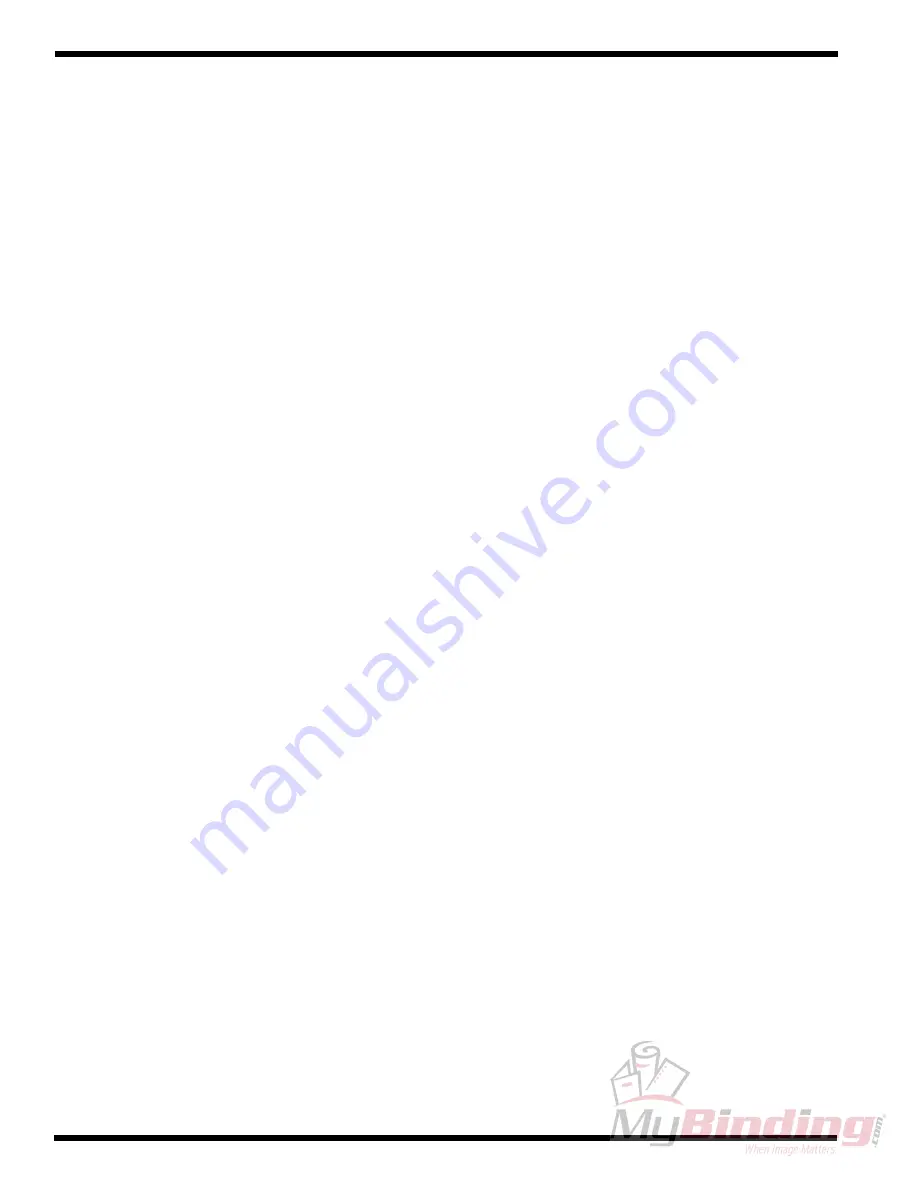
© GBC Films Group April 2000
Voyager Operation and Maintenance Manual
Page 1 - 40
Application
5.7 Over view
An over view is provided to explain how
certain adjustments are determined and to give you,
the operator, a more insightful view of an adjustment.
Nip pressure
Many factors affect the choice of the nip
pressure. Factors you should consider may include:
kinds of material in film and paper stock, thickness of
adhesive, paper grain length and grain direction, as
well as thickness and size of sheet. Laminating thick
sheets may call for high pressure to minimize “tenting”
at the end of the sheet. Paper will not tolerate as much
nip pressure after it has been exposed to high humidity.
If you are using material like foam board or
corrugated board, that must be protected from crushing,
you can apply just enough air pressure to overcome
the resistance of the springs and bring the chrome roller
into contact with the sheets.
Film tension
Several factors may affect the choice of film tension.
These factors include the speed of operation, size of
the film roll, and use of the slitter.
There are various ways of adjusting the film tension.
1. First adjust the bow to smooth the film out across the
bow roller as much as possible, prior to applying the
brake tension.
2. Apply film tension by turning the air pressure adjusting
knob on the control panel. Wrinkles in the film will give a
“waterfall” -like appearance to the film near the point
where it meets the chrome roller.
3. By slowly turning the adjusting knob, adjust tension so
the “waterfall” extends no more than halfway around the
chrome roller.
Breaker bar
Because the action of the brake at the Film Supply
Shaft stretches the film before it is applied, the tension in
the film tends to bow the laminated product upward. To
counteract the bowing tendency, the laminator “breaks”
the paper. That is, while the laminated sheets are still hot,
they are pulled over the edge of a breaker bar to stretch
the film more and impart a downward curl to the
product. Thick sheets may not require breaking.
Pull rollers
The Pull Rollers, located after the knicking section of
the laminator, run slightly faster than the laminating
rollers, to keep the web tight as it goes over the breaker
bar. During any laminating operation, the pull rollers
are applied by rotating the lever attached to the lower
pull roller.