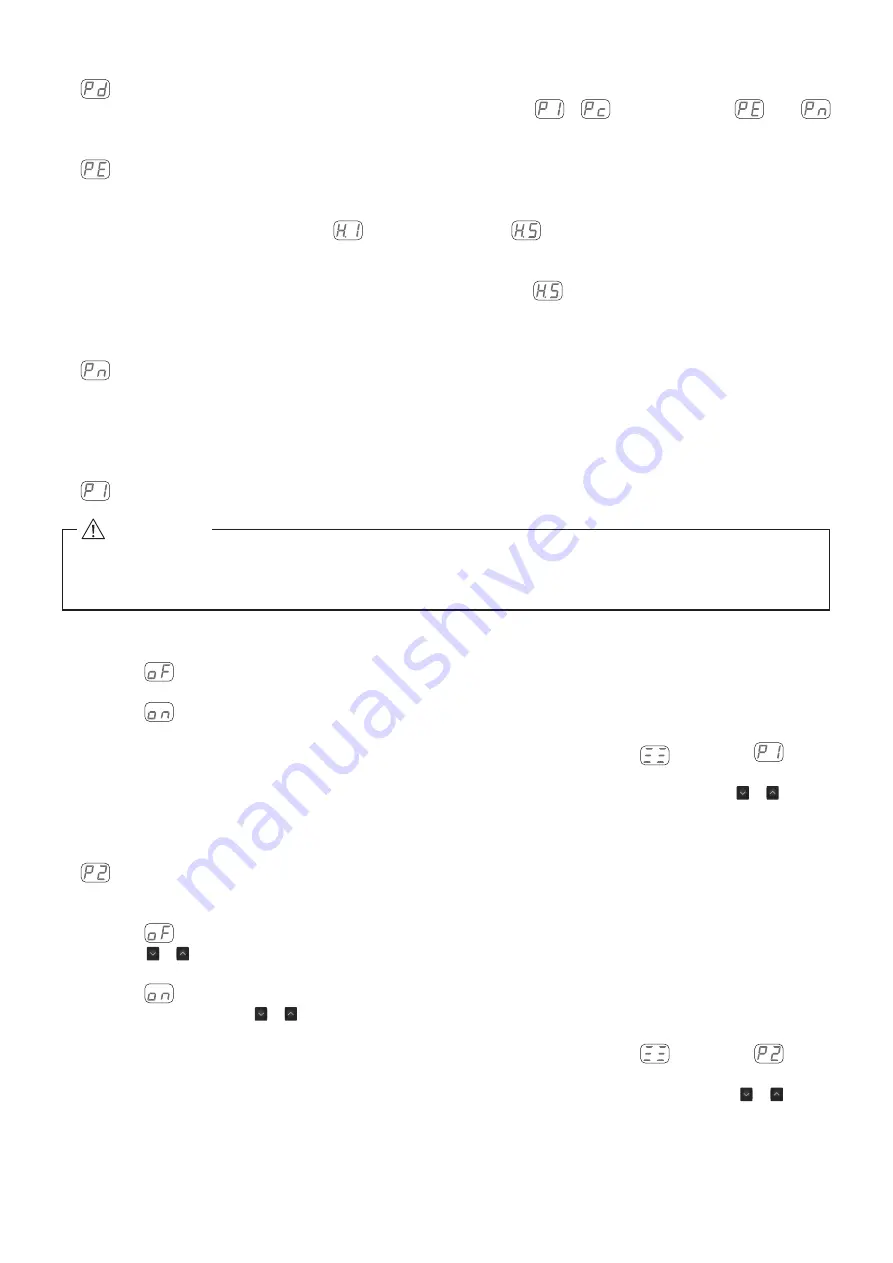
104
⑬
Confirmation of Parameter Setting
・
This mode allows the user to check the settings of parameters
-
. The parameter
and
cannot be checked.
⑭
Error History
・
The Error History, which records previous error codes can be confirmed by the Error Code displayed on the
Digital Speed Indicator
⑬
.
・
The last Error Code recorded will be
and the oldest will be
The Error code is displayed on the Digital
Speed Indicator
⑬
.
・
The Error History cannot be erased or deleted.
・
If Error History contains more than five errors, oldest Error History,
will be deleted.
・
To clear Error History, push and hold the START / STOP Button (START / STOP)
⑯
for three seconds. A beep
emits and the Error History will be cleared.
⑮
Confirmation of Software Version
・
The version of the program installed on the CONTROLLER can be checked.
・
The program version is displayed on the Digital Speed Indicator
⑬
.
18 - 4 Setting procedures
①
Setting of Error Output Mode
Procedure
1. Push the START / STOP Button (START / STOP)
⑯
.
2.
is displayed. This indicates that when an error occurs, the output will be ' OFF (Open) '.
3. Push the START / STOP Button (START / STOP)
⑯
.
4.
is displayed. This indicates that when an error occurs, the output will be ' ON (Closed) '.
5. You can cycle through the choices by pushing the START / STOP Button (START / STOP)
⑯
.
6. Push the Error Reset Button (RESET)
㉑
to send the settings to memory.
followed by
will be
displayed.
7. If you desire to set other parameters, push the Motor Speed Adjustment Button (SPEED
,
)
⑮
to
select the parameter that needs to be set.
8. When you are finished setting parameters, turn the Main Power Switch
⑨
to OFF.
②
Setting AUTO Mode for Motor Speed Control
Procedure
1. Push the START / STOP Button (START / STOP)
⑯
.
2.
is displayed. This indicates that speed control by the Motor Speed Adjustment Button (SPEED
,
)
⑮
is disabled (The External Command Signal Control will be operational).
3. Push the START / STOP Button (START / STOP)
⑯
.
4.
is displayed. This indicates that speed control is changeable by the Motor Speed Adjustment
Button (SPEED
,
)
⑮
.
5. You can cycle through the choices by pushing the START / STOP Button (START / STOP)
⑯
.
6. Push the Error Reset Button (RESET)
㉑
to send the settings to memory.
followed by
will be
displayed.
7. If you desire to set other parameters, push the Motor Speed Adjustment Button (SPEED
,
)
⑮
to
select the parameter that needs to be set.
8. When you are finished setting parameters, turn the Main Power Switch
⑨
to OFF.
CAUTION
If the Error Output Mode has been changed from the default setting, that setting will be displayed the
next time you enter Parameter Setting Mode.