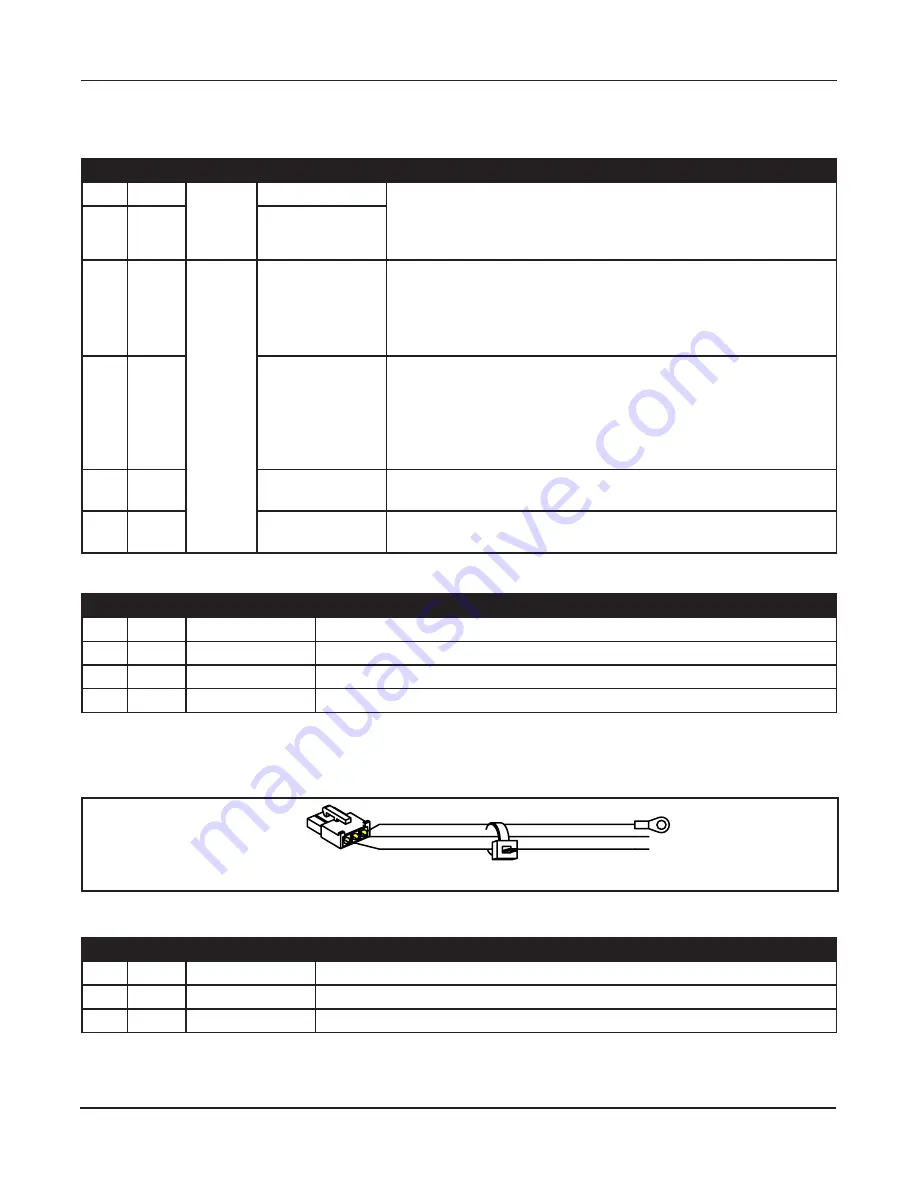
Magnum 4A Control Wiring and Adjustment Manual
Part #C-00084
Rev. 9-09-16
3-8
Magnum 4A Board Terminals
Table #-1
Terminal Block Connections
Pole Wire Harness
Circuit
Description
1
Brown
Aux Pwr
24 VAC Neutral
X
Circuit is used for any Sensor that operates on 24 VAC.
X
Sensor must not exceed 0.5 amp current draw.
X
If Sensor exceeds 0.5 amp current draw Fuse (F1) will trip. A
separate power supply must be used.
2
Orange
24 VAC Hot
3
Violet
Terminal
Continuous Safety
X
Circuit is used with door mounted Sensors on Pull side of door:
X
When Pin (3) is shorted to Pin (5) Sensor will:
• Stop door during opening
• Prevent door from moving when door is fully closed
X
Circuit is always active.
4
White
Safety w/Lockout
X
Circuit is used with Header mounted Presence Sensors or Mats
on pull side of door.
X
When Pin (4) is shorted to Pin (5) Sensor or Mat will:
• Prevent door from opening if already closed
•
Hold door open if already open
X
Circuit is only active while door is fully closed or fully open.
5
Red
Signal Common
This Terminal is the Common to activation, safety, back check and
latch check switches.
6
Black
Activation
Circuit is used for activation of door. When Pin 6 is shorted to Pin 5
door is activated.
Table #-2
Switch Harness
Pin
Wire
Circuit
Description
1
Orange
Door Closed
Door closed or Latch check signal
2
N/A
N/A
N/A
3
Red
Common
Common for Check Signals
4
Blue
Back Check
Door open or back check signal.
Section 3b.
Power Harness
The 120 VAC Power Connector Harness is connected to J4. Please se e Figure 3-3
.
Figure 3-3
Power Harness
DN 0606
1
Table #-3
Power Connector Harness
Pin
Wire
Circuit
Description
1
Green
120 VAC
Incoming Ground wire
2
White
120 VAC
Incoming Neutral wire
3
Black
120 VAC
Incoming Hot wire