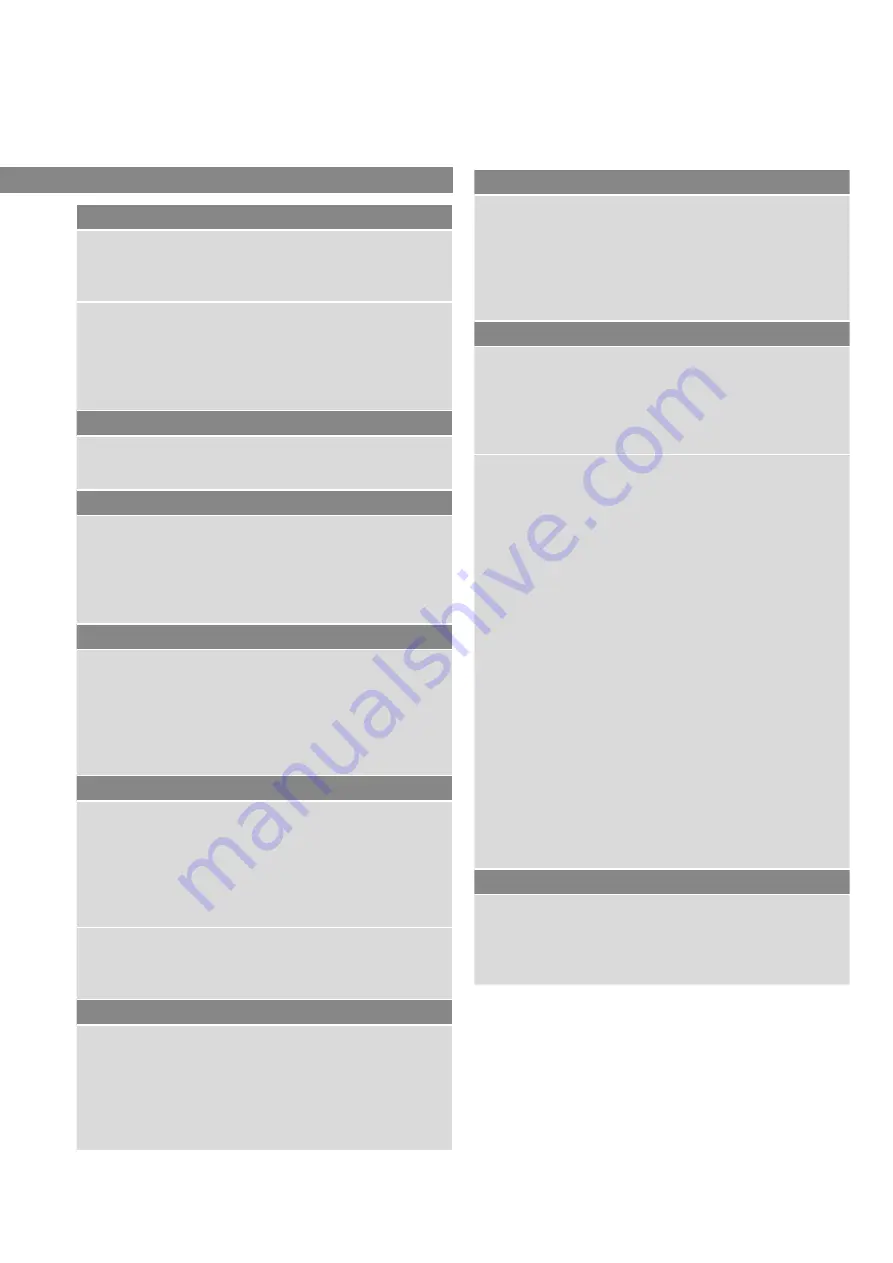
Temposonics
®
R-Series
V
SSI
Operation Manual
11. Glossary
A
Alarm
The alarm bit is set by the sensor if the sensor detects more
magnets (extra magnet) or less magnets (magnet status error) than
confi gured.
Asynchronous mode
In asynchronous mode the position data is continuously updated
inside the sensor as quickly as the sensor’s measurement cycle will
allow, independent of the controller. The controller’s loop time will
determine when the sensor’s most recent data is clocked out over
the SSI interface. (
Synchronous mode)
D
Differential measurement
For differential measurement, the distance between the two position
magnets is output as a value.
E
Extrapolation
The native measurement cycle time of a sensor increases with the
stroke length. With extrapolation, the sensor is able to report data
faster than the native cycle time, independent of the stroke length of
the sensor. Without extrapolation, if data is requested faster than the
native cycle time, the last measured value is repeated.
F
FIR Filter
The FIR fi lter (
F
inite
I
mpulse
R
esponse) is used to smooth the
measured position value before output. To determine the output
value, only input values corresponding to the window (fi lter window
size) are used for fi lter calculation. The output value is calculated
from these input values in the form of a moving average value.
(
IIR Filter)
I
IIR Filter
The IIR fi lter (
I
nfi nite
I
mpulse
R
esponse) is used to smooth the
measured position value before output. To determine the output
value, the input values corresponding to the fi lter grade (fi lter win-
dow size) are used for the fi lter calculation. The previous values are
also taken into account when calculating the output value.
(
FIR Filter)
Internal Linearization
The internal linearization offers an improved linearity for an overall
higher accuracy of the position measurement. The internal lineariza-
tion is set for the sensor during production.
M
Measuring direction
When moving the position magnet, the position and velocity values
increase in the measuring direction.
• Forward: Values increasing from sensor electronics housing
to rod end/profi le end
• Reverse: Values decreasing from sensor electronics housing
to rod end/profi le end
P
Parity
The parity bit is a check bit that is added to a bit string to detect
transmission errors. There are even parity and odd parity. With even
parity, the parity bit is set so that the total number of 1-bits in the bit
string including the parity bit is even. In case of odd parity, the total
number of 1-bits in the bit sequence including the parity bit is odd.
Even parity is implemented in the R-Series
V
SSI.
S
Synchronous Serial Interface
SSI (
S
ynchronous
S
erial
I
nterface) is a digital interface where the
data is transferred serially.The interface of R-Series
V
SSI corre-
sponds to SSI industry standard for absolute encoders. Its displace-
ment value is encoded in a 24/25/26 bit binary or gray format and
transmitted as a differential signal in SSI standard (RS-485/RS-422).
Synchronous mode
In synchronous mode the measurement and output of the sensor is
matched to the data request cycle of the controller. The synchronous
mode minimizes the time delay between measurement and output.
The synchronous mode is required for sophisticated motion control
applications. (
Asynchronous mode)
• Synchronous mode 1
Using synchronous mode 1, the sensor determines the controller’s
loop timing and when data is being requested. The sensor then
determines when to start the next measurement cycle so that it will
complete just in time to deliver the freshest data possible.
• Synchronous mode 2
If new position data is required faster than the sensor’s
measurement cycle time, synchronous mode 2 provides
extrapolated data values, calculated on the fl y. A measurement
value will be calculated and output to the controller whenever the
sensor has not yet completed the next measurement cycle.
• Synchronous mode 3
Synchronous mode 3 provides an additional enhancement to
the high speed update feature of synchronous mode 2. For this
mode all measurements values which are output are calculated
to fully compensate for the inherent lag time due to the sensor’s
measurement cycle.
T
Temperature in the sensor electronics housing
The temperature in the sensor electronics housing is measured
in °C. With this option, the transmitted data word has a length of
32 bits, with the highest 8 bits representing the temperature value,
followed by 24 bits for the position value.