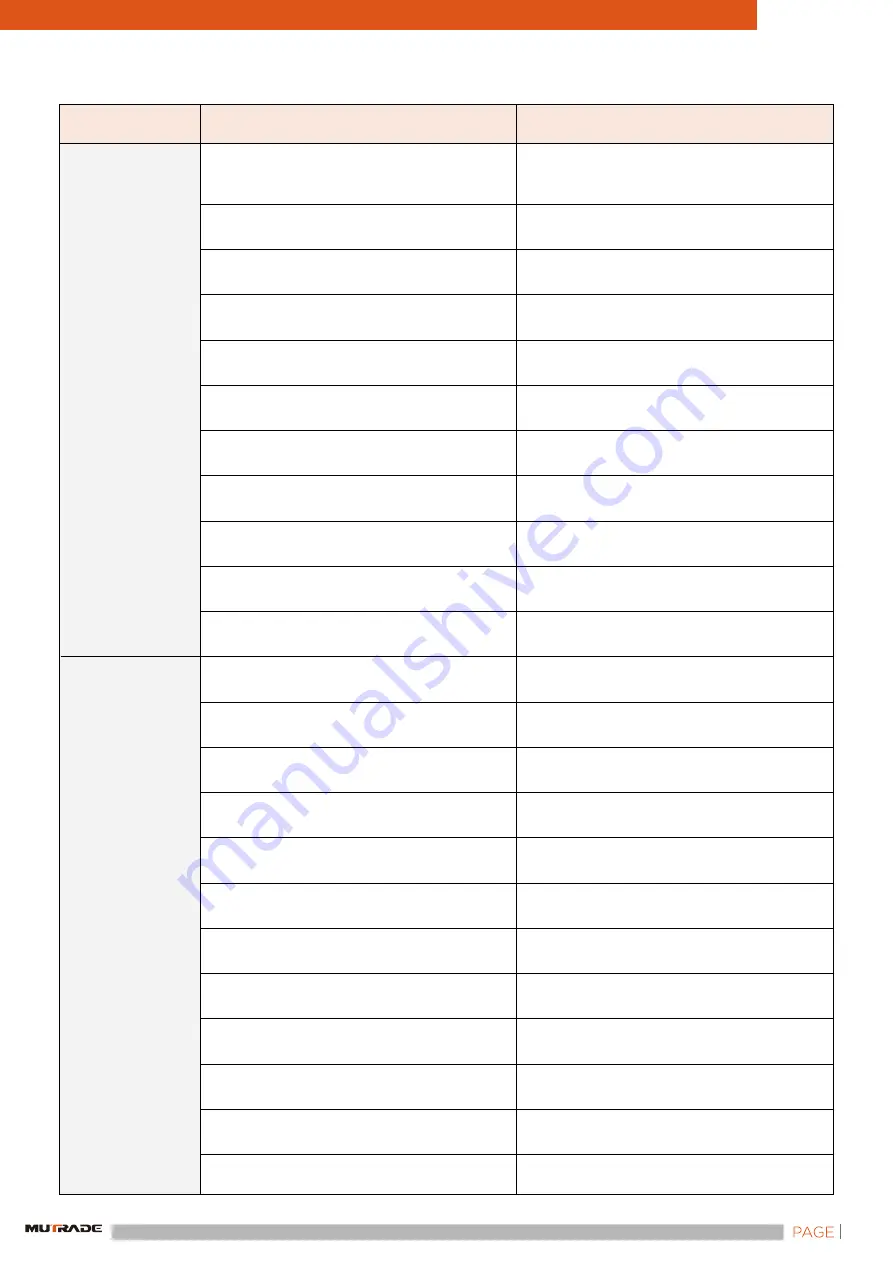
Hydro-Park 1127 & 1123
USER MANUAL
43
MUTRADE INDUSTRIAL CORP.
9.3.3
Servicing of power pack
Trouble
Possible causes
Solutions
Motor is
working, but
cylinder does
not work
The rotation of motor is in wrong
direction due to incorrect motor wiring
Re-connect wires from main power supply
to motor to make motor rotate with
correct direction
Not enough hydraulic oil in oil tank
Broken inlet oil pipe
Inlet oil pipe to be replaced
Broken coupling
Coupling to be replaced
No oil can be pumped out due to blocked
inlet filter
Inlet filter to be cleaned or replaced
Valve element of solenoid valve is blocked
Solenoid valve to be cleaned or replaced
Sealing failure of cushion valve
Cushion valve to be cleaned or replaced
Setting pressure of pressure relief valve
is too low
Turn up setting pressure of pressure relief
valve (with permission of manufacturer)
Emergency depressurizing device of
solenoid valve is not turned off
Turn off emergency depressurizing device
of solenoid valve
Broken gear pump
Gear pump to be replaced
Broken cylinder
Cylinder to be replaced
Hydraulic oil to be replenished into oil tank
Motor is
working, but
platform move
up slowly
Not enough hydraulic oil in oil tank
Hydraulic oil to be replenished into oil
tankCV
Broken inlet oil pipe
Inlet oil pipe to be replaced
fewer oil can be pumped out due to
blocked inlet filter
Inlet filter to be cleaned or replaced
Valve element of solenoid valve is blocked
Solenoid valve to be cleaned or replaced
Sealing failure of cushion valve
Cushion valve to be cleaned or replaced
Valve element of pressure relief valve is
blocked
Pressure relief valve to be cleaned or
replaced
Setting pressure of pressure relief valve
is too low
Turn up setting pressure of pressure
relief valve (with permission of Mutrade)
Hydraulic oil deteriorates or is dirty
Replace hydraulic oil, clean inlet
filter and oil tank
Broken gear pump
Gear pump to be replaced
Broken cylinder
Cylinder to be replaced
Emergency depressurizing device of
solenoid valve is not turned off
Turn off emergency depressurizing device
of solenoid valve
Oil temperature in oil tank is out of
normal range
Stop motor working to cool down hydraulic
oil until it’s in normal temperature