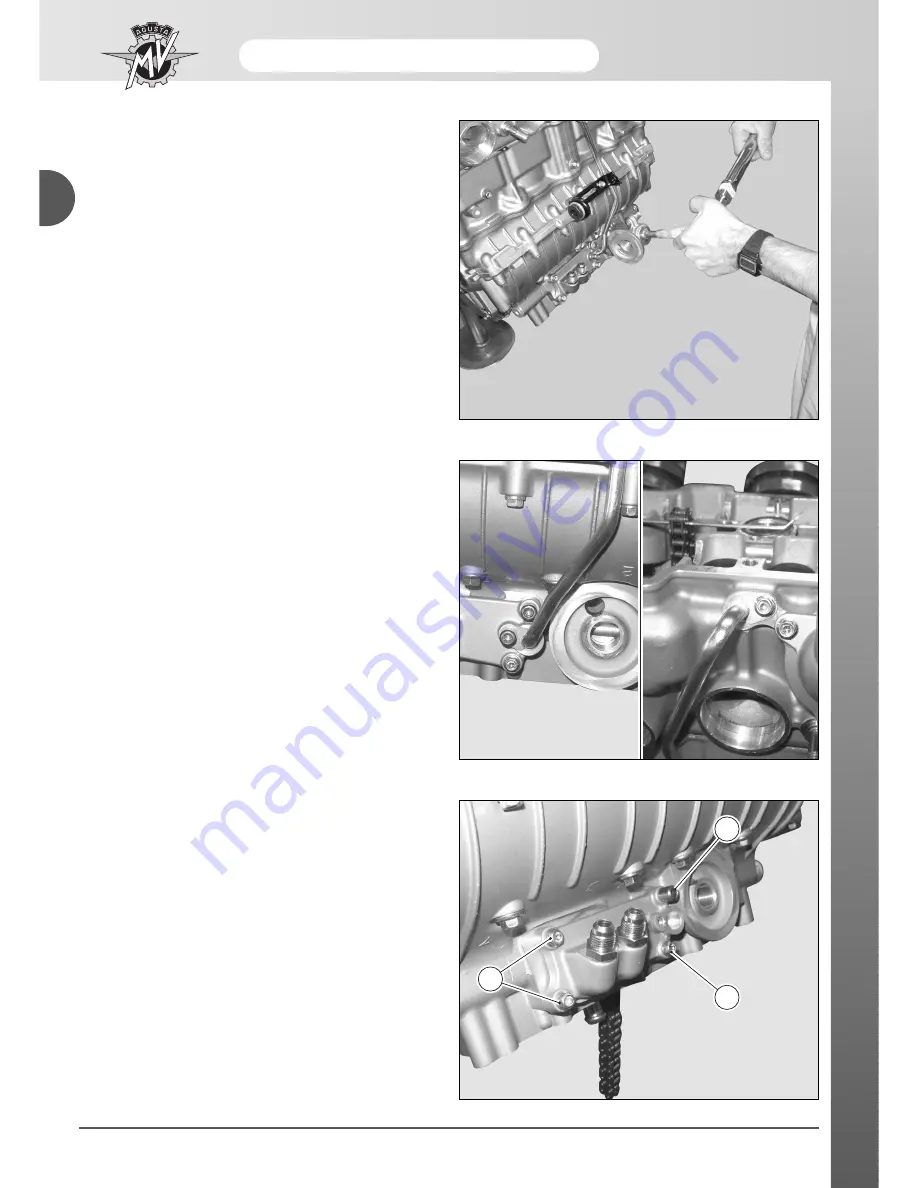
- 86 -
Engine
B
1
2
2
Then, remove the oil head delivery conduit by remo-
ving the lower and upper fixing screws respectively.
Unscrew the three screws (
2
) and remove them; then
remove the special screw (
1
) placed on top left.
LUBRICATION COMPONENTS:
OIL TUBING SUPPORT PLATE
Disassembling and reassembling
To remove the oil tubing support plate, the oil filter sup-
port should be removed first, as described in the “Oil
sump” paragraph.
Summary of Contents for BRUTALE 910 S
Page 1: ...Workshop engine manual MVAGUSTA BRUTALE 910 S MVAGUSTA BRUTALE 910 S...
Page 3: ...Workshop engine manual MVAGUSTA BRUTALE F4 910 S...
Page 5: ...Freni 3 A B General Index GENERAL DESCRIPTION ENGINE...
Page 6: ......
Page 7: ...1 General description A SECTION A Revision 0...
Page 17: ...B 1 Engine SECTION B Revision 0...
Page 48: ...32 Engine B Pin number 24 Pin number 25 Pin number 1...
Page 52: ...36 Engine B 800094798...
Page 112: ...8A00A6440 Part No Edition No 1...