply,
2-finger trigger
GRACO INC.
P.O. BOX 1441
MINNEAPOLIS, MN
55440–1441
COPYRIGHT 1999, GRACO INC.
Graco Inc. is registered to I.S. EN ISO 9001
Summary of Contents for UNICARB
Page 40: ...40 308936 Notes ...