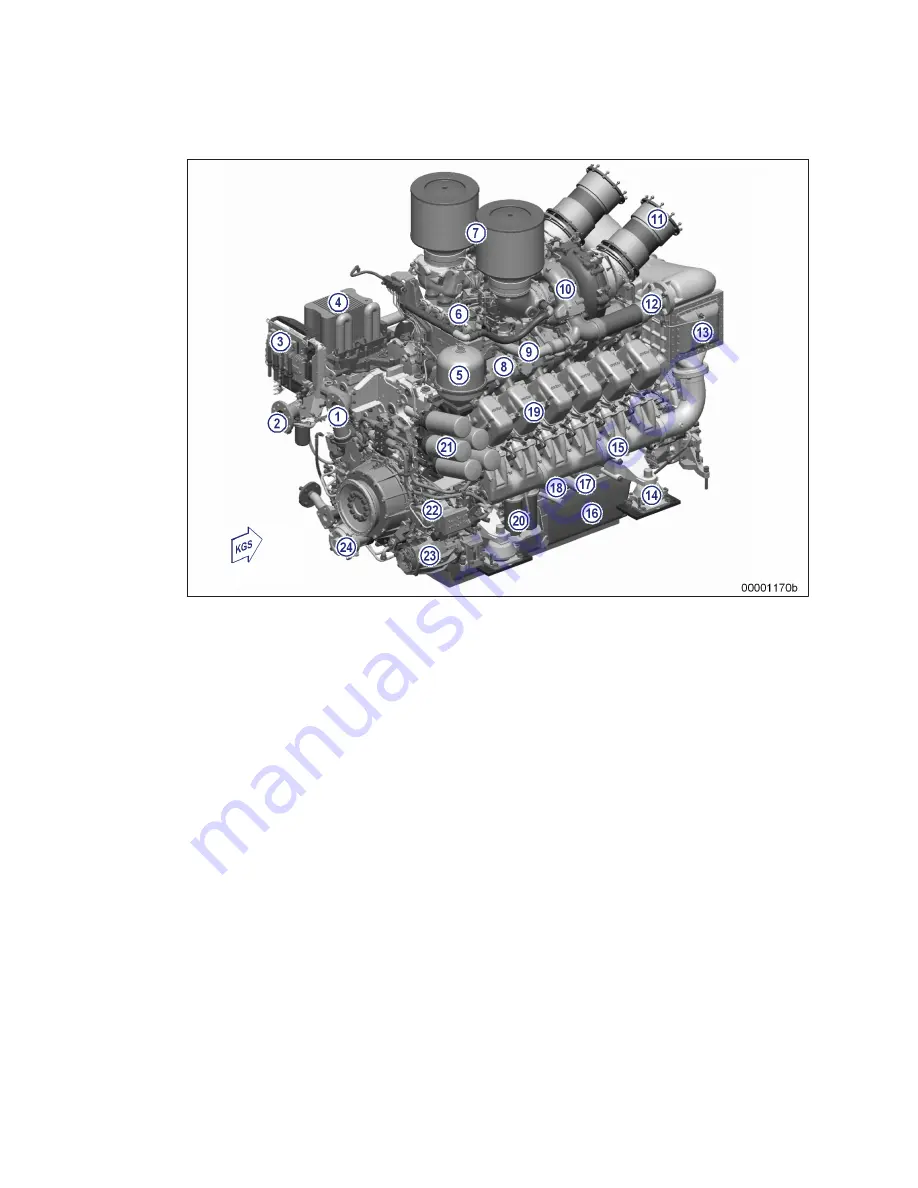
Engines with remote heat exchanger and vertical air intake
1 Coolant outlet to remote
cooling system
2 Coolant inlet from remote
cooling system
3 Engine management and
monitoring
4 Oil cooler
5 Centrifugal oil filter
6 Crankcase breather
7 Dry-type air filter
8 Exhaust manifold
9 Recirculation line
10 Exhaust turbocharger
11 Exhaust outlet
12 Air pipe to intercooler
13 Intercooler
14 Engine mounts
15 Charge-air line
16 Oil pan
17 Oil filler neck
18 Crankcase
19 Cylinder head
20 Fuel filter
21 Oil filter
22 HP fuel pump
23 Battery-charging generator
24 Bilge pump (option)
KGS Free end
Overview drawing is also valid for 16V engines.
30 | Product Summary | MS150068/01E 2014-01
TIM-ID: 0000009990 - 007
Summary of Contents for 12 V 4000 M23F
Page 3: ...Commissioning Note ...
Page 4: ......