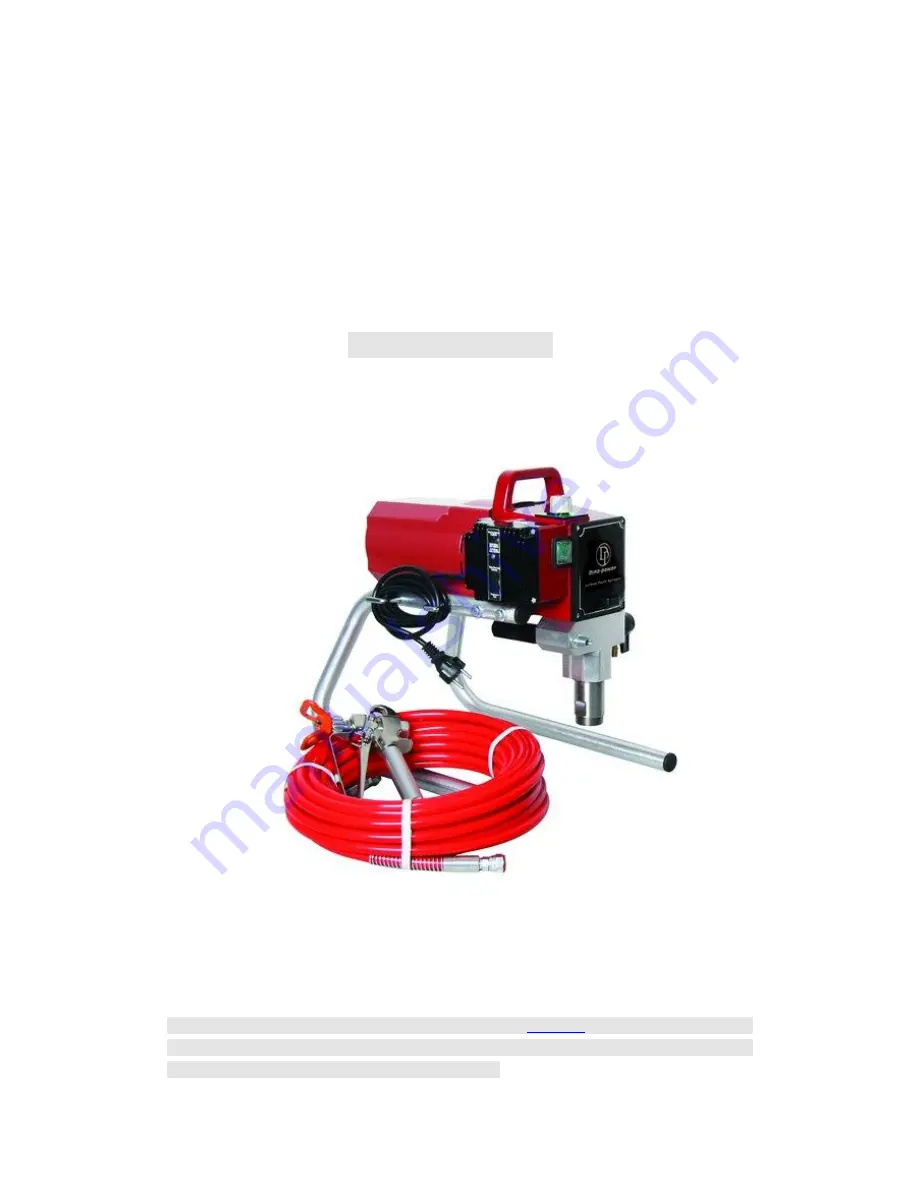
Operation manual for
Airless paint
sprayer
High Pressure Electric
Airless paint sprayer Titan 440i
model
intelligent series
Remark
: this guide manual is the same with model
DP-6389
,the content include :the
operation of equipment,cleaning ,maintenance ,and repair,be sure to pre-operational ,read
the manual carefully before you use this machine.