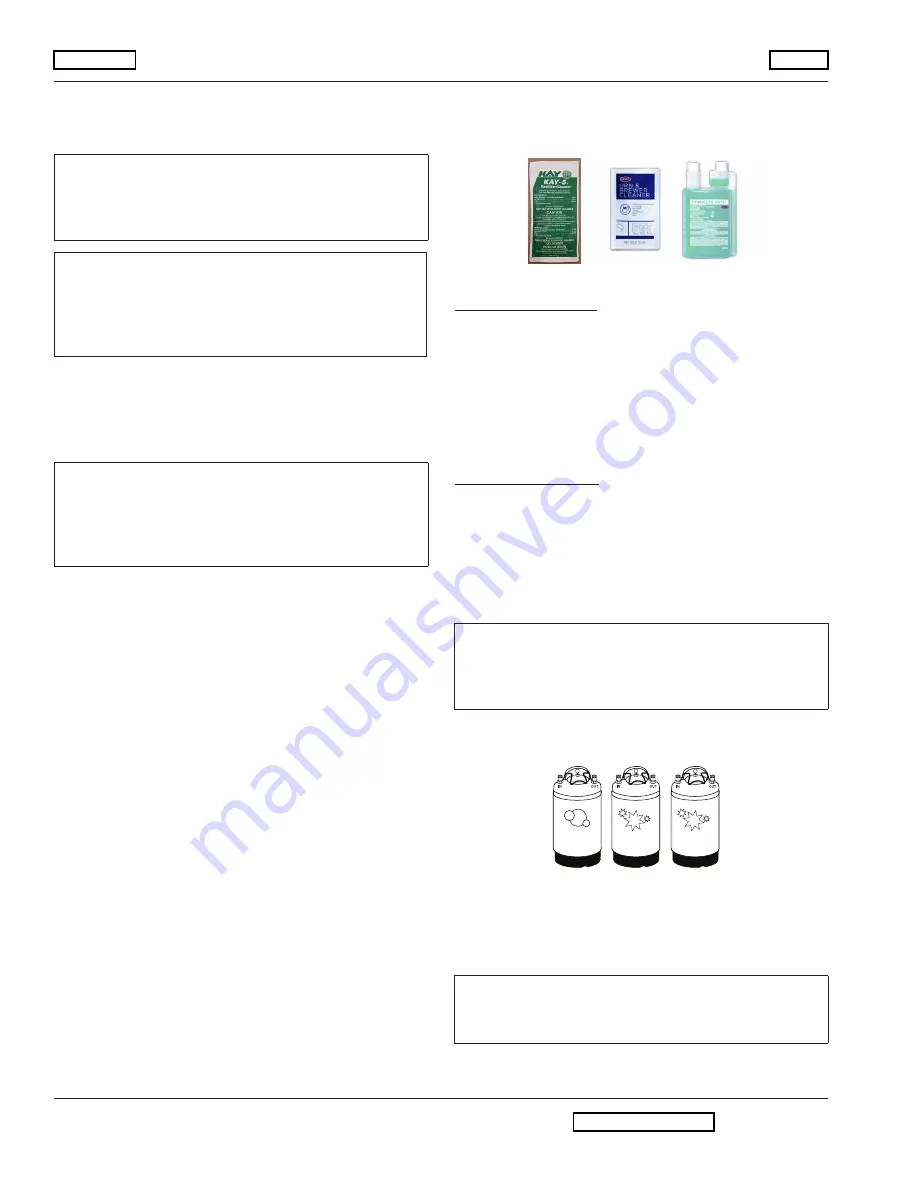
24
Part Number: 9290312 October/22/2018
GENERAL CLEANNG
nteripr Cleaning
Nptice
When cleaning interior and exterior of unit, care should
be taken to avoid the rear power cord. Keep water and/or
cleaning solutions away from electrical parts.
Imprtant
Never use a high-pressure water jet for cleaning or hose
down or flood interior or exterior of units with water. Do
not use power cleaning equipment, steel wool, scrapers
or wire brushes on stainless steel or painted surfaces.
The interior can be cleaned using soap and warm water. If
this isn’t sufficient, try ammonia and water or a nonabrasive
liquid cleaner.
Exteripr Cleaning
,
Cautipn
Never use an acid-based cleaning solution! Many food
products have an acidic content, which can deteriorate
the finish. Be sure to clean the stainless steel surfaces of
ALL food products.
Clean the area around the unit as often as necessary to
maintain cleanliness and efficient operation.
Wipe gasket and surfaces with a damp cloth rinsed in water
to remove dust and dirt from the outside of the unit. Always
rub with the “grain” of the stainless steel to avoid marring
the finish. If a greasy residue persists, use a damp cloth
rinsed in a mild dish soap and water solution. Wipe dry with
a clean, soft cloth.
Never use steel wool or abrasive pads for cleaning. Never
use chlorinated, citrus based or abrasive cleaners.
Stainless steel exterior panels have a clear coating that
is stain resistant and easy to clean. Products containing
abrasives will damage the coating and scratch the panels.
Daily cleaning may be followed by an application of
stainless steel cleaner which will eliminate water spotting
and fingerprints. Early signs of stainless steel breakdown
are small pits and cracks. If this has begun, clean thoroughly
and start to apply stainless steel cleaners in attempt to
restore the steel.
CLEANNG SUPPLES
1. Gather an approved cleaner and sanitizer.
• Only use approved cleaners and sanitizers.
APPROVED CLEANERS
• Urnex® Cafiza® Espresso Machine Cleaner mixed
one (1) teaspoon per gallon, must be used. This
cleaner is compatible with equipment metals
and materials.
• KAY-5® Sanitizer/Cleaner mixed one (1) packet in
2.5 gallons (9.5L) of lukewarm water to equal 100
ppm chlorine. This is also used for the single step
weekly cleaning
APPROVED SANITIZERS
• KAY-5® Sanitizer/Cleaner mixed one (1) packet in
2.5 gallons (9.5L) of lukewarm water to equal 100
ppm chlorine. This is also used for the single step
weekly cleaning
• Quat based Urnex® Complete Cafe’™ mixed 1/2
oz per gallon providing 400 ppm. Used in 3 step
n
Warning
Powdered cleaners and sanitizers must be thoroughly
mixed into water/solution to prevent crystals from
remaining and causing damage to system components.
2. Three (3) clean and sanitized three (3) gallon
(11.36L)
pressure kegs.
• One (1) for cleaning solution.
• Two (2) for sanitizing solution.
NOTE: Only 1 keg will be needed during single step weekly
Imprtant
Kegs used for cleaning, sanitizing solutions and rinse
water should be emptied and cleaned before reuse.