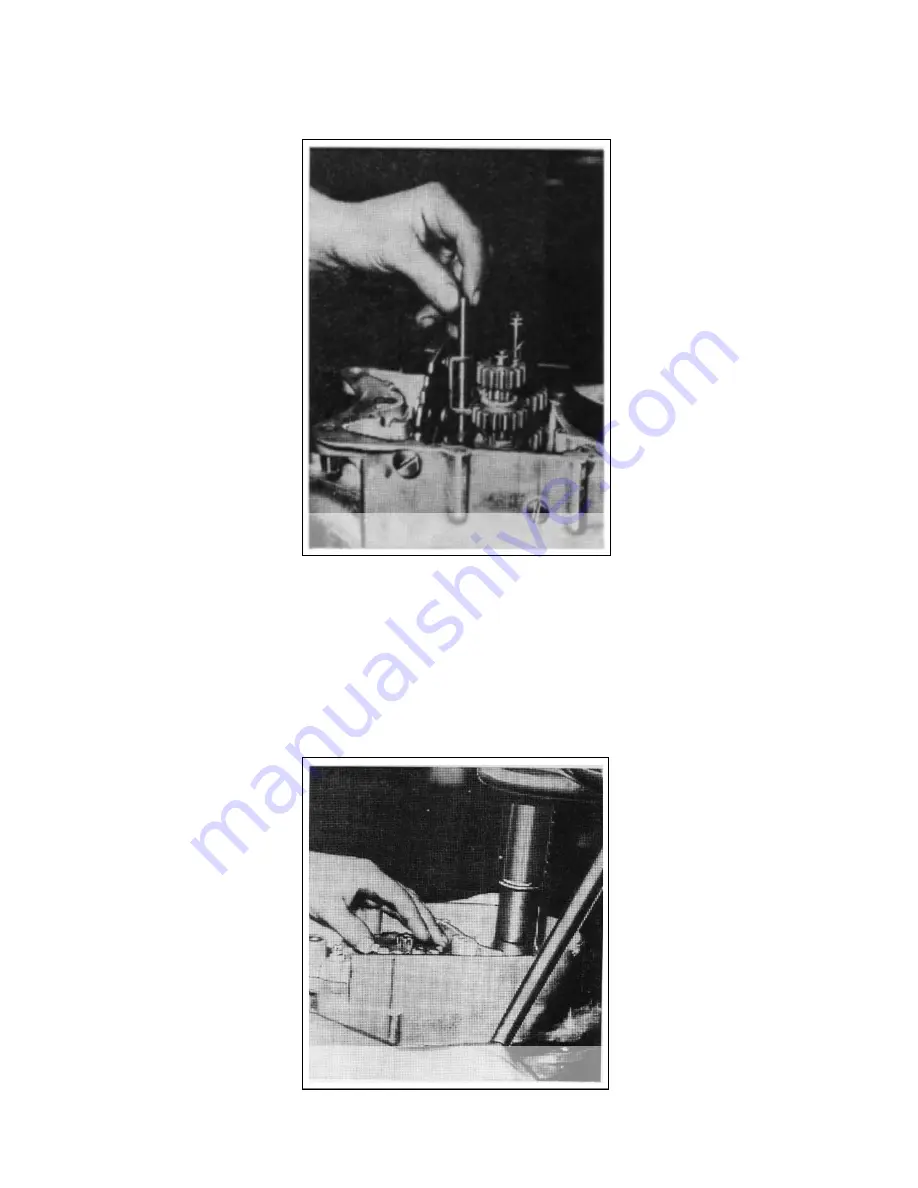
- 34 -
10. Fit the lay shaft with the lay shaft third and top gear pinions
11. Insert the rod into the selector forks and tighten the securing screw. Fig.23.
12. Press the driving gear with hub into the R.H. crankcase half.
13. Turn the crankcase over and press in the sealing ring with the spacer.
14. Knock the gear box sprocket on, fit the securing washer and tighten the nut.
15. Provide both crankcase halves with a coat of sealing compound knock in the
dowel bushes using drift S-2 and tighten fast. For tightening make use of the
gearbox sprocket turning it round. Fig.24.
Fig 23
Fig 24
Summary of Contents for 501/01
Page 1: ...orkshop anual This manual covers all Cezeta and N Zeta models M W ...
Page 12: ... 11 Fig 2 ...
Page 20: ... 19 Fig 7 ...